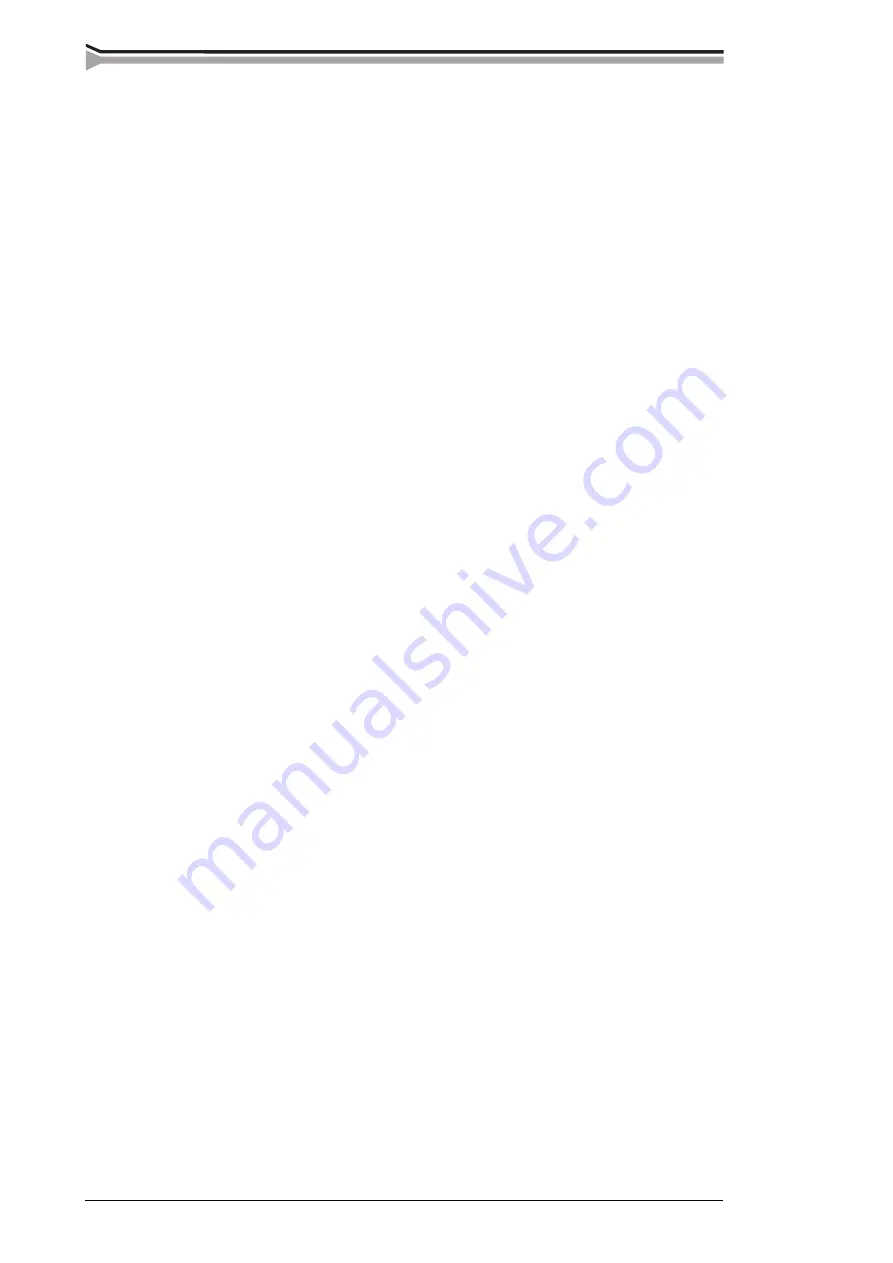
PROMIG 200ML/0509 – 16
© KEMPPI OY
Err 5: PROCOOL cooling unit has stopped welding. Reason can be break of supply
voltage from PROCOOL, pressure of liquid circulation doesn´t arise or tempe-
rature of cooling liquid has arisen too high.
Err 6: Wire feed unit has stopped welding in liquid position of selecting switch S12
of air/liquid-cooled gun for PROMIG, because data communication to cooling
unit is broken (defect in intermediate cable or in connection).
Err 7: Selecting switch S12 of air/liquid-cooled gun for PROMIG is in air position,
PROCOOL is switched-on and start switch is pressed down. Purpose of opera-
tion is to prevent the liquid-cooled gun from being destroyed, if the selecting
switch S12 for air/liquid-cooling is in wrong position.
Err 8: Liquid-cooled PMT gun is overheated.
Err 9: Overload of wire feed motor, which can be caused e.g. by blocked wire guide
of gun or by gun cable, which is too much curved.
Err 10: Operation of thermal release of PRO power source has stopped welding.
Err 11: You try to use the PMT gun, when their use is prevented with the 5. jumper
operation.
Err 12: Welding has been stopped, because so called door switch or gas guard has ope-
rated (operations need extra mountings to standard unit).
Eliminate the error codes as follows:
Error code Err 1 is eliminated when PROMIG wire feed system is set into MIG state.
Blinking of error codes Err 2-4 ends automatically within 5 s, if the trigger is not
pressed down.
Eliminate the reason of error before next start.
Blinking of error codes Err 5-12 ends by next start, if the reason of error code has been
eliminated.