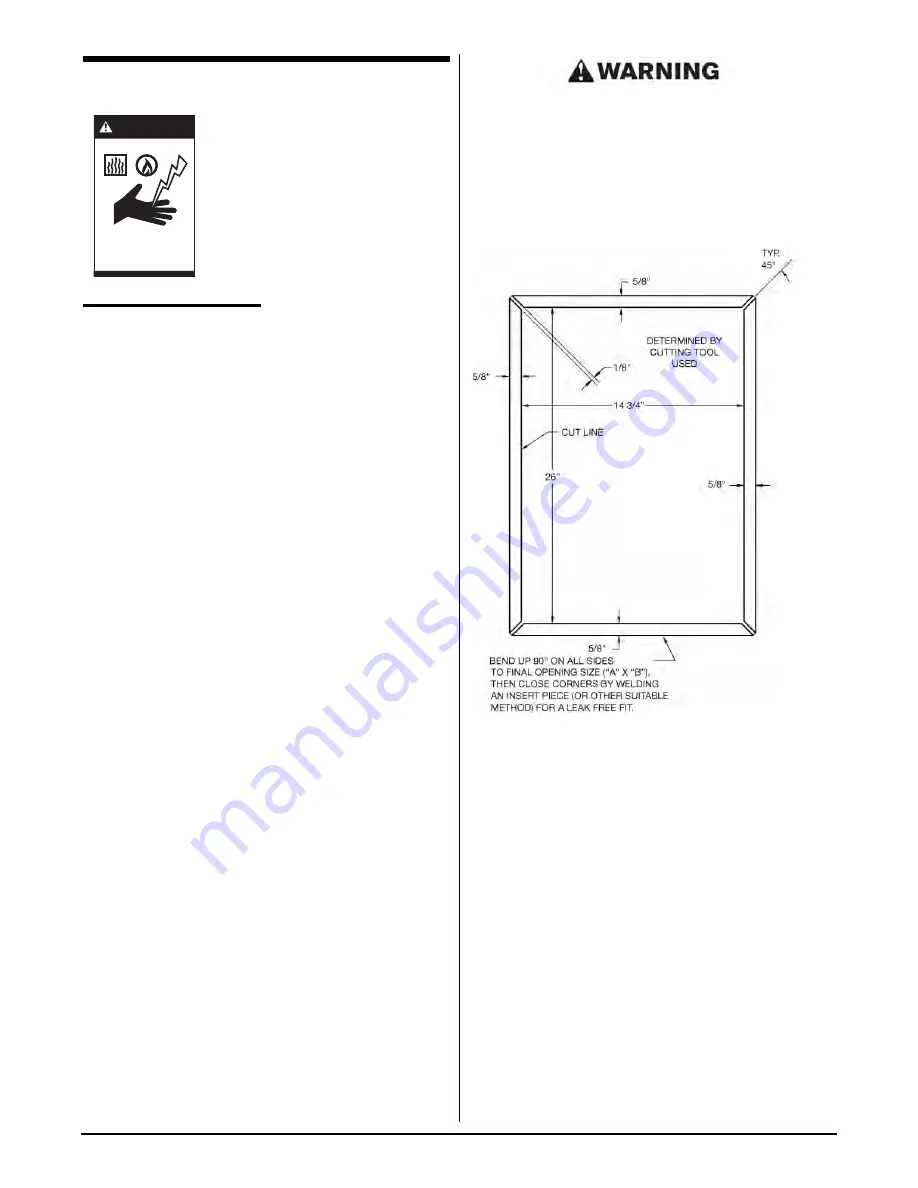
3
II INSTALLATION
This Custom Pasta
™
System MUST
be installed, inspected, calibrated
and serviced by qualified and/or
certified and/or licensed service
personnel – you may void your
Keating warranty if installation is not
completed per current local, national
and Keating specifications. Contact
your dealer for assistance.
DAMAGE DURING
SHIPMENT
The Custom Pasta
™
System has been assembled,
tested and inspected at the factory. Upon arrival, the
complete Pasta System should be checked for any
damage that may have occurred during shipment.
IF EQUIPMENT ARRIVES DAMAGED
Keating does not assume responsibility for loss or
damage incurred in transit.
IMPORTANT
This merchandise has been thoroughly inspected and
carefully packed before leaving our plant. Responsibility
for its safe delivery was assumed by the carrier at the
time of shipment. Claims for loss or damage to the
contents should, therefore, be made upon the carrier,
as follows:
CONCEALED LOSS OR DAMAGE
Concealed loss or damage means loss or damage
which does not become apparent until the merchandise
has been unpacked. The contents may be damaged in
transit due to rough handling even though the carton
may not show external damage. When the damage is
discovered upon unpacking, make a written request for
inspection by the carrier’s agent within fifteen days of
the delivery date. Then file a claim with the carrier since
such damage is the carrier’s responsibility. By following
these instructions carefully, we guarantee our full
support of your claims to protect you against loss from
concealed damage.
VISIBLE LOSS OR DAMAGE
Any external evidence of loss or damage must be noted
on the freight bill or express receipt, and signed by the
carrier’s agent. Failure to adequately describe such
external evidence of loss or damage may result in the
carrier refusing to honor a damage claim. The form
required to file such a claim will be supplied by the
carrier.
DO NOT RETURN DAMAGED MERCHANDISE TO
KEATING. FILE YOUR CLAIM AS ABOVE.
IT MAY BE NECESSARY TO INSTALL A BACK FLOW
OR CHECK VALVE ON THE WATER SUPPLY LINE
TO THE PASTA COOKER. CHECK WITH EITHER
YOUR LOCAL WATER OR HEALTH DEPARTMENT
TO DETERMINE IF THIS IS NECESSARY IN YOUR
SPECIFIC AREA.
DROP-IN PASTA COUNTER
CUTOUT/INSTALLATION
INSTALLATION NOTES
1. Minimum of 130 sq. in. unobstructed vent area near
pasta cooker required for combustion.
2. All Drop-In Pasta must be 16” from any open flame.
3. Pasta must be located no more than 5” from counter
top front.
4. Cabinet must be reinforced to support full weight of
past in use (pasta, water, food, etc.).
5. Pasta cooker must be properly ventilated and located
under an exhaust hood.
DROPPING THE PASTA COOKER INTO THE
It is only necessary to place the pasta cooker in such a
position that the front edge overlaps the front raised
edge of the opening.
COUNTER TOP
WARNIN
G
Improper installation
can cause damage,
injury or death.
Shock
Burns
Gas
Содержание INSTANT RECOVERY SERIES 2009
Страница 17: ...15 VII WIRING DIAGRAMS 14 ELECTRIC PASTA 2 THERMOSTAT WIRING DIAGRAM WITHOUT TIMERS 2...
Страница 18: ...14 ELECTRIC PASTA WITH DIGITAL TIMERS WIRING DIAGRAM 16...
Страница 19: ...17 14 ELECTRIC PASTA WITH 138 TIMERS WIRING DIAGRAM PRE 2000 SERIES BLACK DIAL TIMER NOT DIGITAL...
Страница 20: ...18 14 ELECTRIC PASTA WITH BASKET LIFT AND DIGITAL TIMERS WIRING DIAGRAM...
Страница 21: ...19 18 20 ELECTRIC PASTA WITH 138 TIMERS WIRING DIAGRAM PRE 2000 SERIES BLACK DIAL TIMER NOT DIGITAL...
Страница 22: ...20 18 ELECTRIC PASTA 2 THERMOSTAT WIRING DIAGRAM WITHOUT TIMERS...
Страница 23: ...21 24 ELECTRIC PASTA WITH DIGITAL TIMERS WIRING DIAGRAM...
Страница 24: ......