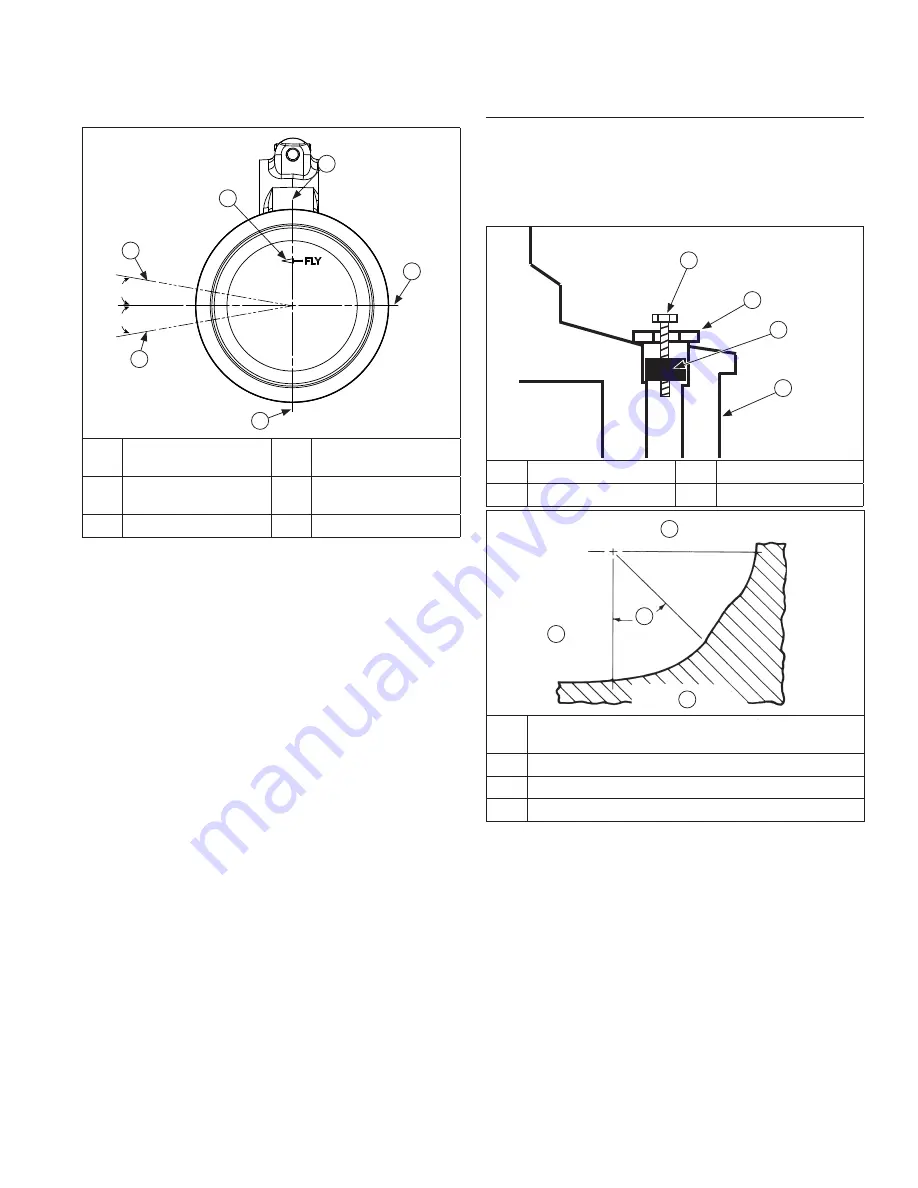
Disassembly/Inspection and Service
83
19 690 01 Rev. --
KohlerEngines.com
Install New Piston Rings
Piston Ring Orientation
10°
10°
F
A
B
C
D
E
A
Top Oil Ring Rail
Gap
B
Bottom Oil Ring Rail
Gap
C
Intermediate Ring
Gap
D
Oil Ring Expander
Gap
E
Top Ring Gap
F
FLY Stamp
NOTE: Rings must be installed correctly. Ring
installation instructions are usually included with
new ring sets. Follow instructions carefully. Use
a piston ring expander to install rings. Install
bottom (oil control) ring
fi
rst and top
compression ring last.
To install new piston rings, proceed as follows:
1. Oil control ring (bottom groove): Install expander and
then rails. Make sure ends of expander are not
overlapped.
2. Middle compression ring (center groove): Install
center ring using a piston ring installation tool. Make
sure identi
fi
cation mark is up or colored dye stripe (if
contained), is to left of end gap.
3. Top compression ring (top groove): Install top ring
using a piston ring expander. Make sure
identi
fi
cation mark is up or colored dye stripe (if
contained), is to left of end gap.
Remove Crankshaft
NOTE: If crankpin is reground, visually check to ensure
that
fi
llet blends smoothly with crankpin surface.
Carefully pull crankshaft from crankcase. Note thrust
washers and shims if used.
Inspection and Service
Crankshaft Components and Details
A
Self-Tapping Screw
B
Flat Washer
C
Plug
D
Crankshaft
A
B
C
D
E
Fillet Must Blend Smoothly with Bearing Journal
Surface
F
High Point from Fillet Intersections
G
45° Minimum
H
This Fillet Area Must Be Completely Smooth
E
G
F
H
Inspect gear teeth of crankshaft. If teeth are badly worn,
chipped, or some are missing, replacement of crankshaft
will be necessary.
Inspect crankshaft bearing surfaces for scoring,
grooving, etc. Measure running clearance between
crankshaft journals and their respective bearing bores.
Use an inside micrometer or telescoping gauge to
measure inside diameter of both bearing bores in vertical
and horizontal planes. Use an outside micrometer to
measure outside diameter of crankshaft main bearing
journals. Subtract journal diameters from their respective
bore diameters to get running clearances. Check results
against values in Speci
fi
cations. If running clearances
are within speci
fi
cation, and there is no evidence of
scoring, grooving, etc., no further reconditioning is
necessary. If bearing surfaces are worn or damaged,
crankcase and/or oil pan will need to be replaced.