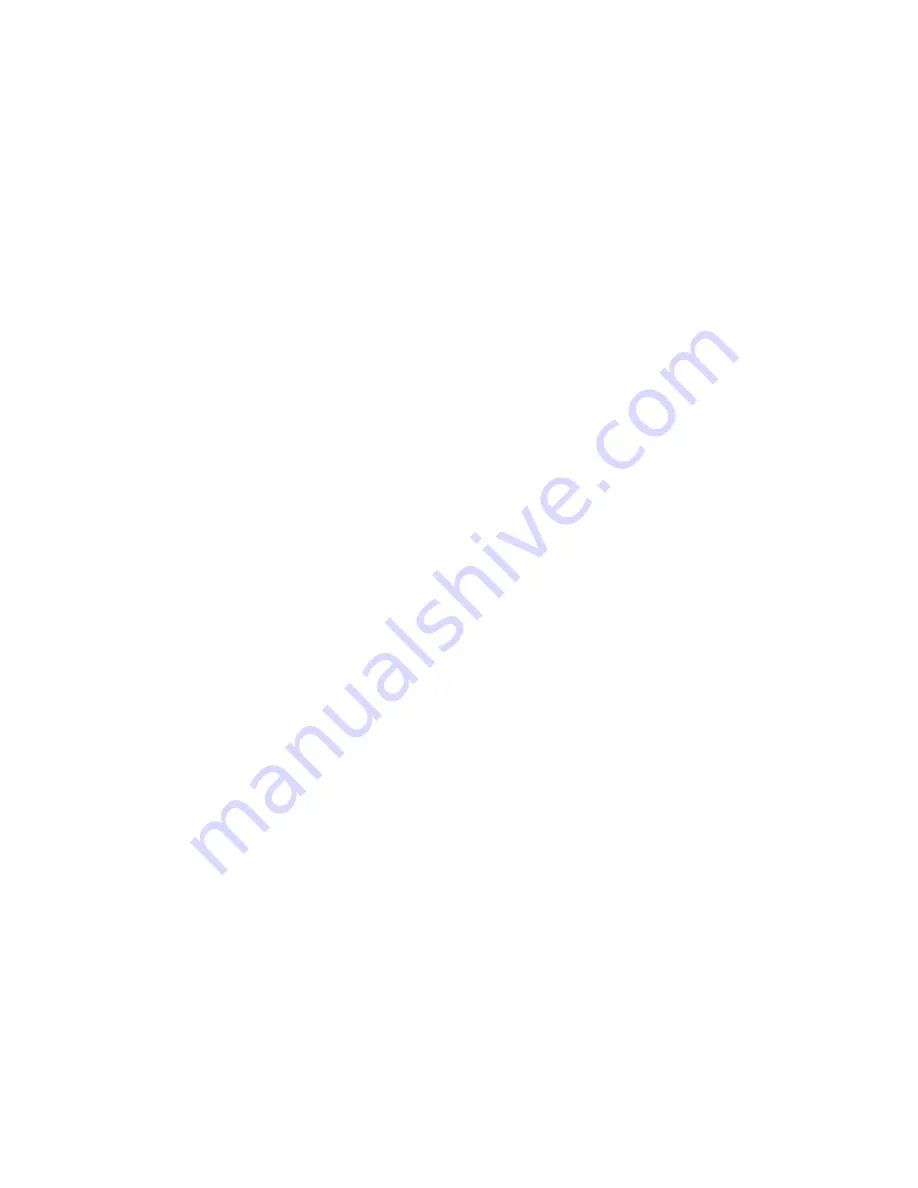
30
PFP7/REV C/01-08
8.3
Optical system description
Light is emitted from the flame and collected by a plano-convex lens mounted on the inner
chimney. The wavelength of light reaching the photo-detector is determined by up to 5 different
interference filters mounted in a wheel. The filter in the light path is selected by the front panel
control and is indicated by this control. Na (589nm) and K (766nm) filters are fitted as standard
and positions 1, 2 and 3 can be fitted with Ca (620nm), Ba (520nm) and Li (670nm) filters to
order.
The filters are held in the wheel by circlips. Should replacements or alternatives need to be
fitted, care must be taken to prevent fingerprints getting onto the optical surfaces. If this does
happen a small amount of ethanol on a very soft, lint-free cloth may be used to gently wipe
away deposits.
Filtered light from the flame falls on the PIN diode mounted on a small PCB on fixing brackets
that allow critical adjustment so that the lens on the diode can be set to an optimum position in
the light path. The electrical signal from the diode is taken via a 3-pin connector and a screened
cable to the main PCB.
8.4
Power supply description
Refer to
Figures 8.4.1
and
8.4.2
.
The mains AC supply is fed in via the rear panel socket/filter unit to a 3A anti-surge fuse (6A
anti-surge fuse when operating on 115V). This fuse protects any equipment such as a recorder
or compressor plugged into the
POWER OUT
socket on the rear panel.
The AC line is taken via a 250mA fuse, for protecting the internal circuitry, to the
power
switch
on the front panel. The AC neutral is taken to the other pole of the
power
switch. The earth from
the mains supply is taken directly to the chassis.
From the
power
switch the AC line is taken to a two-position
VOLTAGE SELECTOR
switch
mounted on the rear panel and then onto the transformer primary winding; the other side of
which is connected to the neutral from the
power
switch. The transformer primary is auto wound
to provide a step up function to supply 240V for the igniter unit when a 115V supply is
connected.
The two 12V secondary windings are joined with a centre tap which forms the 0V rail; they are
full wave rectified to give a +12V and -12V supply with respect to the centre tap. The
unreg12V is fed to the 7805 1 amp regulator to give the +5V rail. The unregulated -12V
is fed to the 79L05 100mA regulator to give the -5V rail.
The unreg12V is used to automatically operate the fuel solenoid via the relay, but it is
also fed to one pole of the ignition switch for manual operation. The other pole is fed with 240V
which is then switched to the ignition unit, such that when the ignition switch is depressed, the
fuel solenoid is opened and the ignition unit activated to generate a series of high voltage
pulses (approx. 2 per second) which are discharged in the form of a spark between the ignition
electrode and burner, which is at earth potential. Hence the fuel passing through the solenoid
into the mixing chamber and out through the burner will be ignited by the series of sparks, whilst
the solenoid is manually held open.
The thermo-electric potential developed by the thermocouple mounted on the top, back of the
chimney is fed into the inverting input of the 741 (IC1). When this level becomes greater (due to
flame temperature) than the level set by RV8 on the non-inverting input to the 741 (IC1) then the
output rapidly switches from +4.5V approx. to -3.0V approx. turning off transistor TR2 which, in
turn, switches transistor TR1 on, energising the relay coil. The normally open contacts close
holding the +12V supply on the solenoid. If the flame should be extinguished the thermocouple
cools down and the voltage on the inverting input IC1 decreases. When the level falls below that
set by RV8 on the non-inverting input to IC1 the output goes back to +4.5V approx., turning on