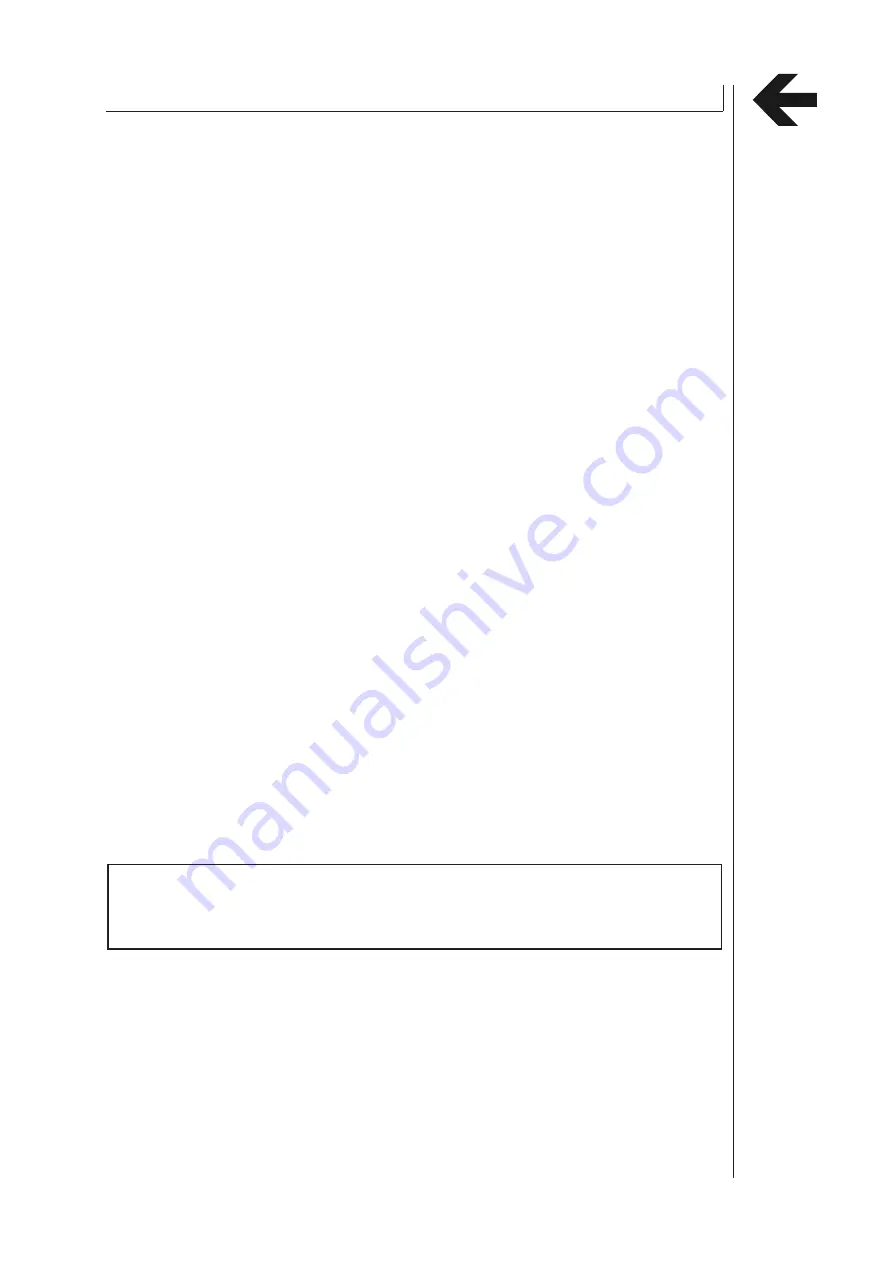
Operating Instructions
17
6
IMPORTANT INFORMATION ON WATER QUALITY
In order to achieve a correct and trouble-free operation on your water chiller it is necessary to
examine the water quality and, when necessary, carry out water treatment. Corrosion, furring and biological
problems can occur in the water system.
The following information is important for the assessment of a half-open system:
- water quality
- all materials having contact with the cooling water
- max. and min. system water temperature
- requirements for water quality
1. Deionized / Demineralized / Destilled / Return Osmosis water
When using deionized, demineralized, destilled or return osmosis water it is required to add a
corrosion inhibitor or glycol to the water system.
2. Fresh water/ City water / Tap water
When using fresh water, city water or tap water it is recommended to analyse the water by a
specialist to minimize the risk of any chiller damage through a high chloride content. A high chloride content
(>20mg/l) in the system water can cause corrosion on the stainless steel evaporator.
It is required to make use of a corrosion inhibitor as additive to the system water. We recommend the use of
Nalco 77382 at a concentration of 5g/l in the complete water system
, unless an Inhibitor with similar characteri-
stics is prescribed from the manufacturer.
Organic sediments and algae in the water cycle can be controlled by analysing the number of organic germs. If
the number of organic germs exceeds 1000 KBE/ml, we recommend to use
Biozid Nalco 77352 at a concentration of 100mg/l
. After 3 to 4 days it is recommended to exchange the
complete system water. The chiller can operate during this period.
Evaporation leads to a concentration of minerals and chloride in the system water, especially at the surface level.
The water parameters which are initially below the guide values, can increase to exceed the guideline value as a
result of the evaporation. An excessive chloride content in the system water will cause corrosion on the stainless
steel evaporators and stainless steel tank. We therefore recommend to regularly monitor the water quality and if
necessary drain the concentrated water from the system in order to rematch the water values to the parameters as
per guideline. It is recommended to exchange the water at least once or more times per year and to inspect the
evaporators on regular intervals.
Water quality parameters:
ph-value:
7-9
alkality
(°dH):
<1
conductivity:
<300 μS/cm
chloride content:
<20 mg/L
hardness (°dH):
<0,1
organic germs:
<1000 KBE/ml
For any further questions please contact the water specialist (S. 1
8
)
Ignorance of the above information cancels the Manufacturers liability for
subsequent damage.
Содержание Chilly
Страница 21: ...20 Operating Instructions FOR YOUR NOTICE ...
Страница 33: ......
Страница 34: ......
Страница 35: ......