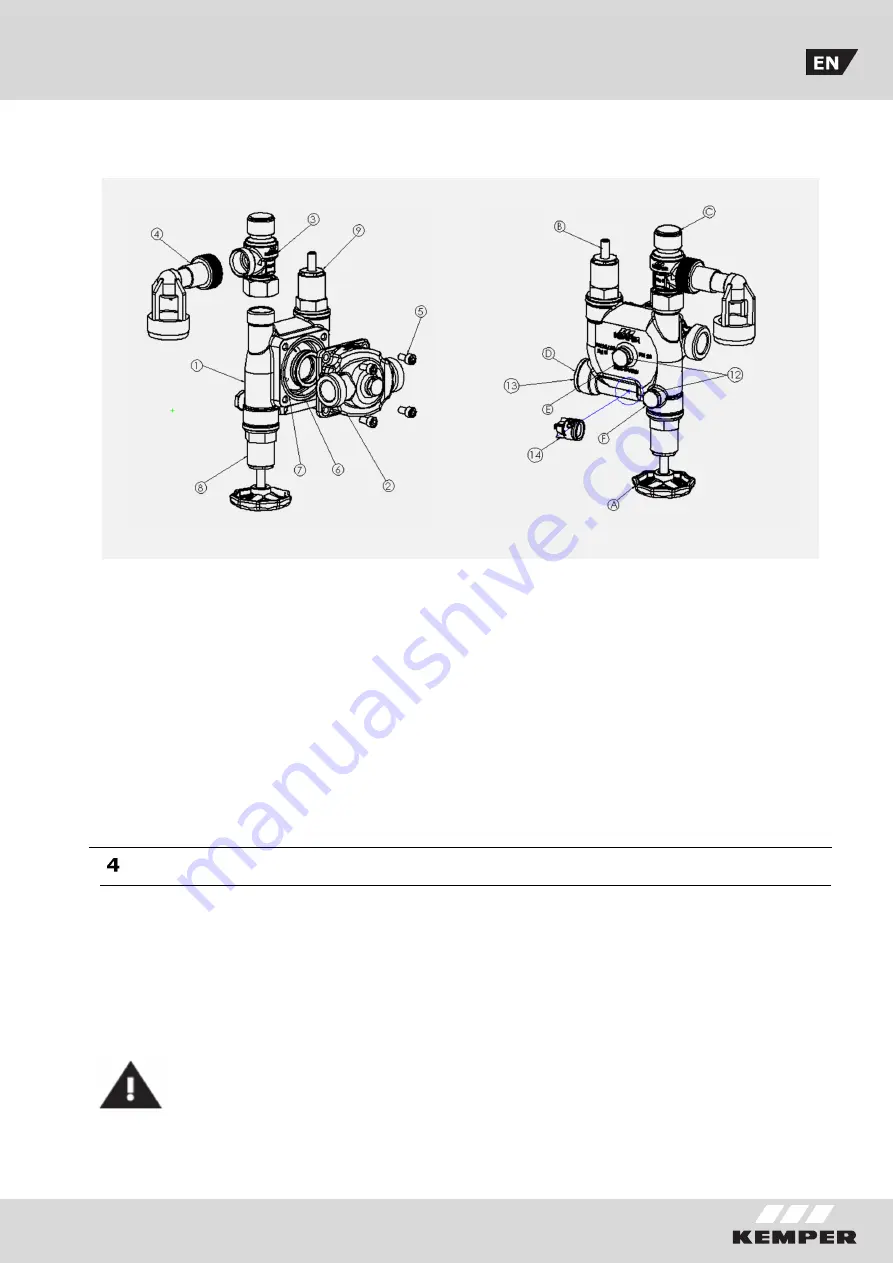
K4100714000001-00 / 05.2017
7
Assembly
see Scope of delivery pages 2/3 Accessories | Spare parts list
Mount basic module (2) in place by means
of hexagon socket head cap screws M 6 x
12 (5). After pressure testing (see 5. Initial
system checkout), screw the diaphram-
type safety valve (3) onto the safety group
housing and tighten firmly. For pressure
testing purposes, the connection for the
diaphragm-type safety valve can be closed
off with a cap with an R ¾“ female thread).
The telescopic drainage funnel (4) is
attached to the safety valve and aligned
vertically downward. The drainage funnel
must be rigidly connected to the blow-down
piping. According to DIN 4753 Part 1, the
blow-down piping may have a maximum of
2 bends and be a maximum of 2 m in
length. If reasons dictate the use of more
bends or a greater length, then the entire
blow-down piping must be dimensioned to
have the next higher nominal size. More
than 3 bends and a length of over 4 m are
not permissible. The blow-down piping
must normally be installed in slanting
position.
Initial system checkout
In the as-delivered condition the main
isolating valve (A) and the maintenance
valve (B) are fully opened. It must first of
all be ensured that the upstream piping has
been adequately flushed through. The main
isolating valve and the maintenance valve
must then be opened successively. Once
the pressure in the system has stabilized,
the seal cap of the safety valve (C), the
backflow preventer test connection (F) and
the pressure gauge connection (E) must be
opened for a short time in order to
eliminate any air pockets.
The safety valve outlet must not be
closed off. In order to subject the
safety group to pressure testing,
the safety valve must be removed
from the safety group and plugs
used to seal off the safety group. The
pressure testing is performed at 1.5 times
the working pressure to DIN 1988-2