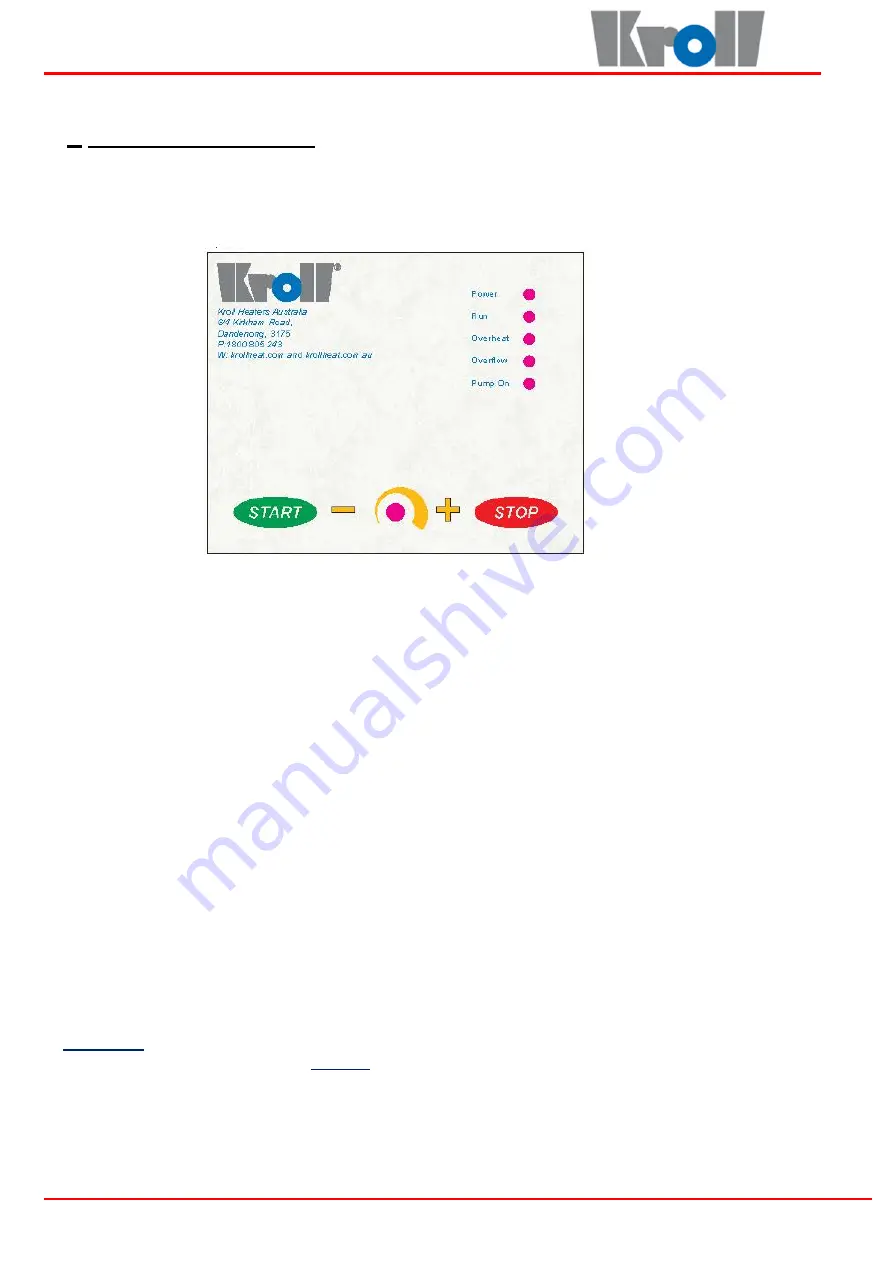
8.
Device operation description
Control panel:
The controller of universal oil heater type MTM 52 is equipped with an adjusting knob and two
switches, stop and start, which enable the user to control the heater operation, and five light emitting diodes [leds]
indicating the operation phase of the device, connected to an alarm in case of a failure.
Fig. 5. The front panel of the control module of the universal oil heater.
Automatic heater shutdown may occur due to overheating or overflow of oil
Overheating is sensed by a bimetallic sensor located on the heat exchanger, see fig6-1. The sensor opens at
100C. The controller thenswitches the pump off, and indicatesthis via blinking red led Overheat on the front panel,
above. Additionally, an alarm is enabled. The heater fan operates until the furnace emperature falls below 35°C.
When this happens, the heater stops.
Then, wait until the heater has cooled down (i.e. the fan has switched off) and press the button on the casing of the
bimetallic sensor. Now pressing the Stop button will cause the Overheat led and the alarm to turn off.
The heater may now be switched on again.
The Overflow signal is generated by a micro-switch located under the overflow tank. The contact opening signals
that the tank has overflowed. The control system switches the pump off, overflowing is signalled by blinking red
led Overflow on the control panel. Additionally, a sound signal is made. The heater fan operates until the furnace
temperature falls below 35°C, and the heater stops.
Then, remove the tank guard located on the side enclosure of the device, empty the overflow tank and press the
Stop button, which will cause the heating led and the sound signal to turn off. The heater may now be switched on
again.
NOTE:
Overheating may occur for a number of reasons such as flue blockage, heat exchanger blockage or using
inappropriate fuel types for the Kozy. Overflow would usually occur due to excess ash being in the combustion
chamber bottom bowl [see fig 6]