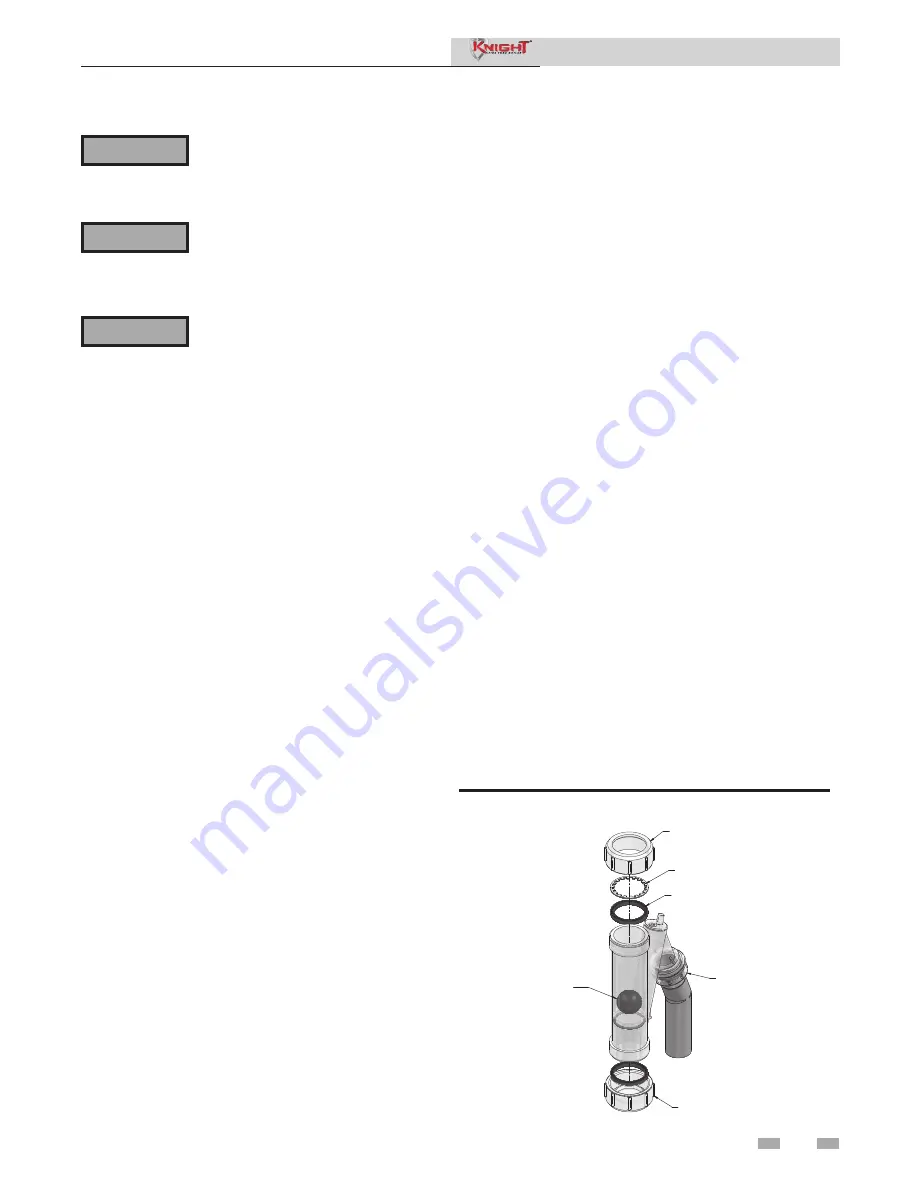
2
Maintenance
(continued)
33
Follow the Service and maintenance procedures given throughout this manual and in component literature
shipped with the boiler. Failure to perform the service and maintenance could result in damage to the boiler
or system. Failure to follow the directions in this manual and component literature could result in severe
personal injury, death, or substantial property damage.
The boiler should be inspected annually only by a qualified service technician. In addition, the maintenance
and care of the boiler designated in Table 2-1 and explained on the following pages must be performed
to assure maximum boiler efficiency and reliability. Failure to service and maintain the boiler and system
could result in equipment failure.
Electrical shock hazard – Turn off power to the boiler before any service operation on the boiler except
as noted otherwise in this instruction manual. Failure to turn off electrical power could result in electrical
shock, causing severe personal injury or death.
Address reported problems
1. Inspect any problems reported by the owner and
correct before proceeding.
Inspect boiler area
1. Verify that boiler area is free of any combustible
materials, gasoline and other flammable vapors and
liquids.
2. Verify that air intake area is free of any of the
contaminants listed in Section 1 of the Knight Fire
Tube Boiler Installation and Operation Manual. If any
of these are present in the boiler intake air vicinity, they
must be removed. If they cannot be removed, reinstall
the air and vent lines per this manual and the Knight
Fire Tube Boiler Installation and Operation Manual.
Inspect boiler interior
1. Remove the front access cover and inspect the interior
of the boiler.
2. Vacuum any sediment from inside the boiler and
components. Remove any obstructions.
Service Manual
Inspect condensate trap
1. Inspect the condensate trap and drain line monthly
to ensure it is properly installed and there are no
obstructions in the drain line.
2. Inspect the neutralizing kit (if installed) monthly to
ensure the condensate is draining properly and there is
an adequate amount of neutralizing agent available.
Annual cleaning
1. The condensate trap should be cleaned at least once
annually, or at the end of each heating season. Remove
the clean out cap on the bottom of the trap (FIG. 2-1).
Let the condensate and any debris drain out and clean
out any sediment that exists. Ensure the gasket is
seated in the cap before reinstalling.
Figure 2-1
Condensate Trap
2. To remove the condensate trap from the unit, loosen the
compression fitting located on top of the condensate (FIG.
2-1). Condensate fluid may run out of the heat exchanger.
3. The provided condensate trap is equipped with a ball
that acts as a seal against harmful flue gases escaping in
case there is no condensate in the trap. If this ball is not
present, flue gases may be able to pass through the trap
when there is no condensate present, resulting in an unsafe
environment. It is important to check and make sure the
ball is located in the trap, acting as a seal against flue gases.
4. Fill condensate trap with enough water to make the ball
float (FIG. 2-1).
5. Reinstall the condensate trap onto the condensate drain.
The stainless steel retaining ring, which allows the trap to
be pushed on, but not pulled off, must be installed between
the rubber sealing gasket and the compression fitting. The
compression fitting must be tightened.
6. Ensure condensate tubing slopes down and away from
the boiler into a drain or condensate neutralizing filter (if
installed).
CONDENSATE
DRAIN
REMOVABLE CAP TO
CLEAN OUT TRAP
COMPRESSION
FITTING
FLOAT BALL
IMG00209
GASKET
RETAINING
RING
⚠
WARNING
⚠
WARNING
⚠
WARNING
Содержание 100 Series
Страница 51: ...51 Service Manual Notes ...