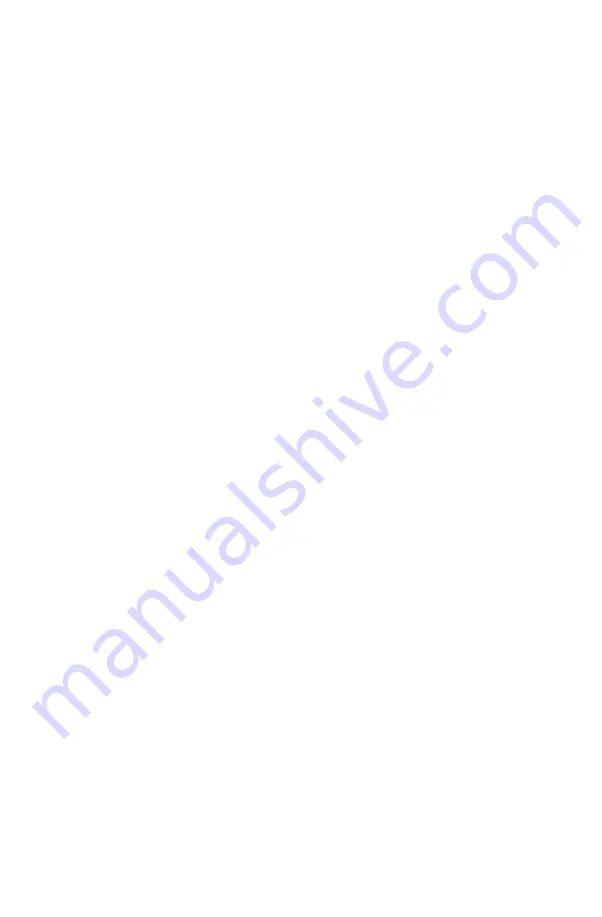
Instruction Manual
Section Five
II. GRINDING A HAND REAMER USED WITH CAST IRON,
STAINLESS STEEL, AND MONEL METALS
Generally there will be a few exceptions to the above procedure for hand reamers
for steel. The major difference will be final margin width left (primary relief)
on the reamer front leading taper and the remainder of the blades back from this
taper. As stated in the introduction, this figure can vary approximately from .012
inch for cast iron up to .038 inch for the Monel Metals depending on the size of the
reamer and the specific metal involved.
III. GRINDING A HAND REAMER USED WITH SOFT METALS
The procedure will be the same as in Part I, except that the primary relief land
is reduced to a "hair line" of no more than .002 inch for best results in most
instances. This can be achieved by grinding the primary relief as suggested in the
Table and then grinding a sufficient secondary clearance to reduce the primary
land to the desired width. Experience will tell the correct margin to leave for
the material being reamed.
IV. GRINDING A MACHINE OR CHUCKING REAMER FOR STEEL,
CAST IRON, MONEL METALS, AND OTHER SOFT METALS
A. The general grinding sequence is the same as discussed in Part I. Whenever
possible (AND ESPECIALLY FOR USE W I T H STEEL) it is desirable to cylin
drically grind the margin of the reamer. These reamers, as is true with most
reamers, have some amount of back taper. (See Part I, B above.) Chuck
ing reamers usually cut with the front chamfer, but a few cut with a slight
lead taper These portions of the reamer showing wear first need to be
sharpened more often.
1. Fluted Chucking Reamers: These reamers have either straight or tapered
shanks, spiral or straight flutes, and are primarily used in turret lathes and
screw machines for light metal removal. They have a gradual leading
chamfer or taper, and the relief back of the cutting edge (rear point of
chamfer) extends the full length of the land. Reproduce the lead taper
when sharpening after grinding the relief on the periphery back of the
cutting edge. Observe any back taper that may be present.
2. Rose Chucking Reamers: Reamers of this class are used in the same ma
chines as fluted chucking reamers, but they are designed for larger amounts
of metal removal and thus do all of their cutting on the end chamfer,
which is usually 45 degrees. If necessary, they should be cylindrically
ground back of the chamfer with a back taper of not more than .001 inch
per inch. There is no relief on the lands back of the chamfer. Use the
reamer clearance tables and sharpen the 45 degree chamfer with the
recommended clearance angle. (See Part 1-D and refer to Photo 50).
B. Observe the margin requirements where applicable as described in sections
I, II and III of this chapter for the different types of metals which are to
be machined.
V. GRINDING A STRAIGHT OR HELICAL FLUTE TAPER REAMER
A. Taper reamers are sharpened leaving a very narrow or hair line margin. This
margin requirement usually demands the use of a cup wheel and should not
exceed .003 inch for the largest reamers. Use the clearance table for reamers.
B. Use the same general procedure for sharpening as given in Part I above. The
set-up is shown in Photo 51. The taper should be checked after grinding the
first tooth even though the swivel table has been adjusted to the correct
—67—
Содержание B2000
Страница 14: ...Instruction Manual Section Three PHOTO 3 4 ...
Страница 24: ...Instruction Manual Section Four PHOTO 9 14 ...