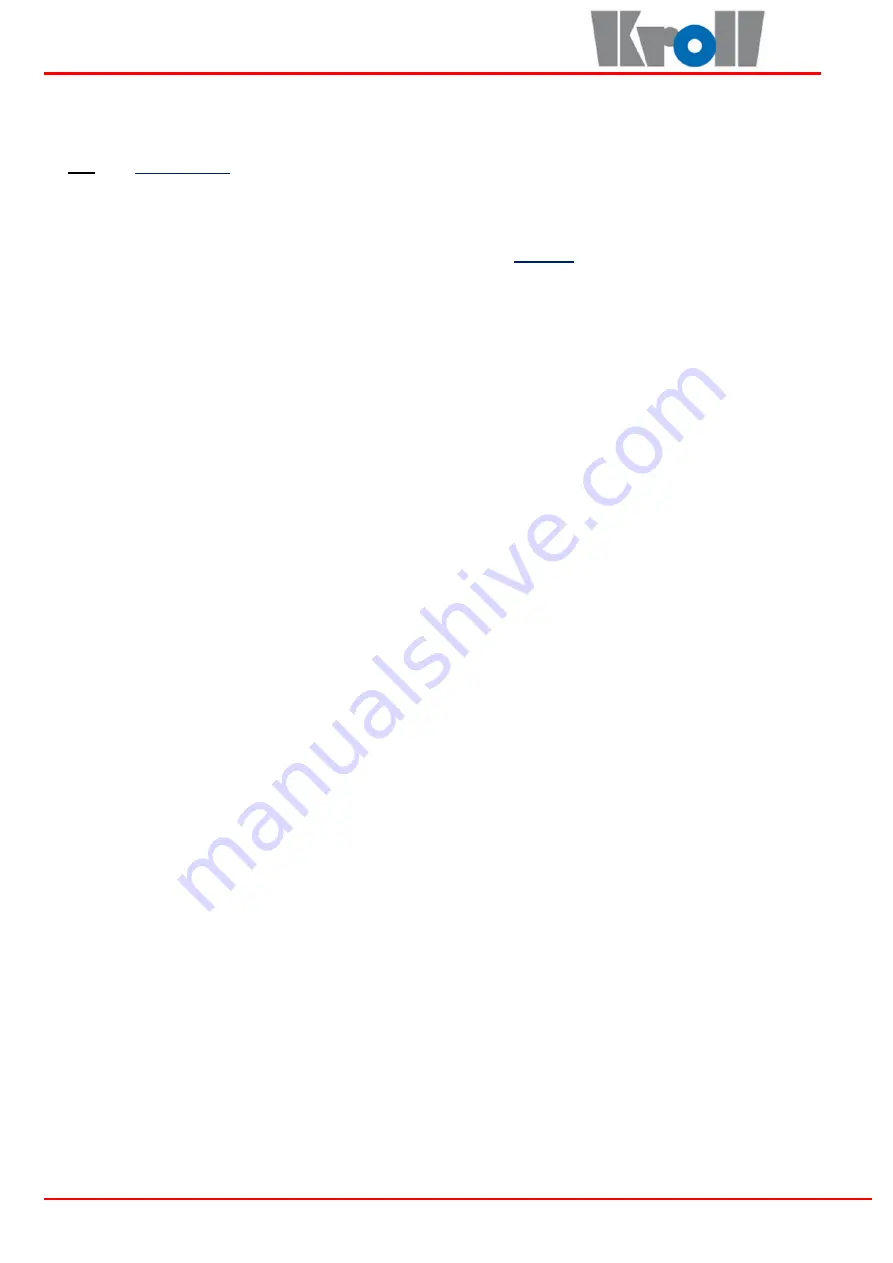
10.
Maintenance
The heater requires little maintenance activity. Following the manufacturer’s recommendations will ensure safe
and failure-free operation of the device:
•
clean the furnace bowl and other combustion chamber elements everyday before firing up. The maximal device
operation time without cleaning the bowl is about 7-12 hours (depending on the employed oil intended for
combustion)
•
check the passability of the overflow pipe (the pipe in the lower part of the combustion chamber, directly over
the overflow bowl), clean if necessary.
•
clean the combustion chamber base (the element under the furnace bowl) at least once a week
•
check whether the air inlet openings in the lower and upper part of the combustion chamber are not blocked
•
clean the rubber duct feeding oil onto the furnace bowl at least once a week
•
clean the fuel tank and oil pump filter during the heating season
•
if the heater is going to be off for a longer time, carefully clean the combustion chamber and the furnace bowl
and protect them against corrosion by coating them with a thin layer of oil
CAUTION!!!
DUE TO EXHAUST DUST ACCUMULATING
IN THE PIPE EXCHANGER, IT IS ADVISABLE TO CLEAN IT AT LEAST ONCE A
YEAR BEFORE THE HEATING SEASON!