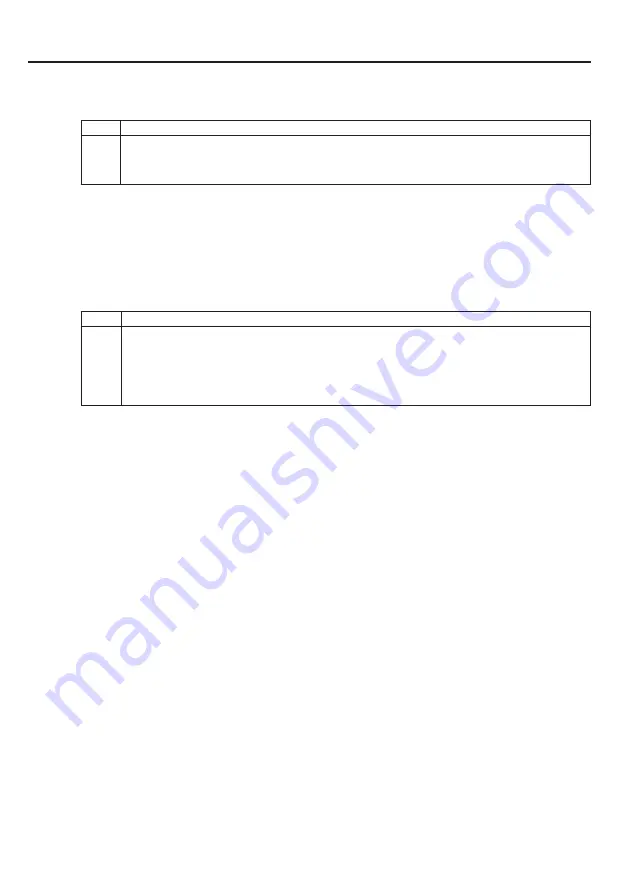
20
CP-Parameter
CP.10 Speed Control / Configuration
This parameter activates the speed or the torque control.
Value Description
4
Speed control
5
Torque control
6
Speed / torque control
CP.19 Motor adaption
The factory settings of the servo correspond to the size of the unit and the respective
motorIf the motor data in CP.11...18 are changed, then CP.19 must be activated once.
This re-adjusts the current controller, torque curve and torque limit. The torque limit is
set at the value, that is maximally possible in the basic speed range (depending on
inverter rated current). Rated motor torque x 3 at maximum.
CP.19 Pre-adjustment of the motor-dependent control-parameters.
1
The voltage class of the inverter is taken as input voltage.
2
The measured DC-link voltage / v2 measured at switch on is taken as input
voltage.Thus the frequency inverter can be adapted to the actually
available mains voltage (e.g. USA with 460 V).
When control release is active the adjustment was not completed. „nco“ appears in the
display!
CP.20 Absolute position (encoder 1)
The system position of the attached resolver system is adjusted at EC.07. With this
parameter it is possible to adjust the controller to a not aligned motor. If the ystem
position of the motor is unknown an automatic trimming can be done. Before starting
with the adjustment, the direction of rotation must be checked. The speed display at
CP.1 must be positive when the engine runs manual in clockwise direction. If that is not
the case, the direction of rotation can be exchanged as described with CP.21. If the
correct direction of rotation is displayed, it can be started with the adjustment.
• The connected motor must be able to rotate freely.
• Open control release (terminal X2A.16).
• Set CP.20 = 2206.
• Close control release (terminal X2A.16).
Now the motor is excited with its rated current and aligned to its zero position. The
adjustment is finished when the displayed system position at CP.20 does not change
for approx. 5 s. In this case open control release and switch off the unit.
If the error message E.EnC is displayed during trimming the direction of rotation must
be checked (CP.21). In this case the position trimming must be repeated.
In case that motors with aligned encoder system are used, the value which has been
established by the automatic trimming, can be entered under CP.20 as well. The
adjustment values of known motors of the KEB COMBIVERT S4 series must be
multiplied by the pole-pair number of the motor. The lower 16 bits of the result must be
entered in CP.20.
Содержание COMBIVERT F5 Servo
Страница 1: ...C O M B I V E R T 00 F5 SEM KA01 11 2004 Installation Guideline C GB A Housing...
Страница 25: ...25...
Страница 26: ...26...
Страница 27: ......