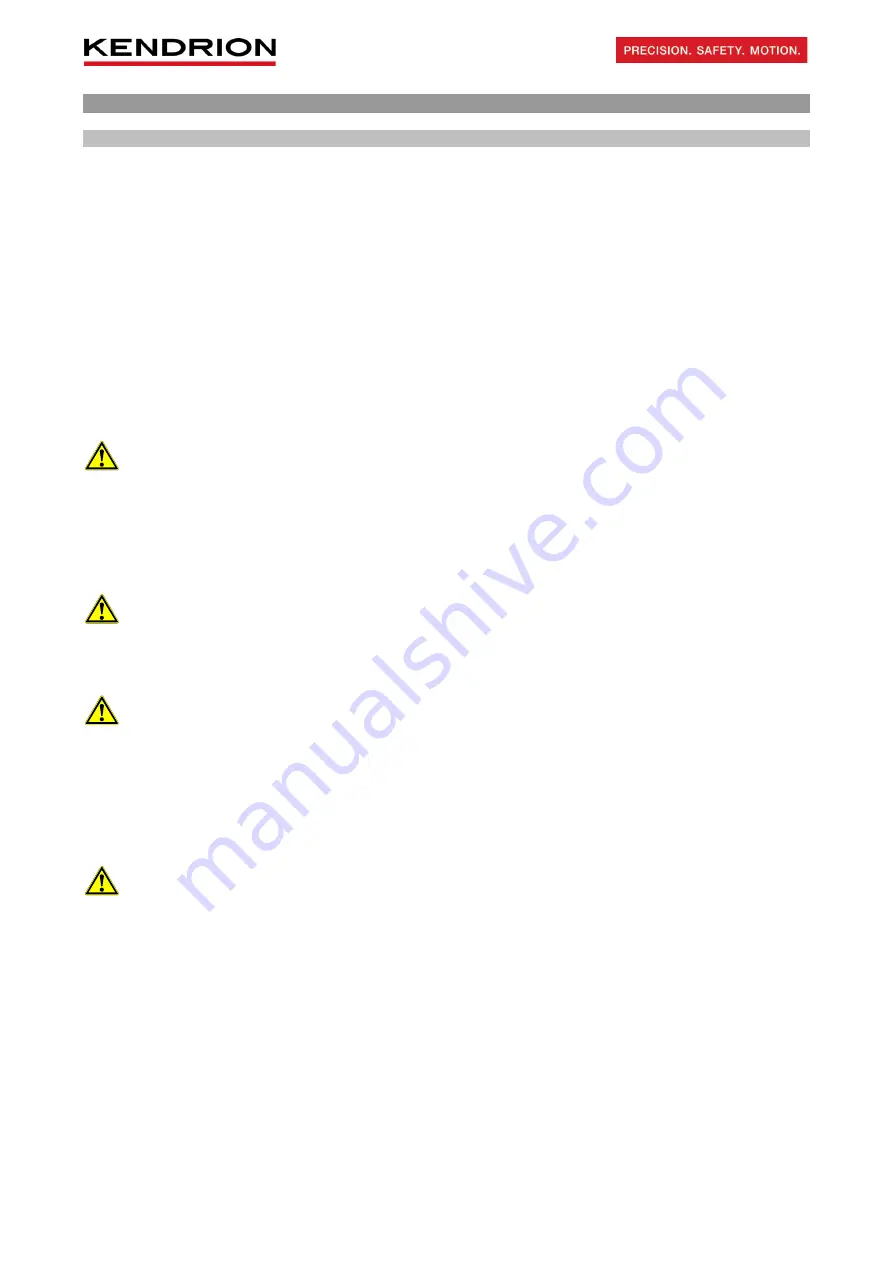
Operating Instructions BA 77 600..A00 // Last updated: 13/03/2020 // Page 20 of 33
4. Maintenance
4.1 Checks and service
The spring-applied single-disc brake does not require any particular maintenance except that the air gap 's'
must be measured at regular intervals. After the screw plugs (23) have been removed from the intermediate
ring (6), the air gap 's' (see Table 29/1 for rated air gap specification) between the armature (2) and the friction
disc (5) can be checked by means of a feeler gauge while the brake is energised. When the maximum air gap
s
max
has been reached (see Table 29/1), the friction disc (5) must be replaced as follows: Loosen the fixing
screws (22) and remove the brake from the hub (17). Remove the cover hood (9) and screw out the adjusting
ring (7) after having loosened the set screw (8). Loosen the machine screws (13) and sealing rings (12), and
remove the flange (11) and friction plate
3)
(10) from the intermediate ring (6). Remove the worn friction disc
(5) and replace it by a new one. Before reassembling the brake components, clean all parts (flange (11), friction
plate
3)
(10), armature (2) and intermediate ring (6)) with grease-free cleaners. Install the friction plate
3)
(10)
in such a way that the convex surface is in contact with the flange (11). Screw the flange (11) with the
intermediate ring (6) to the core element of the spring-applied single-disc brake by means of the machine
screws (13) and sealing rings (12). Screw in the adjusting ring (7) until the b
3
clearance (marked on the collar
of the brake back) has been reached and secure it with the set screw (8). Install the cover hood (9) as shown
in Fig. 6/1. Install and connect the spring-applied single-disc brake as described in Sections 3.2 and 3.3.
Attention!
When installing the spring-applied single-disc brake, it is crucial that the fixing screws (22) be tightened
applying the M
A
tightening torque specified in Table 8/1. The machine screws (13) must be tightened to the
M
AZ
torque specified in Table 8/1. The set screw (8) of the adjusting ring (7) must be tightened to M
A
= 3Nm.
After the friction disc (5) has been replaced, the air gap 's' must be checked (see Table 29/1 for information on
the rated air gap).
Attention!
After the adjusting ring (7) has been screwed in, the set screw (8) must be located directly beside the marking
of the adjusting ring clearance b
3
. Check that the set screw is not positioned on a stud (4).
Attention!
Depending on its operating condition, it may no longer be possible to release the spring-applied single-disc
brake when the maximum air gap s
max
(see "Technical specifications" in Table 29/1) has been exceeded. In
this case, the braking effect cannot be neutralised. This may cause thermal overloading of and irreversible
damage to the brake if the machine (e.g. motor) is started before the brake has been released. Thermal
overloading of the machine (e.g. motor) may occur if the machine (e.g. motor) is not started while the brake is
still engaged.
Caution!
If a hand release lever (21) is fitted to the brake and the maximum air gap s
max
(see "Technical specifications"
in Table 29/1) has been exceeded, the hand release lever (21) will limit the axial movement of the armature
(2). This will cause the torque to be reduced down to zero. Whenever carrying out maintenance work, check
the degree of wear of the friction disc (5) and the air gap 's' and replace the friction disc (5) well before the
maximum air gap s
max
(see "Technical specifications" in Table 29/1) is reached.
3)
Size 10 to 16 brakes.
Содержание 7760016A00-0004
Страница 33: ......