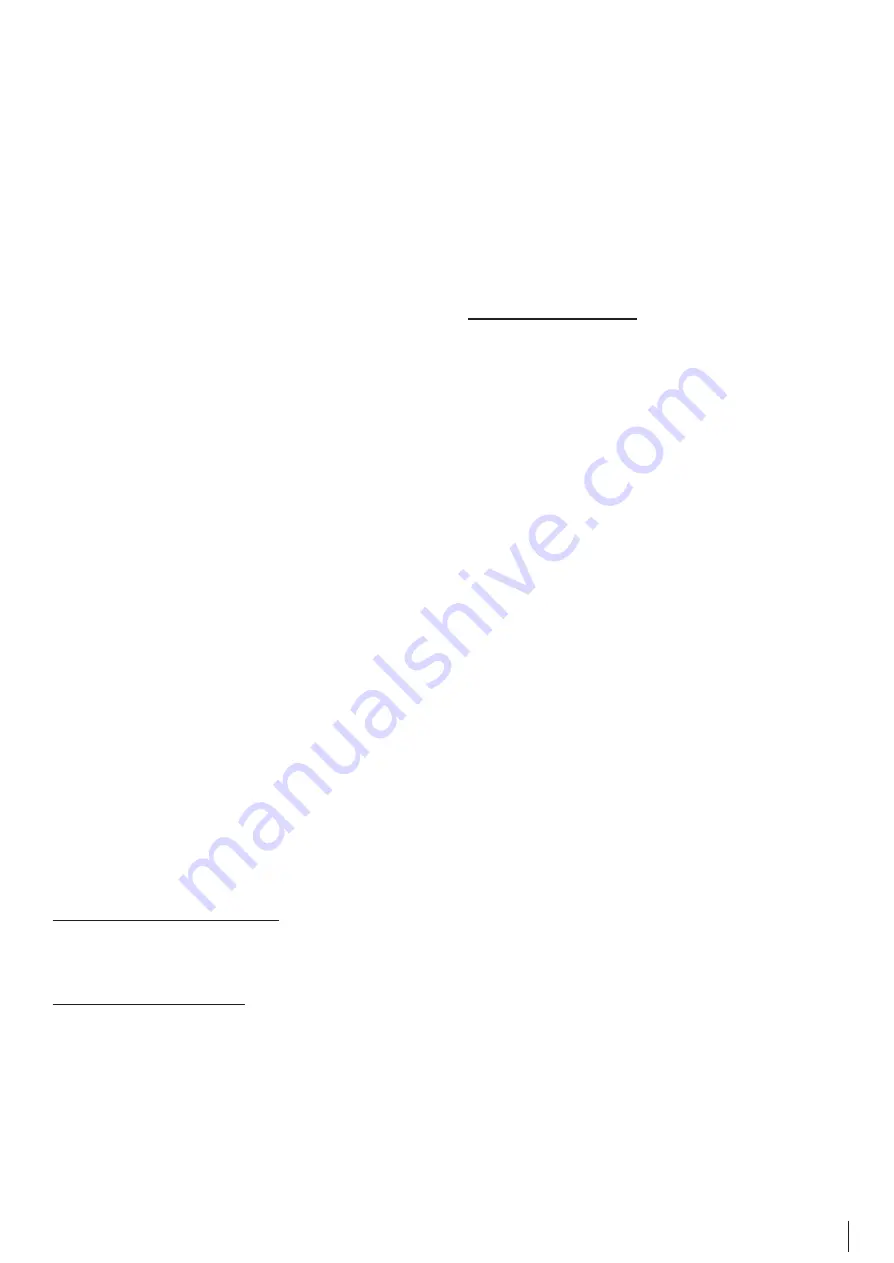
17
• Very sensitive control characteristic: smooth
start-up.
• Sensing and computing of the actual motor data:
self adjusting clock frequency (32 kHz or
higher), dynamic timing.
• Start protection at power up, blocked motor
protection, over temperature protection, over
current limitation.
• Digital microprocessor control: therefore no
thermal drift.
• Please note, that the KOLIBRI ESC is not
PROGCARD compatible.
• Updatable: online firmware update possible.
• 24 months warranty: for items with proof of
purchase.
• CE tested and certified
.
• Fast repair service: in-house service centre.
• Free of charge Hotline (when calling from
Germany): during our daily business hours.
For information to business hours see:
www.kontronik.com (Service-Center)
• Developed and produced in Rottenburg,
Germany.
4.2 Cooling and mounting
Sufficient cooling increases the efficiency and
lifespan of the ESC. When mounting the ESC to the
model, make sure to mount it with the cooling plate
(sticker on the KOLIBRI 60 LV and KOLIBRI 90 LV
upside) facing upward. If using the cooling fan on
the KOLIBRI 140 LV it should be uncovered
.
4.3 BEC / running without BEC
The KOLIBRI ESC has a switched BEC. Compared
to general BEC systems the capacity of the BEC is
designed to be independent of the input voltage.
This allows the usage of the BEC at higher
voltages. In addition, the KOLIBRI features a high
interference rejection.
BEC capacity of KOLIBRI ESC
10 A
continuous
30 A
max peak current
BEC voltage: default 5.6 V
The BEC voltage can be adjusted from 5 V to 9 V
(in 0.1 V steps) by using the programming unit.
For safety reasons, we recommend connecting
either
a 2-cell LiFePo battery
(adjusted BEC voltage:
6,6 V - 7 V)
or a 2-cell LiPo battery
(adjusted BEC voltage: 8
V)
or a 4-cell NiCd battery
(adjusted BEC voltage:
5,6 V)
in parallel to the receiver.
ATTENTION: please ensure the servos and
receiver are compatible with the requested
voltage
Operation without BEC:
When operating without BEC, the red receiver lead
is to be disconnected or removed.
4.4 Active freewheeling circuit
To optimize the efficiency of partial load operation
and to reduce heating of the ESC, the KOLIBRI
features an active freewheeling circuit. The active
freewheeling circuit should not be used at very low
throttle settings as this may result in discontinuity
of motor RPM.
4.5 Part load capability
Due to its active freewheeling circuit, the ESC may
be operated in partial load conditions if you do not
exceed the
KOLIBRI’s continuous current limits
during operation.
4.6 Sensorless Commutation
KOLIBRI ESCs work without sensors inside the
motor via a 3D recognition system. Commutation
of the motor will automatically be optimized for the
application.
4.7 Variable clock frequency
The KOLIBRI ESC uses a clock frequency of
32 kHz, or higher. Depending on the operational
parameters,
clock
frequency
is
adjusted
automatically. The actual frequency depends on
the motor and the actual load. The frequency is
tuned perfectly to the current parameters.
Therefore, the motor is always running at the
highest possible efficiency.
4.8 Protective functions
In the KOLIBRI ESC, the following protective
functions are automatically active:
• If a valid receiver signal is not received within 2
seconds the controller shuts down the motor.
Shut down time is adjustable via the
programming unit.
• In APM and glide mode, overheating of the esc
initiates an automatic decrease of the motor
RPM ending in a complete power-off of the
motor.
!
Содержание KOLIBRI 140 LV
Страница 14: ...14 ...