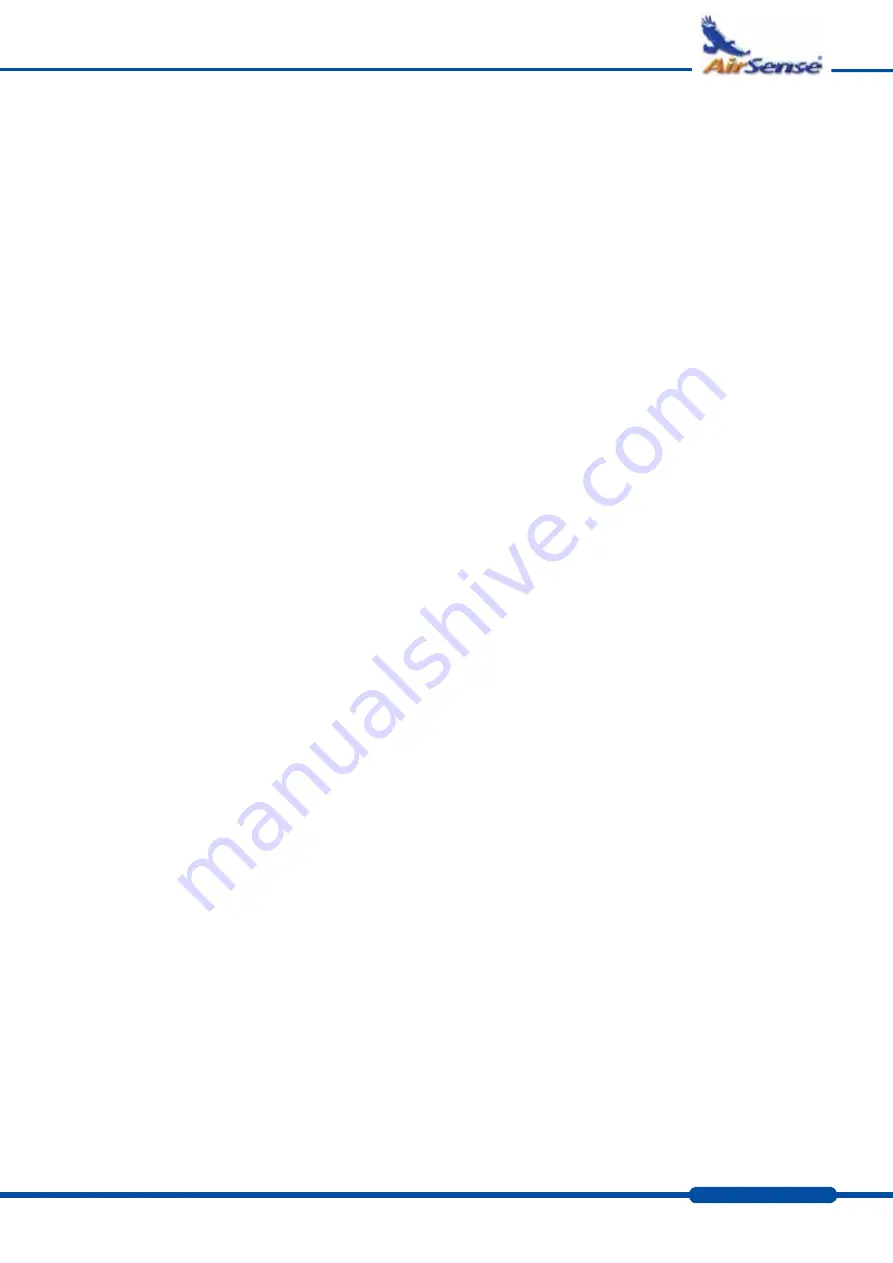
Page 23
Stratos-Micra • INSTALLER’S HANDBOOK • Iss. 1
5.2
EN54-20 and
UL compliance
5.2.1 EN54-20
5.2.2 UL
The installation must be designed using PipeCAD software, which is provided free
on the CD shipped with each detector. After designing the installation including
pipes, endcaps and sampling holes, enter the detector type. To select the detector
type, select Options, select Calculation options, and then select the detector from
he Type drop-down list.
t
Select “Options” “Calculate” or click on the calculator icon. The software will prompt
you to choose from “Use set hole sizes” “Best flow balance” and “Max. permissible
transit time”. Select the appropriate option and click “OK”. The results for each pipe
(“View” “Results”) show calculations for each sampling hole on the pipe with the
earest to the detector at the top of the screen, and the endcap hole at the bottom.
n
For EN54-20 compliance the transport time of the last sampling hole shall be
checked following all installation and proven to be less than or equal to that
etermined by PipeCAD.
d
The classification of each sampling device configuration and associated sensitivity
settings are determined ” by the column headed “Hole sensitivity % obs/m which
shows the predicted sensitivity for each hole. For the installation to comply with
EN54-20 depending on the class of installation, each sampling hole must be no
ess sensitive than the following:
l
Class A: 0.31% obs/m
Class B: 0.31% obs/m
lass C: 0.31% obs/m
C
The calculation can be further refined by leaving a working detector in the
protected area for at least 24hrs at the intended alarm factor for the installation
(this could be done before or after installation). The detector sensitivity can be read
from the “Sensitivity” figure on the histogram screen of the Remote software
supplied with each detector. Click "Options" and then click "Calculation options" to
open the "Hole calculation options" dialog box. Enter the sensitivity value obtained
from the practical test, and then click OK. The new calculated value will use the the
eal sensitivity from the practical test.
r
The PipeCAD software will determine the classification of any used configuration.
Commissioning and periodic system tests must involve smoke tests to verify that
the system performs as expected and enters Fire 1 alarm within the time
determined by PipeCAD from the farthest hole. The detector sensitivity must also
be inspected to ensure it has not radically fallen from the installed figure. If it has
changed for any reason, the new figure must be re-entered into PipeCAD and the
recalculated hole sensitivities must be confirmed to be within the class limits
shown above. The settings of a compliant system should be recorded, as it is
possible by changing certain programmable functions to make the system non-
compliant. If functions are changed, it is recommended that the system is retested
if continuing compliance is in any doubt.
UL268 fire tests were passed with an installation as follows:
- Total sampling pipe length: 160 ft (single pipe)
- Number of sampling holes: 10
- Worst-case sampling hole sensitivity as indicated by PipeCAD: 1.28% obs/ft*
- Alarm factor: 1
- Fire 1 alarm delay: 0 seconds
These settings gave satisfactory responses to the test fires in 120 seconds or
better. For the purposes of UL268 compliance, these should be regarded as worst
case values. Layouts should be planned in PipeCAD and the indicated worst-case
hole sensitivity should be better than 1.28% obs/ft*. Commissioning smoke tests
should be performed to ensure that the farthest sampling hole from the detector is
capable of generating a fire alarm within 120s of receiving smoke
.
*The results should be verified at installation by entering the installed detector's Fire 1
sensitivity (as indicated in the remote software histogram screen) into the PipeCAD
“Options/Calculation options/Detector sensitivity” field and recalculating the layout results.