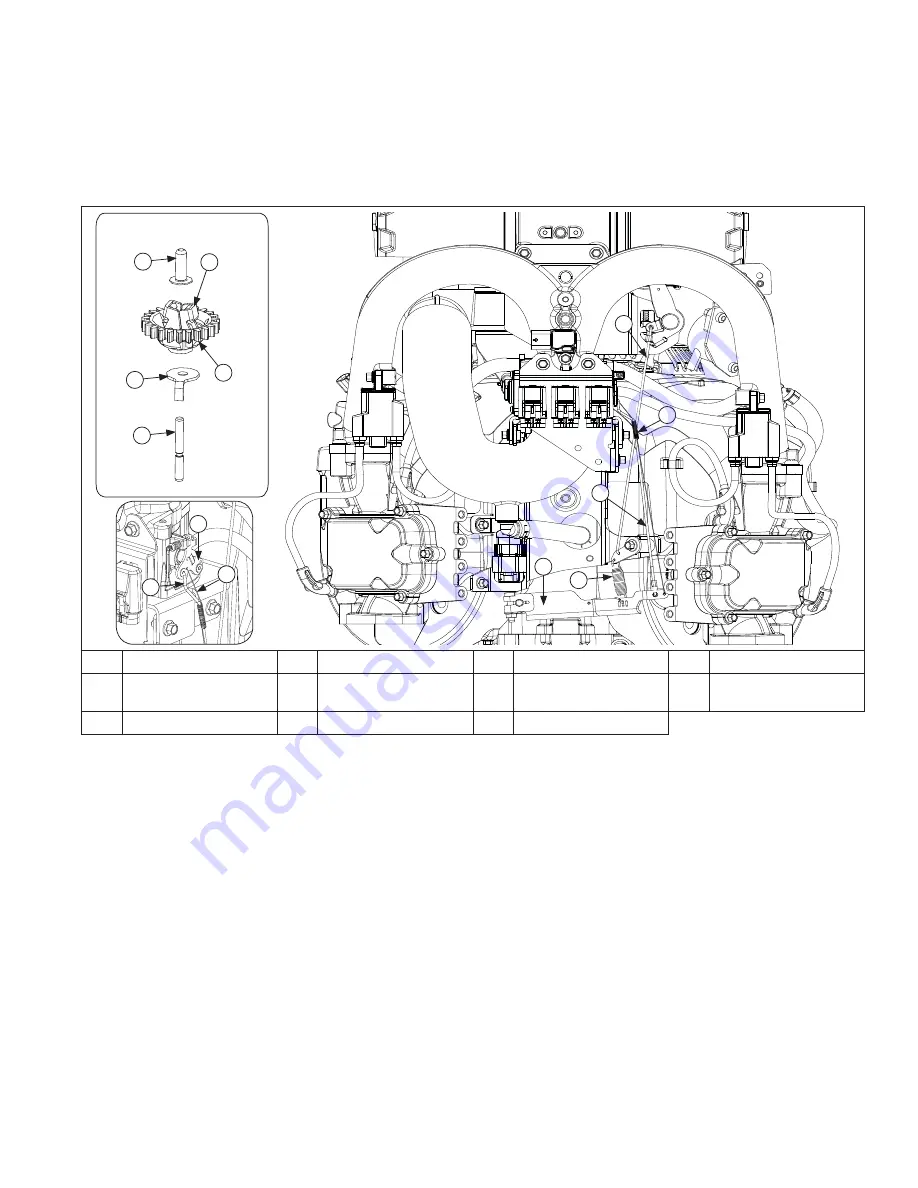
Governor System
57
19 690 01 Rev. --
KohlerEngines.com
MECHANICAL GOVERNOR
Governed speed setting is determined by position of throttle control. It can be variable or constant, depending on
engine application.
Governor is designed to hold engine speed constant under changing load conditions. Governor gear/
fl
yweight
mechanism is mounted inside oil pan and is driven off gear on camshaft.
Components
C
C
E
A
D
F
Inside Engine
J
I
K
G
H
D
B
A
Governor Lever
B
Governor Spring
C
Governor Linkage
D
Linkage Spring
E
Speed Control
Linkage
F
Throttle Lever
G
Governor Gear Shaft
H
Locking Tab Thrust
Washer
I
Governor Gear
J
Flyweight
K
Regulating Pin
This governor design works as follows:
●
Centrifugal force acting on rotating governor gear assembly causes
fl
yweights to move outward as speed
increases. Governor spring tension moves them inward as speed decreases.
●
As
fl
yweights move outward, they cause regulating pin to move outward.
●
Regulating pin contacts tab on cross shaft causing shaft to rotate.
●
One end of cross shaft protrudes through crankcase. Rotating action of cross shaft is transmitted to throttle lever of
throttle body through external linkage.
●
When engine is at rest, and throttle is in FAST position, tension of governor spring holds throttle plate open. When
engine is operating, governor gear assembly is rotating. Force applied by regulating pin against cross shaft tends to
close throttle plate. Governor spring tension and force applied by regulating pin balance each other during
operation, to maintain engine speed.
●
When load is applied and engine speed and governor gear speed decreases, governor spring tension moves
governor lever to open throttle plate wider. This allows more fuel into engine, increasing engine speed. As speed
reaches governed setting, governor spring tension and force applied by regulating pin will again offset each other to
hold a steady engine speed.