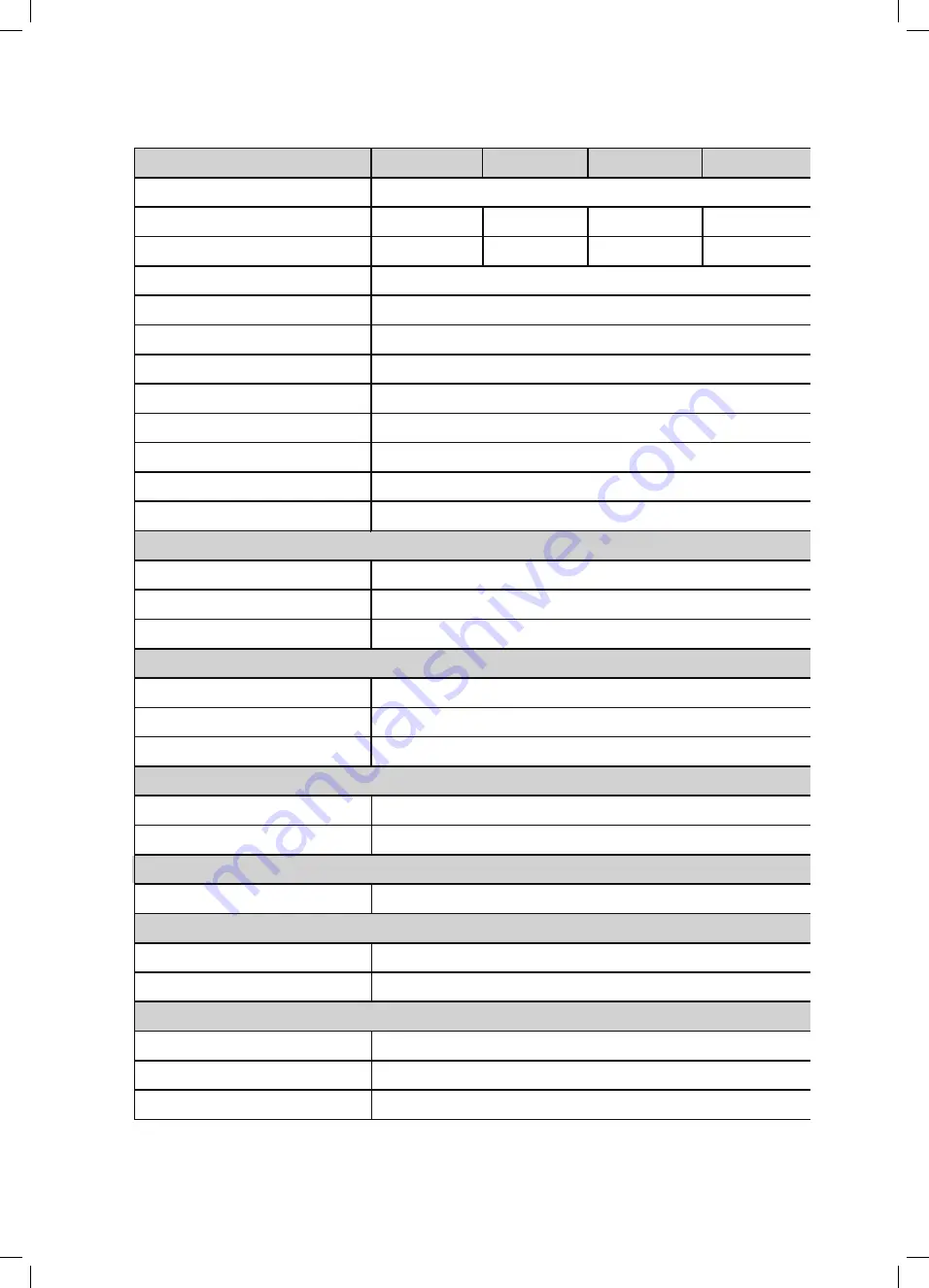
69
Unit
Power supply
Rated input
10.6kW
13.8kW
14.5kW
Rated Current
21.6A
16.8A
12.5kW
18kW
26kW
30kW
22kW
19.6A
22.8A
Norminal capacity
Dimensions (W×H×D)[mm]
Packing (W×H×D)[mm]
Heat exchanger
Electric heater
Internal water volume
Safety valve
Filter mesh
Min. water flow (flow switch)
Type
Max. head
Power input
Expanssion vessel
Volume
Max. operating pressure
Pre-charge pressure
Weight
Net weight
177kg
Gross weight
206kg
Connections
Water inlet/outlet
Operation range - water side
Operation range - air side
heating model
cooling model
heating model
cooling mode
Domestic hot water
+5
~
+60
℃
+5
~
+25
℃
-25
~
+35
℃
-5
~
+46
℃
-25
~
+43
℃
0.1MPa
5/4 BSP
12m
262W
8L
1.0MPa
0.3MPa
60
27L/min
Pump
Fixd speed pump
/
380-415V 3N
~
50Hz
Refer to the technical data
1129x1558x528
1220x1735x565
Plate heat exchanger
3.5L
14 TECHNICAL SPECIFICATIONS
70
15 INFORMATION SERVICING
1) Checks to the area
Prior to beginning work on systems containing flammable refrigerants, safety checks are necessary to ensure that the risk of
ignition is minmised. For repair to the refrigerating system, the following precautions shall be complied with prior to conducting
work on the system.
2) Work procedure
Works shall be undertaken under a controlled procedure so as to minimise the risk of a flammable gas or vapour being present
while the work is being performed.
3) General work area
All mintenance staff and others working in the local area shall be instructed on the nature of work being carried out. work in
confined sapces shall be avoided. The area around the work space shall be sectioned off. Ensure that the conditions within the
area have been made safe by control of flammable material.
4) Checking for presence of refrigerant
The area shall be checked with an appropriate refrigerant detector prior to and during work, to ensure the technician is aware
of potentially flammable atmospheres. Ensure that the leak detection equipment being used is suitable for use with flammable
refrigerants, i.e. no sparking, adequately sealed or intrinsically safe.
5) Presence of fire extinguisher
If any hot work is to be conducted on the refrigeration equipment or any associated parts, appropriate fire extinguishing
equipment shall be available to hand. Have a dry power or CO
2
fire extinguisher adjacent to the charging area.
6) No ignition sources
No person carrying out work in relation to a refrigeration system which involves exposing any pipe work that contains or has
contained flammable refrigerant shall use any sources of ignition in such a manner that it may lead to the risk of fire or explosion.
All possible ignition sources, including cigarette smoking, should be kept sufficiently far away from the site of installation, repair-
ing, removing and disposal, during which flammable refrigerant can possibly be released to the surrounding space. Prior to work
taking place, the area around the equipment is to be surveyed to make sure that there are no flammable hazards or ignition
risks. NO SMOKING signs shall be displayed.
a) During repairs to sealed components, all electrical supplies shall be disconnected from the equipment being worked upon
prior to any removal of sealed covers, etc. If it is absolutely necessary to have an electrical supply to equipment during servicing,
then a permanently operating form of leak detection shall be located at the most critical point to warn of a potentially hazardous
situation.
10) Repairs to sealed components
7) Ventilated area
Ensure that the area is in the open or that it it adequately ventilated before breaking into the system or conducting any hot work.
A degree of ventilation shall continue during the period that the work is carried out. The ventilation should safely disperse any
released refrigerant and preferably expel it externally into the atmosphere.
8) Checks to the refrigeration equipment
Where electrical components are being changed, they shall be fit for the purpose and to the correct specification. At all times
the manufacturer s maintenance and service guidelines shall be followed. If in doubt consult the manufacturer s technical
department for assistance. The following checks shall be applied to installations using flammable refrigerants:
9) Checks to electrical devices
Repair and maintenance to electrical components shall include initial safety checks and component inspection procedures. If a
fault exists that could compromise safety, then no electrical supply shall be connected to the circuit until it is satisfactorily dealt
with. If the fault cannot be corrected immediately but it is necessary to continue operation, and adequate temporary solution
shall be used. This shall be reported to the owner of the equipment so all parties are advised.
Initial safety checks shall include:
The charge size is in accordance with the room size within which the refrigerant containing parts are installed;
The ventilation machinery and outlets are operating adequately and are not obstructed;
If an indirect refrigerating circuit is being used, the secondary circuits shall be checked for the presence of refrigerant;
marking to the equipment continues to be visible and legible.
Marking and signs that are illegible shall be corrected;
Refrigeration pipe or components are installed in a position where they are unlikely to be exposed to any substance which
may corrode refrigerant containing components, unless the components are constructed of materials which are inherently
resistant to being corroded or are suitably protected against being so corroded.
That capacitors are discharged: this shall be done in a safe manner to avoid possibility of sparking;
That there no live electrical components and wiring are exposed while charging, recovering or purging the system;
That there is continuity of earth bonding.
153
152
Содержание MONO KHC-22RX3
Страница 1: ...INSTRUKCJA INSTALACYJNA INSTALATIONMANUAL POMPA CIEPŁA MONO MONO TYPE HEAT PUMP PL EN ...
Страница 2: ......
Страница 79: ...79 ...
Страница 80: ......
Страница 157: ...NOTE 157 ...
Страница 158: ...NOTE ...
Страница 159: ...16125300002403 V C ...
Страница 160: ...kaisai com ...