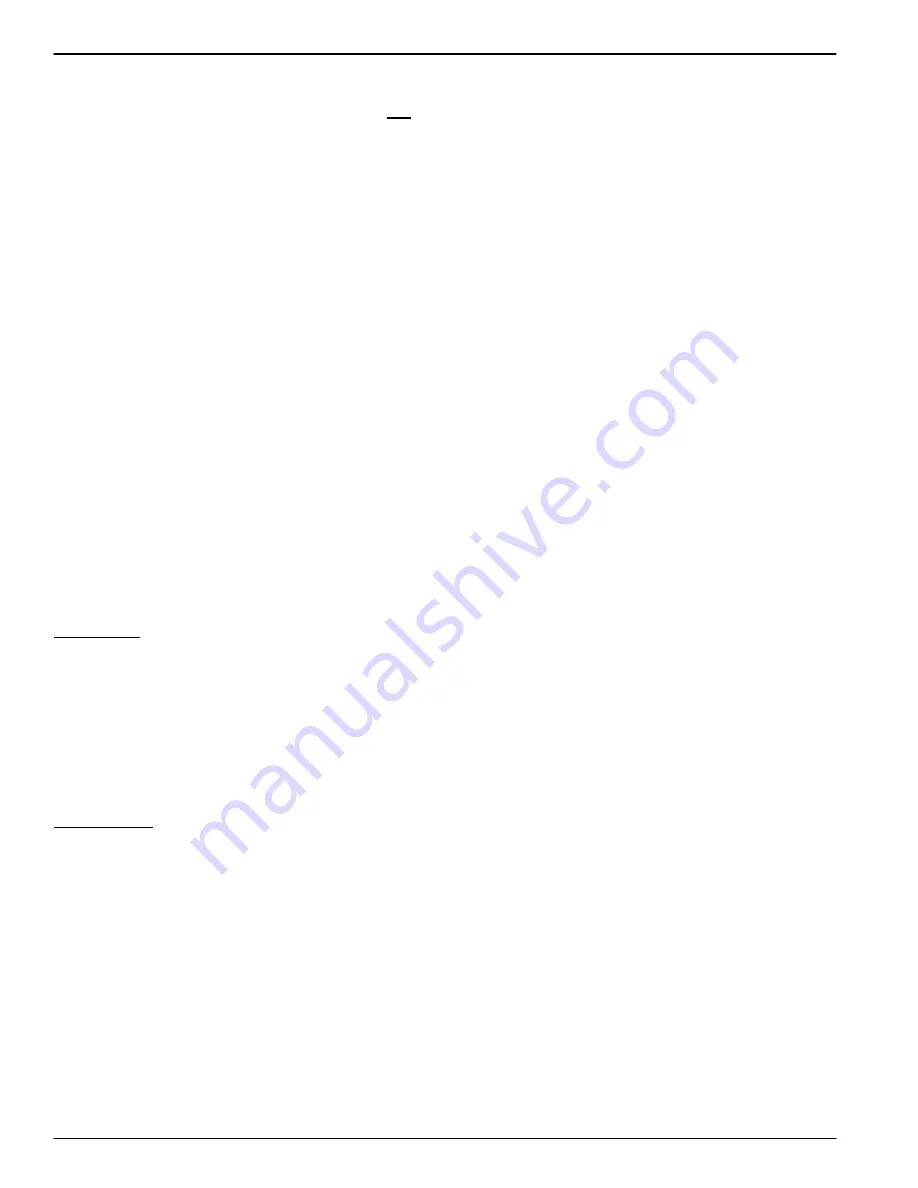
Service Manual
6-14
7F3318 2005 July Rev. B
2. Controls machine subsystems through the MicroComm interface.
3. Controls the following devices which are not on the MicroComm bus:
•
Processor Drum Motor (speed)
•
Processor Drum (temperature)
•
Optics Translation Motor (speed and direction)
•
Platen Feed Motor
•
Platen Centering Motor
•
Front Door Solenoid
•
Safety interlocks
4. Reads the state of the Optics Home Sensor, Platen Film Sensor and Transport Sensor
6-4-2-1.
Master CPU
The Master CPU has general control of all MCS functions. The main resident serial port on the CPU chip
is programmed to talk to 4 slave units on the 9-bit Microcom Interface, as described in paragraph 6-3-1. A
special feature of the CPU allows the creation of UARTs (Universal Asynchronous Receiver/Transmitters)
on its TPU (Time Processing Unit) channels. The integral UARTs allow the CPU to communicate directly
with peripherals, saving the expense of an external UART chip. The current configuration of the MCS
employs only one TPU UART, which is used to communicate with the IMS.
The CPU works with an Address Decoder FPGA to route Chip Select, control, and addressing signals to
other components on the MCS Board. This FPGA extends the CPU’s ability to address and control the
other components of the MCS.
CPU I/O Port Functions
----CPU input and output port functions are defined as follows:
CPU Inputs:
•
Optics Home Sensor----Low when optics is in (or past) the home position.
•
Platen Sensor----High when film is actuating the sensor.
•
Transport Sensor----High when film is actuating the sensor.
•
Processor Temp Frequency In----This is a frequency input that is proportional to the processor
temperature. It is used to monitor temperature.
•
Expose Done----A high pulse at the end of each print.
CPU Outputs:
•
Platen On----When low, enables operation of the Platen Nip Stepper Motor.
•
Platen Phase 1 and Phase 2----These two channels control direction of the Platen Nip Motor by
generating two square waves that are 90 degrees out of phase. Direction depends on which signal
leads the other. If Phase 1 leads, the motor turns in the load direction. If Phase 2 leads, the
direction is opposite (unload).
•
Centering On----When low, turns on the Centering Stepper Motor.
•
Centering Phase 1 and Phase 2----These two channels control direction of the Centering Motor by
generating two square waves that are 90 degrees out of phase. If Phase 1 leads, the motor
operates in the home direction. If phase 2 leads, it operates in the centering direction.
•
Vertical On----When low, turns on the Transport Roller Motor.
•
Vertical Clk----This is a pulse-width modulated signal that controls the stepping rate of the
Transport Roller Motor.
Содержание DryView 8150
Страница 1: ...SERVICE MANUAL Kodak DryView 8150 LASER IMAGER 1961259 7F3318 07 05 ...
Страница 20: ...Service Manual 1 6 7F3318 2005 July Rev B BLANK PAGE ...
Страница 34: ...Service Manual 2 14 7F3318 2005 July Rev B 6 Remove the 2 SCREWS and 2 TAGS 6 ...
Страница 50: ...Service Manual 2 30 7F3318 2005 July Rev B 6 Check each parameter ...
Страница 91: ...Section 2 Installation 2 71 2005 July Rev B 7F3318 BLANK PAGE ...
Страница 105: ...Service Manual 3 14 7F3318 2005 July Rev B BLANK PAGE ...
Страница 167: ...Service Manual 4 62 7F3318 2005 July Rev B 7 Troubleshoot image problems if necessary See Section 7 ...
Страница 182: ...Section 4 Disassembly Reassembly 4 77 2005 July Rev B 7F3318 BLANK PAGE ...
Страница 196: ...Service Manual 5 14 7F3318 2005 July Rev B Figure 5 9 Cleaning the HEAT SHIELD and ROLLERS ...
Страница 200: ...Service Manual 5 18 7F3318 2005 July Rev B Figure 5 11 Adjusting the DIVERTER ...
Страница 236: ...Service Manual 6 34 7F3318 2005 July Rev B Figure 6 17 Pickup Operation Sheet 1 of 3 ...
Страница 237: ...Section 6 Theory of Operation 6 35 2005 July Rev B 7F3318 Figure 6 17 Pickup Operation Sheet 2 of 3 ...
Страница 238: ...Service Manual 6 36 7F3318 2005 July Rev B Figure 6 17 Pickup Operation Sheet 3 of 3 ...
Страница 239: ...Section 6 Theory of Operation 6 37 2005 July Rev B 7F3318 Figure 6 18 Load Platen Operation Sheet 1 of 2 ...
Страница 240: ...Service Manual 6 38 7F3318 2005 July Rev B Figure 6 18 Load Platen Operation Sheet 2 of 2 ...
Страница 241: ...Section 6 Theory of Operation 6 39 2005 July Rev B 7F3318 Figure 6 19 Expose Operation ...
Страница 242: ...Service Manual 6 40 7F3318 2005 July Rev B Figure 6 20 Unload Platen Operation ...
Страница 243: ...Section 6 Theory of Operation 6 41 2005 July Rev B 7F3318 Figure 6 21 Processor Operation Sheet 1 of 2 ...
Страница 244: ...Service Manual 6 42 7F3318 2005 July Rev B Figure 6 21 Processor Operation Sheet 2 of 2 ...
Страница 245: ...Section 6 Theory of Operation 6 43 2005 July Rev B 7F3318 Figure 6 22 Front Door Open Operation Sheet 1 of 2 ...
Страница 246: ...Service Manual 6 44 7F3318 2005 July Rev B Figure 6 22 Front Door Open Operation Sheet 2 of 2 ...
Страница 247: ...Section 6 Theory of Operation 6 45 2005 July Rev B 7F3318 Figure 6 23 Front Door Close Operation ...
Страница 252: ...Service Manual 6 50 7F3318 2005 July Rev B Figure 6 27 Sequence of AIQC and GSM Functions ...
Страница 288: ...Service Manual 7 36 7F3318 2005 July Rev B 7 4 Next Page 12 075 28 506 01 910 from DRE Figure 7 3 MCS Self Test Startup ...
Страница 292: ...Service Manual 7 40 7F3318 2005 July Rev B Next Page 21 921 21 921 Figure 7 5 FILM FEEDER MODULE Diagnostics Sheet 3 ...
Страница 294: ...Service Manual 7 42 7F3318 2005 July Rev B Prev Page Next Page 29 924 29 924 Figure 7 7 DENSITOMETER MODULE Diagnostics ...
Страница 444: ...Service Manual 8 102 7F3318 2005 July Rev B BLANK PAGE ...
Страница 466: ...Service Manual 9 22 7F3318 2005 July Rev B BLANK PAGE ...
Страница 468: ...Service Manual 10 2 7F3318 2005 July Rev B BLANK PAGE ...
Страница 469: ......