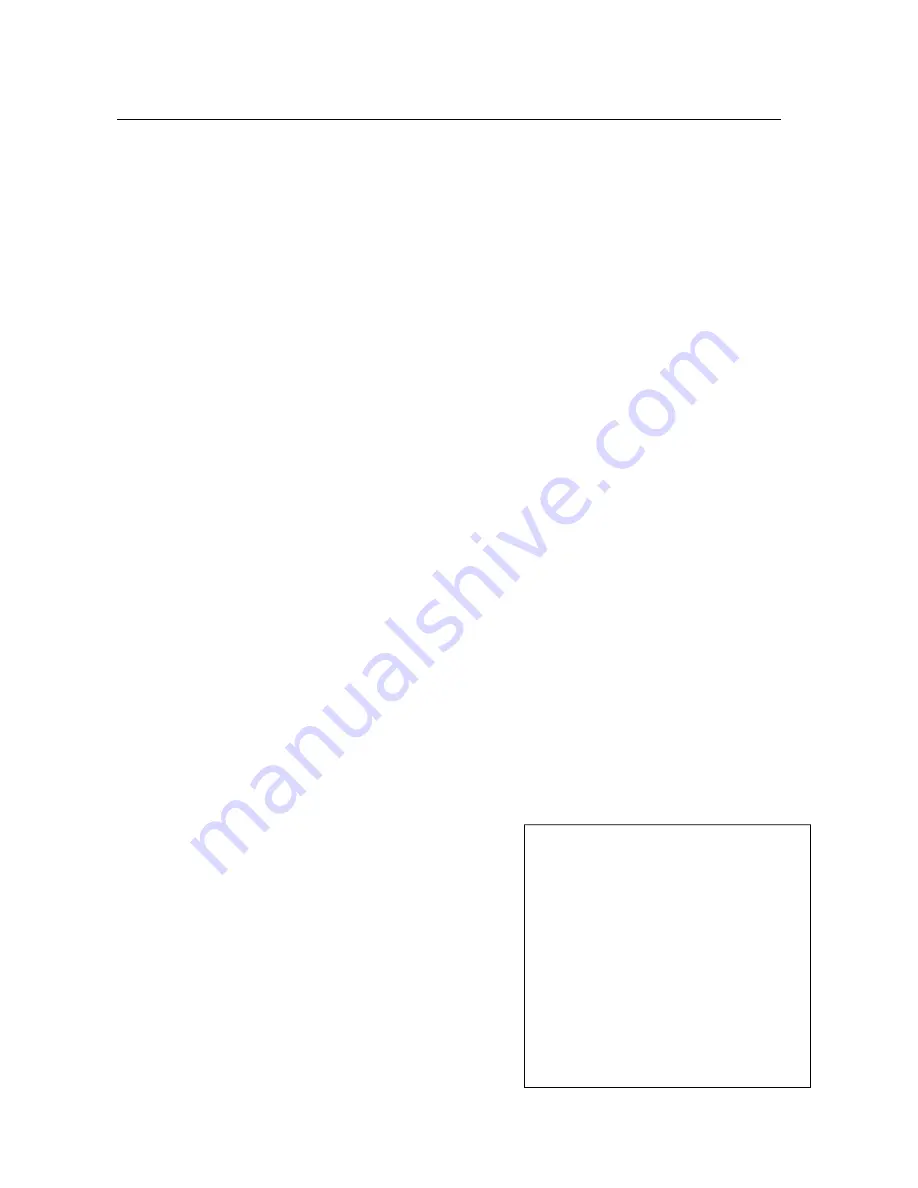
16
Prefilter Maintenance
Background:
Maintaining a healthy watermaker largely involves taking proper care of the
prefilter assembly and seawater intake plumbing. Failure to do so is the most common cause of the
two most frequent types of watermaker “failure” we hear about: (1) producing diminished or no
freshwater output, or (2) producing “bad-smelling” product freshwater. Here is what happens:
No Freshwater Output:
The most common cause of diminished or no product freshwater
output is air entering the seawater intake system at some point. The pump volume is small and the
pressure required to press water through the membrane is rather high (about 800 psi). Since air is
highly compressible, a very small amount of air can keep the pump from producing enough pressure
to produce product freshwater. Periodically inspect and test the entire seawater intake system to
assure that all joints and fittings are airtight, especially the connections at the prefilter assembly.
(
Note:
Be aware that a stable air gap at the top of the prefilter housing is not uncommon, and
doesn’t necessarily mean that air is getting to the pump itself.)
Bad-smelling Product Freshwater:
The purpose of the prefilter assembly is to trap any
particulates in the intake seawater that are larger than 30 microns. A coarse strainer (if installed)
performs the same chore for contaminants of larger size. In each case, trapped material remains in
the prefilter housing (or strainer bowl) until removed.
Much of the trapped material is organic: plankton, seaweeds and flotsam of all types. After a
watermaker has been turned off, this material soon begins to decompose. As it does, it breaks down
into a number of chemicals composed of smaller molecules. Some of these molecules are small
enough to pass through the watermaker membrane along with the product freshwater. Perhaps the
best-known example of such a chemical is hydrogen sulfide, a gas which (in small concentrations)
smells like “rotten eggs.”
Two main factors affect the speed with which these products of organic decomposition will
contaminate a watermaker system: (1) the ambient temperature and (2) the quantity of trapped
material. We realize that many users of our equipment run their watermakers in near-shore
situations while anchored. The amount of trapped material is usually high in such locations, and the
prefilter assembly will require more frequent attention. Moreover, the high ambient temperatures in
tropical locations greatly accelerate the rate of such decomposition. Users in temperate climate areas
or users processing open-ocean seawater during offshore passages are less likely to require the
same diligence.
Prefilter Maintenance:
At the
end
of each run of your watermaker, examine the prefilter
assembly (and the coarse strainer, if installed) for trapped
material. If anything is visible, perform the following
procedure:
1.
Unscrew the prefilter housing, remove the dirty
prefilter element, and discard the water in the bowl.
Do not lose the large o-ring at the top of the bowl.
2.
Clean the inside surface of the prefilter bowl. Inspect
and clean the o-ring at the top of the bowl. Lubricate
the o-ring and the threads of the prefilter housing
with a light coat of silicone grease.
3.
Install a clean filter element and screw the prefilter
bowl back on securely.
Warning:
If you purchase after-
market filter elements, be certain they
are made from
polyester
fibers. In
particular, be wary of elements made of
paper materials. They look very similar,
but are designed for use with other
types of water purification systems and
are harmful to the membranes and high
pressure pumps used in reverse osmosis
watermakers. Be certain you purchase
only polyester filters of 30-micron (or
finer) size.
Содержание PowerSurvivor 40E
Страница 1: ...PowerSurvivorTM 40E 12 Volt 24 Volt Watermakers OWNER S MANUAL ...
Страница 30: ...30 Diagrams ...
Страница 31: ...31 Kit Spool Valve 8018615 8016525 ...
Страница 32: ...32 ...
Страница 33: ...33 ...
Страница 35: ...35 Service Log Date Preserved Membrane Cleaned Membrane Other Service ...