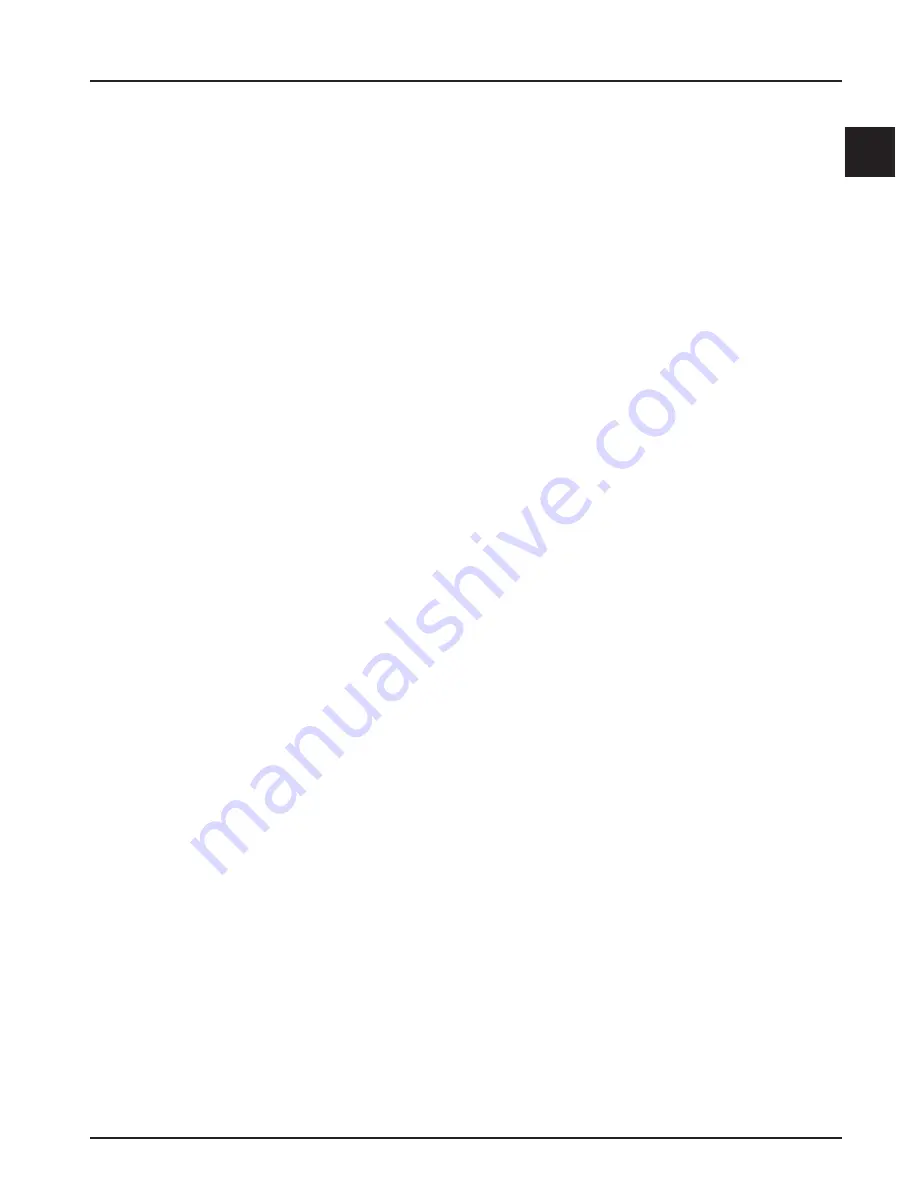
1.17
Section 1
Safety and General Information
1
Muffl er
Exhaust Screw Torque
CH270 (M8) ............................................................................................... 24 N·m (212 in. lb.)
CH395,CH440 (M10) ................................................................................ 35 N·m (310 in. lb.)
Mu
ffl
er Shield Screw Torque (M6) ............................................................... 8 N·m (71 in. lb.)
Mu
ffl
er Shield Screw Torque (M4)
CH270 ........................................................................................................ 2 N·m (18 in. lb.)
CH395,CH440 ........................................................................................... 3.5 N·m (31 in. lb.)
Spark Arrestor Screw Torque (M5) ............................................................... 3.5 N·m (31 in. lb.)
Piston, Piston Rings, and Piston Pin
Piston-to-Piston Pin Running Clearance
CH270 ........................................................................................................ 0.009/0.016 mm (0.0003/0.0006 in.)
CH395,CH440 ........................................................................................... 0.002/0.016 mm (0.0001/0.0006 in.)
Piston Pin Bore I.D.
New
CH270
................................................................................................. 18.004/18.005
mm
(0.7088/0.7089 in.)
CH395
................................................................................................. 18.000/18.008
mm
(0.7087/0.7090 in.)
CH440
................................................................................................. 20.000/20.008
mm
(0.7874/0.7877 in.)
Max. Wear Limit
CH270,CH395 .................................................................................... 18.05 mm (0.7106 in.)
CH440
CH440 .................................................................................................
................................................................................................. 20.05 mm (0.7894 in.)
20.05 mm (0.7894 in.)
Piston Pin O.D.
New
CH270,CH395
.................................................................................... 17.992/17.995
mm
(0.7083/0.7084 in.)
CH440
................................................................................................. 19.992/19.998
mm
(0.7871/0.7873 in.)
Max. Wear Limit
CH270,CH395 .................................................................................... 17.95 mm (0.7067 in.)
CH440 ................................................................................................. 19.95 mm (0.7854 in.)
Top and Center Compression Ring Side Clearance
New
Bore
CH270 ................................................................................................. 0.04 mm (0.002 in.)
CH395 ................................................................................................. 0.07 mm (0.003 in.)
CH440
CH440 .................................................................................................
................................................................................................. 0.045 mm (0.0018 in.)
0.045 mm (0.0018 in.)
Used Bore (Max.)
CH270 ................................................................................................. 0.15 mm (0.006 in.)
CH395 ................................................................................................. 0.11 mm (0.004 in.)
CH440 ................................................................................................. 0.10 mm (0.004 in.)
Top Compression Ring End Gap
New
Bore
CH270 ................................................................................................. 0.325/0.400 mm (0.013/0.016 in.)
CH395,CH440 .................................................................................... 0.250/0.400 mm (0.010/0.016 in.)
Used Bore (Max.)...................................................................................... 1.00 mm (0.039 in.)
Содержание Command PRO CH270
Страница 1: ...SERVICE MANUAL HORIZONTAL CRANKSHAFT CH270 CH395 CH440 ...
Страница 2: ......
Страница 4: ......
Страница 26: ...1 22 Section 1 Safety and General Information ...
Страница 52: ...6 4 Section 6 Lubrication System ...
Страница 70: ...8 14 Section 8 Electrical System and Components ...
Страница 86: ...9 16 Section 9 Disassembly ...
Страница 124: ...11 26 Section 11 Reassembly ...
Страница 125: ......