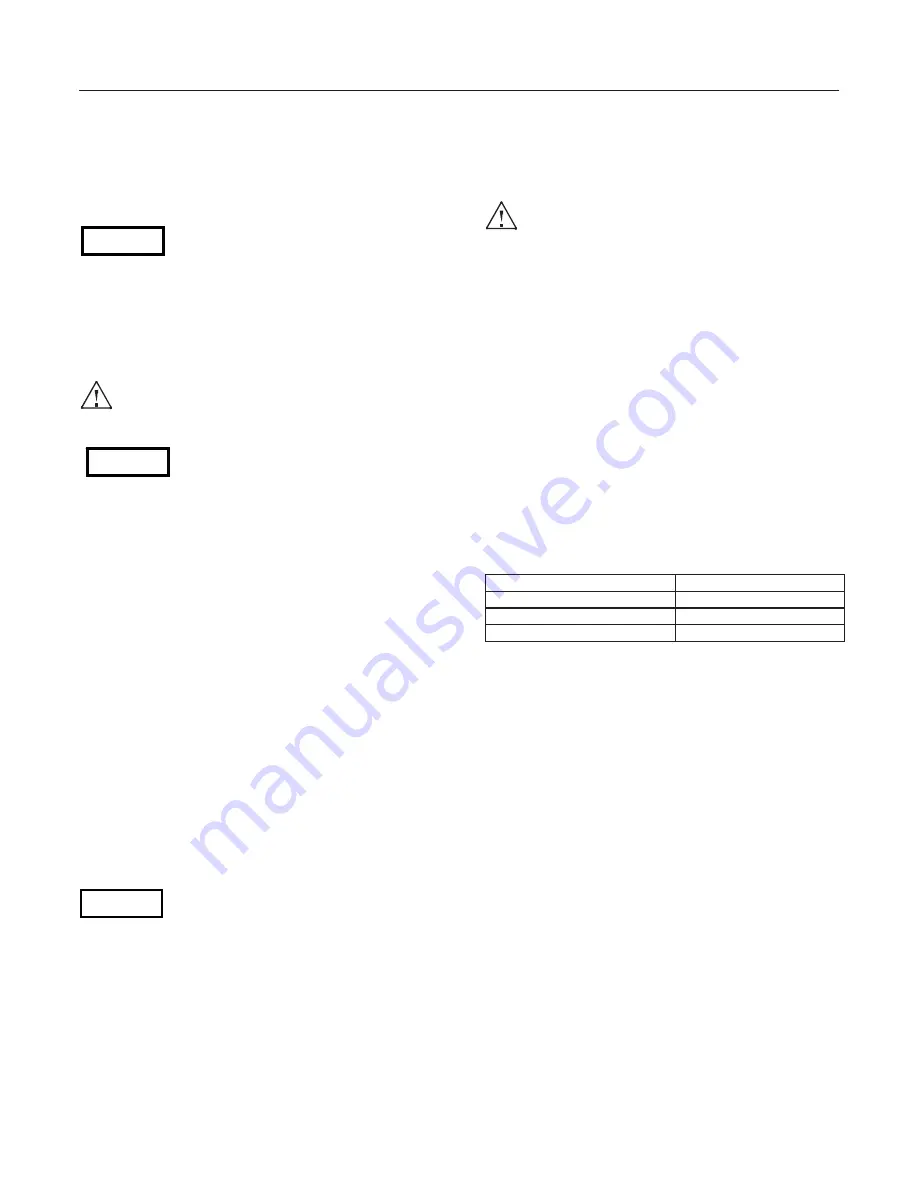
LCC
14
Caution
Caution
6.1.6
Suction Strainer
If a suction strainer has been fitted to protect the pumps
against dirt and/or to retain contamination from the plant;
the strainer’s contamination level must be monitored by
measuring the differential pressure to ensure adequate
inlet pressure for the pump.
6.1.7 Start-up
Before starting the pump ensure that the
shut-off element in the suction line is fully
open. The pump may be started up against a closed
discharge-side swing check valve or shut-off element.
Only after the pump has reached full rotational speed
should the shut-off be opened slowly and adjusted to
comply with the duty point. When starting up against an
open discharge-side shut-off element, take the resulting
increase in input power into account.
Prolonged operation against a closed shut-off
element is not permitted.
Danger of steam
generation and explosion!
Once the operating temperature has
been reached and / or in the event of
leakages, switch off the unit and re-
tighten all bolts. Check the coupling alignment as
described in Section 5.3.1 and re-align, if necessary.
6.1.8 Shutdown
Under no circumstances should the pipe system be
equipped with a check valve or other device that can
rapidly decelerate the flow rate.
Switch off the drive, making sure that the unit runs
smoothly down to a complete stop. Variable
Frequency Drive (VFD) and other controllers must
not use any braking function to slow the pump.
Diesel power trains should disengage the clutch and
allow the pump to coast to a stop.
Close any auxiliary connections. Pressurized
bearing lubrication systems must remain running
until all rotation has stopped. If the any part of the
system uses a cooling liquid supply, turn that off only
after the pump has cooled down. Where liquid filled
shaft seals are used, consult seal maintenance
manual for specific shutdown procedures.
In the event of shutdown where a
significant static discharge head exists
in the system, the impeller can begin to run
backwards as the flow reverses in the pipeline. This
creates a positive torque on the shaft so the impeller
connection will not unscrew. Until the flow stops, do
not close any main line valves. A change in fluid
velocity can create a negative torque on the impeller
and unscrew it from the shaft. This can damage wet
end pump parts as well as bearings, seals and other
components
Where temperatures may drop below freezing, the
pump and system must be drained or otherwise
protected against freezing.
6.2
Operating Limits
The pump’s / unit’s application limits regarding
pressure, temperature and speed are stated on the
data sheet and must be strictly adhered to. If a data sheet
is not available, contact your GIW/KSB representative.
6.2.1
Temperature of the Medium Handled, Ambient
Temperature, Bearing Temperature
Do not operate the pump at temperatures exceeding those
specified on the data sheet or the nameplate unless the
written permission of the manufacturer has been obtained.
Damage resulting from disregarding this warning will not
be covered by the manufacturer’s warranty.
Bearing temperatures, as described in Section 7.2.1, must
be observed. Excessive bearing temperature could
indicate misalignment or other technical problem.
6.2.2
Switching Frequency
To prevent high temperature increases in the motor and
excessive loads on the pump, coupling, motor, seals and
bearings, the switching frequency should not exceed the
following number of start-ups per hour (h):
6.2.3
Density of the Medium Handled
The power input of the pump will increase in proportion to
the density of the medium handled. To avoid overloading
of the motor, pump and coupling, the density of the
medium must comply with the data specified on the
purchase order.
6.3
Shutdown / Storage / Preservation
Each GIW / KSB pump leaves the factory carefully
assembled. If commissioning is to take place some time
after delivery, we recommend that the following measures
be taken for pump storage exceeding 3 months.
6.3.1
Storage of New Pumps
x
Maximum protection for up to 12 months, if the pump
is properly stored indoors.
x
Store the pump in a dry location
x
Rotate the pump rotor by hand once a month.
x
Follow manufacture’s instructions for mechanical
seals.
x
See requirements for rubber liner storage below.
6.3.2
Measures to be taken for Prolonged Shutdown
1 The pump remains installed; operation check run
In order to make sure that the pump is always ready
for instant start-up and to prevent the formation of
deposits within the pump and the pump intake area,
start up the pump set regularly once a month or once
every 3 months for a short time (approx. 5 minutes)
during prolonged shutdown periods. Prior to an
Motor rating
max. switchings / hr
up to 12kW (16hp)
25
up to 100kW (135hp)
20
more than 100kW (135hp)
10
Caution
Содержание GIW LCC 100-400
Страница 27: ...LCC 27 NOTES ...
Страница 34: ......