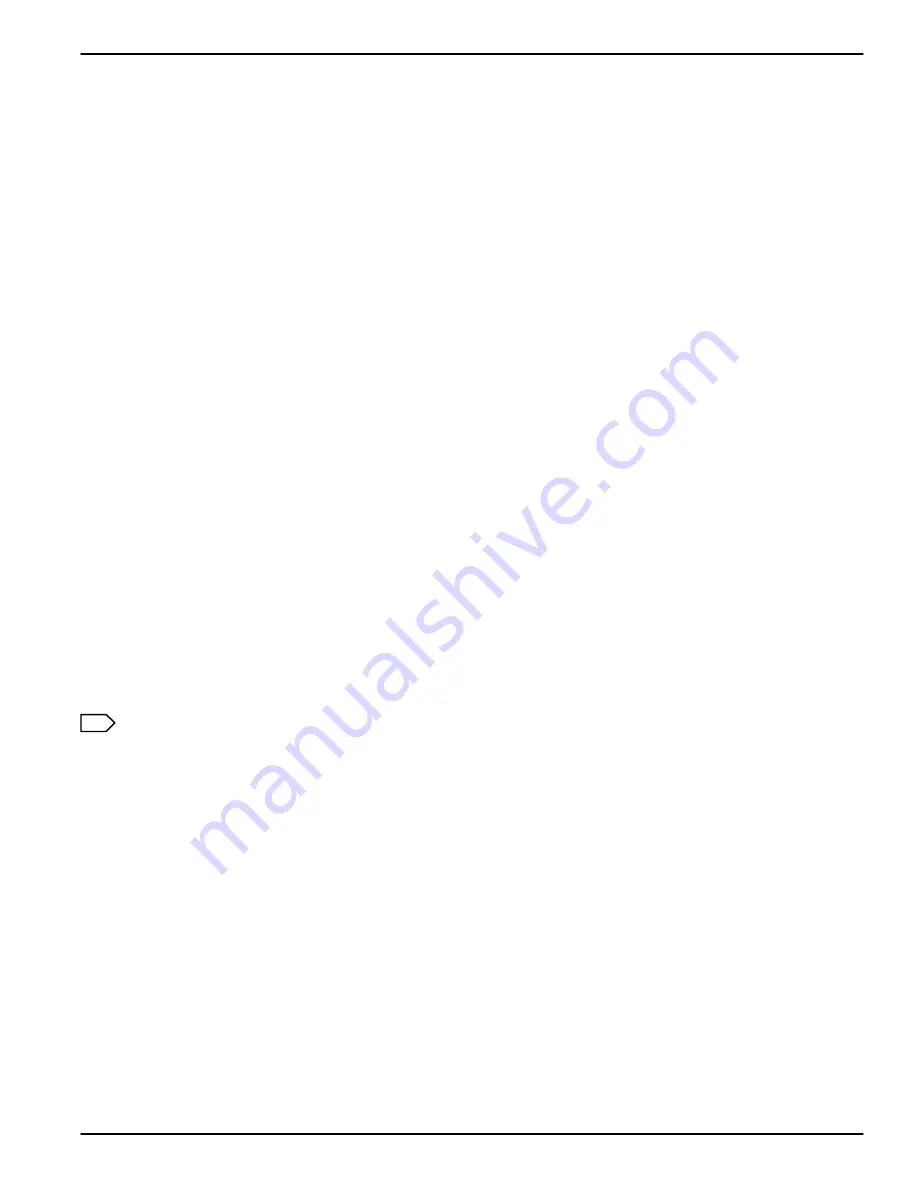
Section 6 -- Theory of Operation
6-29
2005 July Rev. B 7F3318
6-4-6-2.
Sensor Control
The Feeder Control Board receives status from the following 8 sensors:
•
Pickup Position Sensor, which indicates that the pickup arm is in its home (top) position.
•
Film Surface Sensor, which signals that the pickup arm has moved to the position where the sensor
contacts the film surface.
•
Film Out Sensor, which indicates (after the pickup arm has moved down) whether the cartridge is out
of film.
•
Cups Engaged Sensor, which indicates that the suction cups have rotated down to engage the film.
•
Feed Roller Open Sensor, which indicates whether the feed rollers are open or closed.
•
Cartridge Present Sensor, which indicates that a film cartridge is loaded.
•
Rollback Home Sensor, which indicates that the film cartridge is closed.
•
Elevator Home Sensor, which indicates that the elevator is in the home (lowered) position.
All 8 sensors are identical electronically and have the same pinout configuration. Since the sensors are
the infrared type, and thus have the potential of exposing film, the Slave CPU switches them off and on as
needed by means of the SENSOR CONTROL line. When this line is low, the sensors are off. To read
sensor status, the CPU sets the line high, providing a ground for the sensor circuits through Q1. All the
sensors operate with the same “sense”: When a sensor is blocked (i.e., no light is reaching the detector
side), the output of the sensor is a logic 0 (low).
As shown on sheet 2 of the 8150 Functional Diagrams, the Feeder Control Board contains 2 jumper plugs
for use by a service technician. (Functional Diagrams are on the
Kodak
Health Imaging Digital Output
Service Collection CD set.)
The jumper on plug JP3 will provide a “full time” ground for the sensor circuits if placed in the SENSORS
ON position (bypassing CPU control). Also, the jumper on plug JP2 can be used to activate the 8 LEDs
on the board for troubleshooting purposes. Each sensor input line to the CPU includes an LED. When a
particular sensor is blocked (not conducting), its corresponding LED will turn on if jumper JP3 is in the
SENSORS ON position.
Note
Following service use, the jumpers must be removed from the service position and stored in the
“normal” position on the jumper plugs, for normal machine operation.
6-4-6-3.
Film Pickup and Feed Functions
The MCS software that controls film pickup and feed through the MicroComm interface implements the
following commands:
Start Pickup
----This command initiates the following sequence:
1. Check the following items before moving the pickup arm:
•
The pickup arm is home (Pickup Position Sensor).
•
Pickup and feed diagnostics have passed.
•
No other operations are in process.
•
A film cartridge is present (Cartridge Present Sensor)
•
The cartridge has been rolled back (Rollback Home Sensor).
•
The cartridge elevator is lowered (Elevator Home Sensor).
Содержание DryView 8150
Страница 1: ...SERVICE MANUAL Kodak DryView 8150 LASER IMAGER 1961259 7F3318 07 05 ...
Страница 20: ...Service Manual 1 6 7F3318 2005 July Rev B BLANK PAGE ...
Страница 34: ...Service Manual 2 14 7F3318 2005 July Rev B 6 Remove the 2 SCREWS and 2 TAGS 6 ...
Страница 50: ...Service Manual 2 30 7F3318 2005 July Rev B 6 Check each parameter ...
Страница 91: ...Section 2 Installation 2 71 2005 July Rev B 7F3318 BLANK PAGE ...
Страница 105: ...Service Manual 3 14 7F3318 2005 July Rev B BLANK PAGE ...
Страница 167: ...Service Manual 4 62 7F3318 2005 July Rev B 7 Troubleshoot image problems if necessary See Section 7 ...
Страница 182: ...Section 4 Disassembly Reassembly 4 77 2005 July Rev B 7F3318 BLANK PAGE ...
Страница 196: ...Service Manual 5 14 7F3318 2005 July Rev B Figure 5 9 Cleaning the HEAT SHIELD and ROLLERS ...
Страница 200: ...Service Manual 5 18 7F3318 2005 July Rev B Figure 5 11 Adjusting the DIVERTER ...
Страница 236: ...Service Manual 6 34 7F3318 2005 July Rev B Figure 6 17 Pickup Operation Sheet 1 of 3 ...
Страница 237: ...Section 6 Theory of Operation 6 35 2005 July Rev B 7F3318 Figure 6 17 Pickup Operation Sheet 2 of 3 ...
Страница 238: ...Service Manual 6 36 7F3318 2005 July Rev B Figure 6 17 Pickup Operation Sheet 3 of 3 ...
Страница 239: ...Section 6 Theory of Operation 6 37 2005 July Rev B 7F3318 Figure 6 18 Load Platen Operation Sheet 1 of 2 ...
Страница 240: ...Service Manual 6 38 7F3318 2005 July Rev B Figure 6 18 Load Platen Operation Sheet 2 of 2 ...
Страница 241: ...Section 6 Theory of Operation 6 39 2005 July Rev B 7F3318 Figure 6 19 Expose Operation ...
Страница 242: ...Service Manual 6 40 7F3318 2005 July Rev B Figure 6 20 Unload Platen Operation ...
Страница 243: ...Section 6 Theory of Operation 6 41 2005 July Rev B 7F3318 Figure 6 21 Processor Operation Sheet 1 of 2 ...
Страница 244: ...Service Manual 6 42 7F3318 2005 July Rev B Figure 6 21 Processor Operation Sheet 2 of 2 ...
Страница 245: ...Section 6 Theory of Operation 6 43 2005 July Rev B 7F3318 Figure 6 22 Front Door Open Operation Sheet 1 of 2 ...
Страница 246: ...Service Manual 6 44 7F3318 2005 July Rev B Figure 6 22 Front Door Open Operation Sheet 2 of 2 ...
Страница 247: ...Section 6 Theory of Operation 6 45 2005 July Rev B 7F3318 Figure 6 23 Front Door Close Operation ...
Страница 252: ...Service Manual 6 50 7F3318 2005 July Rev B Figure 6 27 Sequence of AIQC and GSM Functions ...
Страница 288: ...Service Manual 7 36 7F3318 2005 July Rev B 7 4 Next Page 12 075 28 506 01 910 from DRE Figure 7 3 MCS Self Test Startup ...
Страница 292: ...Service Manual 7 40 7F3318 2005 July Rev B Next Page 21 921 21 921 Figure 7 5 FILM FEEDER MODULE Diagnostics Sheet 3 ...
Страница 294: ...Service Manual 7 42 7F3318 2005 July Rev B Prev Page Next Page 29 924 29 924 Figure 7 7 DENSITOMETER MODULE Diagnostics ...
Страница 444: ...Service Manual 8 102 7F3318 2005 July Rev B BLANK PAGE ...
Страница 466: ...Service Manual 9 22 7F3318 2005 July Rev B BLANK PAGE ...
Страница 468: ...Service Manual 10 2 7F3318 2005 July Rev B BLANK PAGE ...
Страница 469: ......