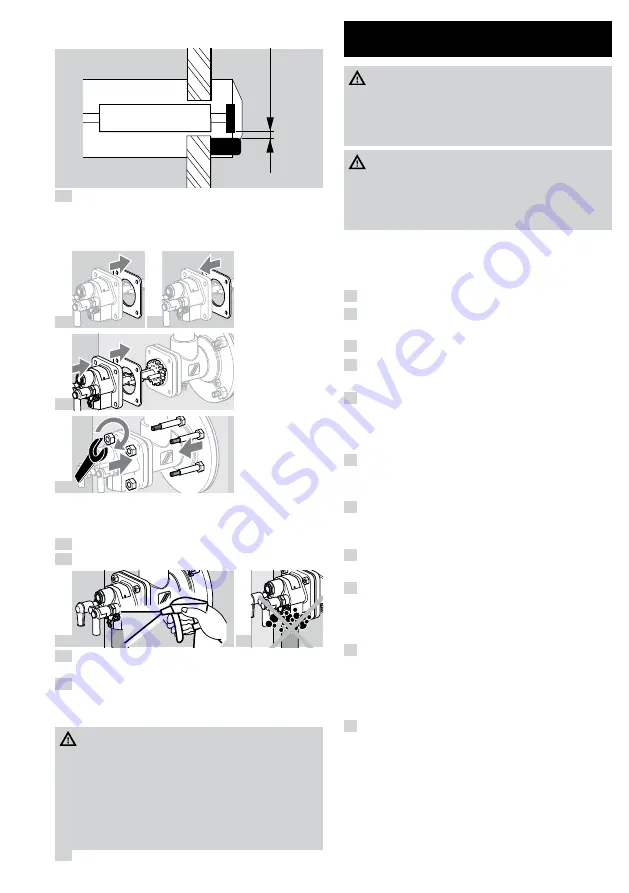
BIO · Edition 09.22
EN-13
➔
Distance of spark electrode from ground pin or gas
nozzle: 2 ± 0.5 mm (0.08 ± 0.02").
2
±
0,5
mm
(0.08
±
0.02
inch)
6
When the furnace chamber has cooled down,
check the burner tube and burner block through
the furnace flange.
➔
Replace the gas housing gasket.
7
8
9
10
➔
Tighten burner insert in a crosswise fashion: BIO(A)
50 to 100 with max. 15 Nm (11 lb ft), BIO 125 to
140 with max. 30 Nm (22 lb ft).
11
Connect the system to the electrical power supply.
12
Open the gas and air supply.
13
14
15
Set the burner to low fire and compare the pressure
settings to those stated in the acceptance report.
16
Set the burner to low and high fire several times
while monitoring the pressure settings, flue gas
values and flame patterns.
DAnGeR
Risk of explosion and poisoning in case of burner
adjustment with insufficient air!
– Adjust the gas and air supply so that the burner
is always operated with excess air – otherwise
CO will form in the furnace chamber. CO is
odourless and poisonous! Conduct a flue gas
analysis.
17
Produce a maintenance report.
8 AssIstAnCe In tHe eVent oF
MALFUnCtIon
DAnGeR
Electric shocks can be fatal!
– Before working on possible live components,
ensure the unit is disconnected from the power
supply.
DAnGeR
Risk of injury!
Burner heads have sharp edges.
– Burner inspection must only be performed by
authorized trained personnel.
➔
If no issues are found when checking the burner,
proceed to the automatic burner control unit and
check for faults in accordance with the relevant
operating instructions.
? Fault
!
Cause
• Remedy
? Burner does not function.
!
Valves do not open.
• Check the voltage supply and wiring.
!
Tightness control signals a fault.
• Check the valves for tightness.
• Note the tightness control operating instruc-
tions.
!
Control valves do not move to low-fire rate posi-
tion.
• Check the impulse lines.
!
Gas inlet pressure is too low.
• Check the filter for dirt.
• Check the gas supply.
!
Air inlet pressure is too low.
• Check the fan and air supply.
!
Gas and air pressures on the burner are too low.
• Check the restrictors.
• Check/adjust the start rate setting, see operat-
ing instructions for solenoid valve.
!
Automatic burner control unit does not function
correctly.
• Check the device fuse.
• Note the automatic burner control unit operat-
ing instructions.
!
Automatic burner control unit signals a fault.
• Check the ionization cable.
• Check the ionization current. The ionization
current must be at least 5 μA – stable signal.
• Check whether the burner is adequately
grounded.
• Note the automatic burner control unit operat-
ing instructions.