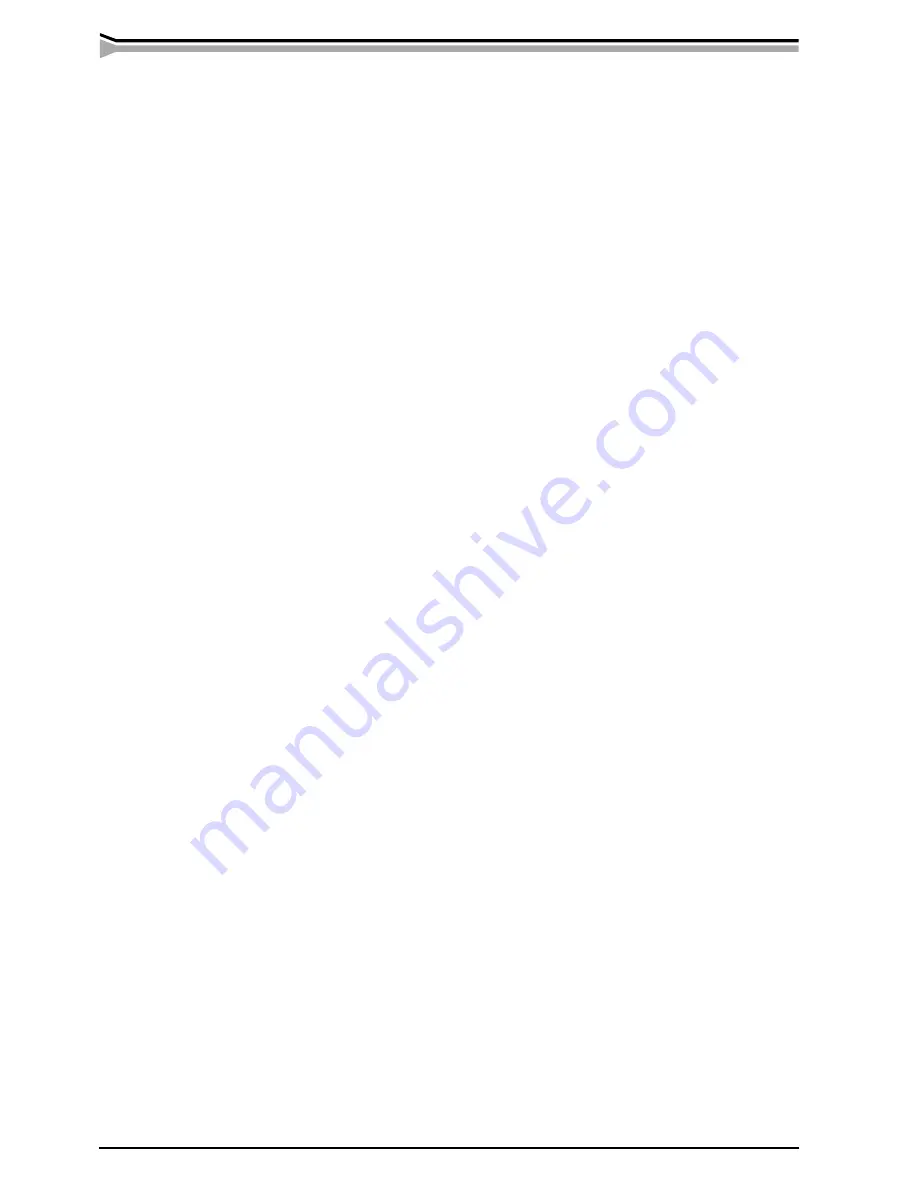
12 – KEMPOWELD 4200, 4200W, 5500W / 0531
© KEMPPI OY
A good tip: Blow compressed air into the tank; closing the filling opening by hand is enough.
The water is pumping, but does not return back to the tank or the return flow is weak:
– filling of interconnection cable can take several minutes
– if you have lifted the gun or interconnection cable for the filling time many meters higher than the power
source, the filling will happen considerably slower. Fill the hoses on the floor position.
– check the whole flowing line connector by connector
The water is pumping, but during welding the red pilot lamp for the water pressure is
illuminated and the equipment is stopped:
– check the cooling water volume and return flow to the tank
– in the system are air bubbles or leakages, especially check the connections of the cooling unit.
– the pressure switch set value (ca. 1 bar) is unsuitable for the gun you are using:
1. Open the side plate. In the middle at the upper end of the pressure guard connected to the pump is the
adjusting screw for limit value.
2. Use the pump during the adjustment by the test switch.
3. After ca. 5 s use twist the screw carefully until the pilot lamp is switched off.
4. Check the result by welding.
5. If the adjustment and checkings do not eliminate the disturbance, take contact with the Authorized
Kemppi repair shop.
During welding the yellow pilot lamp for overheating is lit and the equipment is stopped:
– release the trigger. When the lamp is switched off, the operation has been reset automatically
– check if the gun is suitable for power you are using
– check condition of connectors and connections in the welding current circuit
4. MAINTENANCE
The amount of use and the working environment should be taken into consideration when planning the frequency of
maintenance of the machine. Careful use and preventive maintenance will help to ensure trouble-free operation.
Cables
Check the condition of welding and connection cables daily. Do not use faulty cables! Make sure that the mains
connection cables in use are safe and according to regulations! The repair and mounting of mains connection cables
should be carried out only by an authorized electrician.
Power source
NOTE!
Disconnect the plug of the power source from the mains socket before removing the cover plate.
Check at least every 6 months (twice a year):
– Electric connections of the unit - clean the oxidized parts and tighten the loosened ones. NOTE! You must
know correct tension torques before starting the repair of the joints.
– Clean the inner parts of the machine from dust and dirt e.g. with soft brush and vacuum cleaner.
Do not use compressed air, there is a risk that dirt is packed even more tightly into gaps of components!
Do not use pressure washing device!
Only authorized electrician shall carry out repairs to the machines.
Regular maintenance
Kemppi service repair shops make regular maintenance according to agreement.
The major points in the maintenance procedure are listed as follows:
– Cleaning of the machine
– Checking and maintenance of the welding tools
– Checking of connectors, switches and potentiometers
– Checking of electric connections
– Metering units checking
– Checking of mains cable and plug
– Damaged parts or parts in bad connection are replaced by new ones
– Maintenance testing. Operation and performance values of the equipment are checked, and adjusted when
necessary by means of test equipment.