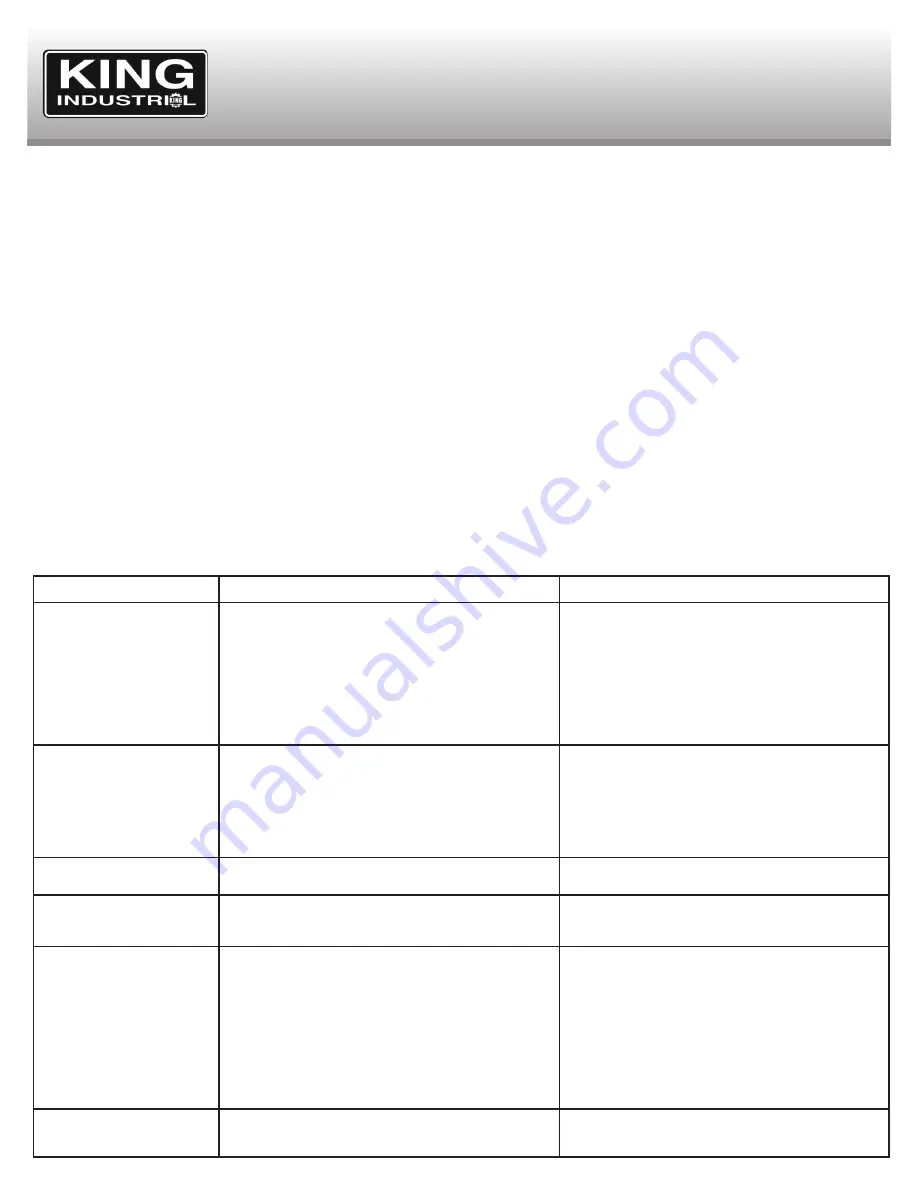
SERVICE & TROUBLESHOOTING
Chip Brush and Chip Scraper Replacement
The purpose of the chip brush and chip scraper is to remove chips from the saw teeth, the saw blade and the lower blade wheel so an
excessive amount of chips do not get into the wheel guard section of the saw. With extended use, this brush and/or scraper will become worn
and will require replacement.
Warning! Disconnect the bandsaw from its power source.
1. Remove the two pan head screws and washers holding the brush (diagram# 83) or scraper (diagram# 98) on.
2. Remove the worn brush or scraper.
3. Install the replacement brush or scraper.
4. Install the two screws and washers.
5. Adjust the brackets, if necessary, so that the brush makes slight contact with the lower blade wheel and the scraper is as close as possible to
the saw blade without touching it.
Adjusting or Replacing the Counterweight
The counterweight (diagram# 191) is located on the base of the saw. It is used to adjust the amount of force the saw puts on the work piece
when the hydraulic control cylinder is open.
Warning! Disconnect the bandsaw from its power source.
1. Move the bandsaw frame in the rearmost position by pushing down on the saw frame release lever (H-Fig.6) and lock it by turning the
hydraulic
feed stop dial
(E-Fig.6) clockwise.
2. Turn the lock knob on the counterweight counterclockwise to loosen it.
3. Slide the counterweight along the bar to the proper location.
4. Turn the lock knob on the counterweight clockwise to tighten it.
Problem
Excessive Blade Breakage
Premature Blade Dulling
Blade is Twisting
Unusual Wear on Side/Back of Blade
Bad Cuts (Crooked)
Bad Cuts (Rough)
Probable Cause
1. Material is loose in the vise.
2. Incorrect speed or feed.
3. Blade pitch is too coarse for the material.
4. Incorrect blade tension.
5. Saw blade is in contact with the workpiece before saw is started.
6. Blade rubs on the wheel flange.
7. Misaligned blade guides.
8. Cracking at the weld.
1. Blade pitch is too coarse.
2. Blade speed is too high.
3. Inadequate feed pressure.
4. Hard spots in the workpiece.
5. Scale on/in the workpiece.
6. Work hardening of material (especially stainless steel).
7. Insufficient blade tension.
8. Operating the saw without pressure on the workpiece.
1. Blade is binding in the cut.
2. Blade tension is too high.
1. Blade guides are worn.
2. Blade guide bearings are not adjusted.
3. Blade guide bearing bracket is loose.
1. Work piece is not square with the blade.
2. Feed pressure is too high.
3. Guide bearings are not adjusted properly.
4. Inadequate blade tension.
5. Span between the two blade guides is too wide.
6. Dull blade.
7. Incorrect blade speed.
8. Blade guide assembly is loose.
9. Blade guide bearing assembly is loose.
10. Blade track is too far away from the wheel flanges.
11. Guide bearing is worn.
1. Blade speed is too high for the feed pressure.
2. Blade teeth are too coarse.
Suggested Remedy
1. Clamp work securely.
2. Check the speed/feed appropriate for the material being cut.
3. Check for the recommended blade type.
4. Adjust the blade tension just to the point where the blade does
not slip of the wheel.
5. Start the motor before placing the saw blade against the work
piece.
6. Adjust the blade tracking.
7. Adjust the blade guides.
8. Use a longer annealing cycle.
1. Use a finer tooth blade.
2. Use a lower blade speed.
3. Decrease the feed speed pressure.
4. Increase the feed pressure.
5. Reduce the blade speed and increase the feed pressure.
6. Increase the feed pressure.
7. Increase the tension to the proper level.
8. Do not run the blade in/on the material at idle.
1. Decrease the feed pressure.
2. Decrease the tension on the blade.
1. Replace the blade guides.
2. Adjust the blade guide bearings.
3. Tighten the blade guide bearing bracket.
1. Adjust the vise so that it is square with the blade (Always clamp
the work piece tightly in the vise).
2. Lower the feed pressure.
3. Adjust the guide bearing clearance to 0.001” (0.002” max.).
4. Gradually increase the blade tension.
5. Move the blade guide bracket closer to the work piece.
6. Replace the blade.
7. Check the blade speed.
8. Tighten the blade guide assembly.
9. Tighten the blade guide bearing assembly.
10. Adjust the blade tracking.
11. Replace the worn bearing.
1. Reduce the blade speed.
2. Replace the blade with a finer tooth blade.