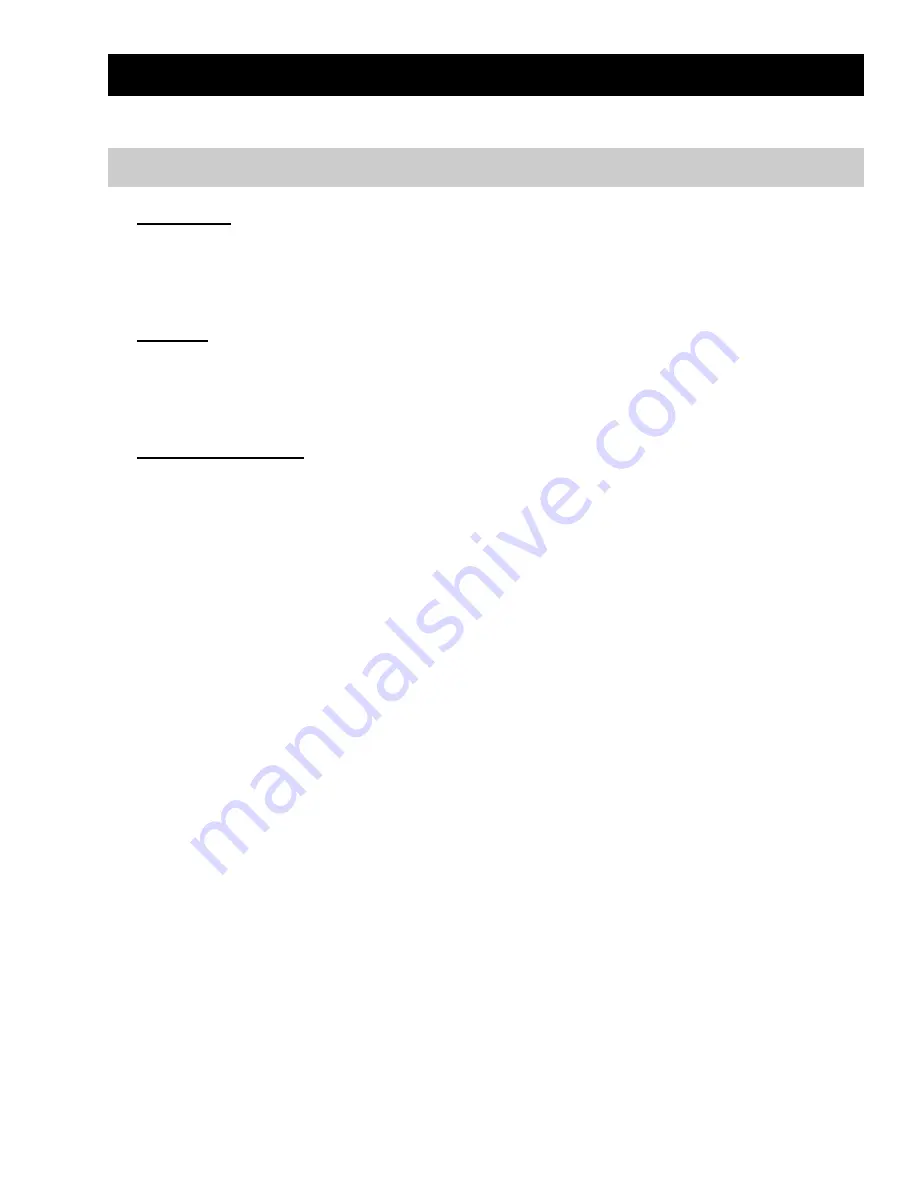
1
6700 SERIES RIP STRIP OWNERS MANUAL
Table of Contents:
FORWARD
Introduction ···························································································· 3
To the Purchaser ······················································································ 3
Models Covered in This Owner’s Manual ······················································· 4-5
Pre-Operational Check List ········································································ 6
SAFETY
Symbol Information ·················································································· 7
Safety Decals ··························································································· 8
Retail Customers Responsibility under the KMC Warranty ································ 9
Safety Procedures ····················································································· 9-10
ASSEMBLY SET-UP
General: ································································································ 11-12
Bolt Torque Chart ··········································································· 13
Overhead Layouts:
Rigid Machines:
4 Row ··················································································· 14-16
6 Row ··················································································· 17-20
8 Row ··················································································· 21
Stackfold Machines:
8 Row ··················································································· 22-24
12 Row ·················································································· 25-28
16 Row ·················································································· 29
Layouts for Standard Tillage Set-up:····························································· 30-33
Rear Distances for Standard Tillage Configurations: ········································ 34
Rip Strip Stackfold Transport Distances: ······················································· 35
Residue Cutting Options:
Front Swivel Coulter············································································· 36
Cover Crop Roller ················································································ 36
Row Cleaner Option: ················································································· 37
Ripper Tool Options:
Reset on the Go Shank ·········································································· 38
Toggle Shank ······················································································ 38
Toolbar Gauge Wheel: ··············································································· 39
Tillage Linkage Arms: ··············································································· 40