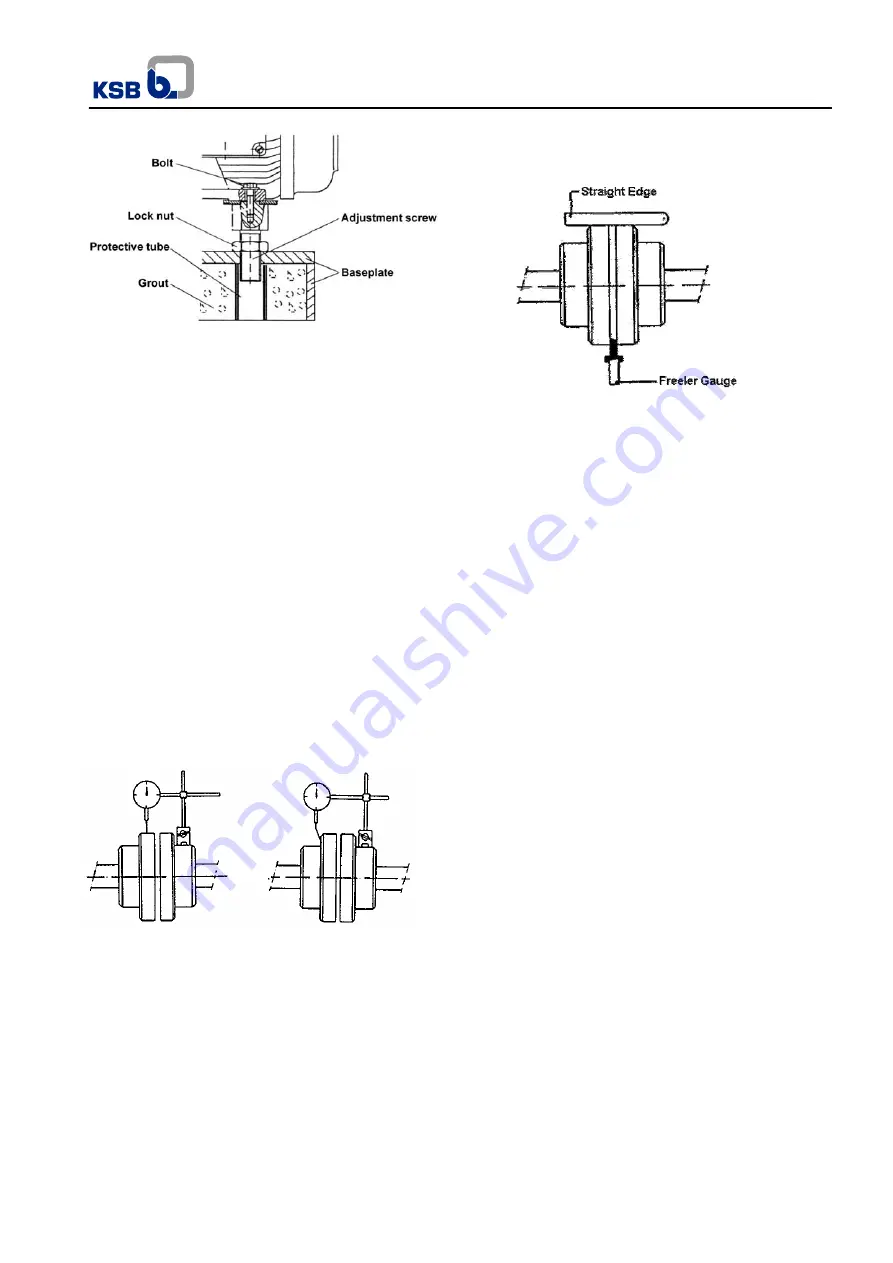
6
Meganorm
Fig. 6b – Grouting inside the baseplates of adjusting screw
type
9.4 Coupling alignment
The useful life of the rotating assembly and its operation free
of irregular vibrations will rely on the perfect alignment
between the pump and the driver.
The alignment performed at the factory must be rechecked
due to the fact that during transportation and handling, the
motor-pump assembly is subjected to deformations, which
may affect the initial alignment.
After the complete set of the grout, perform the alignment, if
possible, with the suction and discharge pipe lines already
connected.
This alignment should be performed with the help of a dial
indicator for the control of the radial and axial displacements.
Fix the button of the instrument to the periphery of one the
coupling halves, adjust the position of the feeler
perpendicular to the periphery of the other half of the
coupling. Move the dial to zero and move manually the
coupling half in which the instrument button is fixed, making
the dial complete a 360 degrees turn. Please see Fig.7.
The same procedure should be performed to control the axial
displacement. Please see Fig.8.
Fig. 7 Fig.8
Radial control Axial control
To correct the alignment, loosen the driver bolts and move
driver laterally or insert shims to adjust height as required.
Axial and radial alignments should remain within a tolerance
of 0.1 mm with the pump and driver set screws tighten
securely.
If there is no dial indicator available, use a straight edge
placed across the two rims of the sleeve coupling. To control
axially use a feeler gauge. Please see Fig. 9. Observe the
sleeve coupling hub clearance specified by manufacturer.
Fig. 9 – Alignment with straight edge and feeler gauge
9.4.1 Motors without adjustment bolts
For the alignment correction, loosen the bolts from the drive
replacing them laterally, or insert shims to correct the height
as required.
9.4.2 Motors with adjustment bolts
To realign the coupling, first loose the four drive bolts, as well
as the lock nuts. Turn the adjustment bolt by hand or with a
tool until the coupling alignment is correct. Retighten the bolts
and respective nuts.
9.5 Suction pipeline – Recommendations
To install the suction piping follow these instructions:
a) Connect the suction piping to the pump only after the
complete hardening of the grout in the base plate.
b) The suction piping should be as straight and short as
possible – reducing pressure losses - and totally air tight,
preventing any air leaks.
c) In order to be free of air pockets, the horizontal section of
the suction piping, when negative, should be installed with
gradual rise slope. When positive, the horizontal section
of the pipeline should be installed with a gradual rise
slope to the suction tank.
d) The nominal diameter of the pump suction flange does not
determine the suction pipe nominal diameter. To calculate
the ideal diameter as a reference, the liquid velocity can
be defined between 3.2 ft/s and 6.5 ft/s (1 and 2 m/s).
e) If it were necessary to use a reduction, it should be
eccentric, mounted with its taper facing downwards, so
that the reduction upper generatrix stays in a horizontal
position coincident with the pump generatrix, so as to
prevent air pockets.