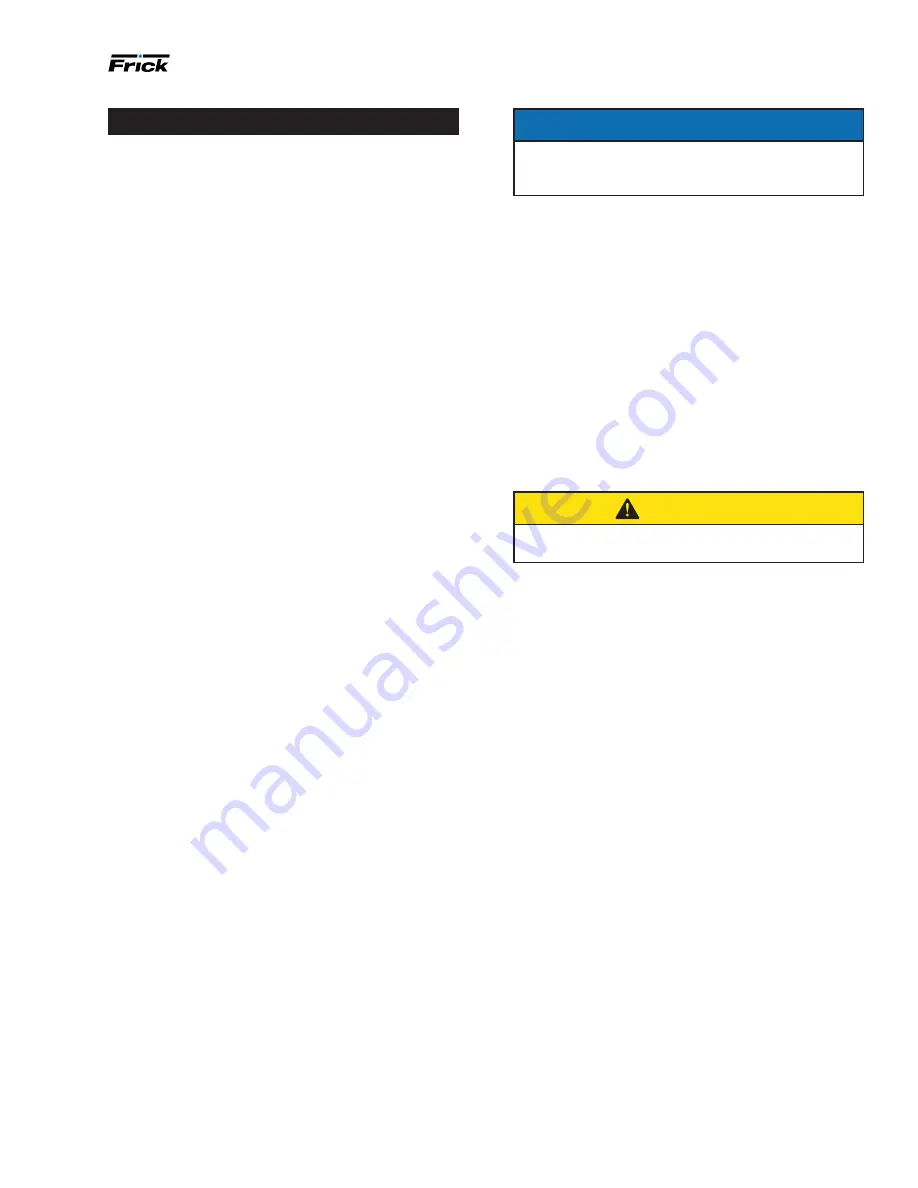
210.100-IOM (JUL 2021)
Page 41
AcuAir Hygienic Air Units
Maintenance
Maintenance
Daily operation and routine
maintenance
Inspect, clean, and lubricate the AcuAir
®
unit on a periodic
basis. The required services and frequency for the various
components are summarized in
A daily AcuAir
®
system operations log is a good method to
assure that no problems develop that may go unchecked.
Make entries to this log during each shift. Enter any nota-
tions as they occur, or as internal policy dictates. It is
essential that the maintenance manager examine all nota-
tions (from the previous 24 hr) on a daily basis.
As weather and safety allow, visually check the AcuAir
®
unit once each shift (daily at a minimum) to examine op-
erating conditions. Log unusual leaks, noise, vibration, part
damage or failures, or vandalism and investigate immedi-
ately. Initiate corrective action immediately.
Ensure components of the AcuAir
®
unit are also part of
the daily operational checks conducted of the equipment
on site. In particular, filtration performance is important
for satisfactory and problem-free AcuAir
®
hygienic system
operation.
Use the
schedule to develop the site
specific hygienic air unit inspection log and maintenance
schedule.
Maintaining the coils
An AcuAir
®
air unit's operational readiness is dependent on
the condition of the fin-coil heat exchanger(s). Coils that
are dirty, blocked from airflow, or physically damaged may
affect overall heat transfer capability of the AcuAir
®
system
to a significant degree.
Regularly visually inspect both the inlet and leaving sides
of the cooling coils, and the refrigerant pipe connections.
Conduct these inspections at least as frequently as indi-
cated in the maintenance schedule in this IOM. Remove
any airborne debris that may have collected on the face of
the fin coils. If site conditions require coil cleaning mea
-
sures following each of the routine inspections, it may be
necessary to increase the frequency of the inspections.
A standard refrigerated food processing facility has stain-
less steel food contact surfaces and clean work spaces.
Evaporators trap airborne contaminants and corrosive
elements in the coils. Dirty coils are also unsanitary. They
must be cleaned regularly with simple, gentle, wash and
rinse procedures.
Refrigerant could leak into the process airstream and
come in contact with food products and personnel. As
such, correct maintenance of refrigerant coils is essential
to prevent corrosion and leaks that result in product loss
and to ensure the safety of plant personnel.
For all coils, chlorine-based cleansing solutions, acidic
cleansing solutions and highly alkaline cleansing solutions
are hazardous to the coil's integrity. Use a mildly alkaline
cleanser. Consult with your chemical supplier and read the
Material Safety Data Sheet for your cleansing solution.
NOTICE
Air units move air (and airborne contaminants)
across the coil. Protect the coil from corrosion by
washing and rinsing frequently.
Analyze the water for washing the coils before use to de-
termine its suitability. Ensure it does not contain dissolved
chemicals or organisms. Contact a specialist to test the
water, then follow their guidance. Establish and follow a
regular testing and treatment schedule.
A certified or factory-trained service person may can
judge if further cleaning or repair of an AcuAir
®
system coil
is necessary. Contact the local AcuAir
®
representative if a
coil or its connections appears to have been significantly
damaged.
Do not allow ice buildup. If a coil remains partially frosted
after a defrost, it is unlikely to ever completely remove
accumulated frost and ice in a subsequent defrost. If a coil
is allowed to build ice into a solid block, the ice can cause
stresses to develop that are capable of crushing or ruptur-
ing coil tubes and piping.
CAUTION
Never take shortcuts to clear ice from a coil by ap-
plying an open flame to melt ice or frost.
Maintaining the dampers
General maintenance
Dampers require correct maintenance in order to function
correctly. Clean and lubricate blade shafts, linkages, stain-
less steel side seals (if applicable), and other moving parts
as indicated in
.
A light molybdenum oil in aerosol cans is preferable
because the jet nozzle permits pinpointing the stream of
lubricant where required. It usually contains an evaporat-
ing solvent and dries to a non-oily film, which does not at
-
tract dirt. For dampers located in difficult or impossible to
reach locations, field access panels or doors are required
as installed by others.
Periodic inspections
Check and service all automatic dampers on a regular
schedule. The suggested interval is monthly and must never
exceed three months. Malfunctioning dampers can lead to
incorrect control of space temperatures, excessive infiltra
-
tion, and increased energy costs.
Inspection checklist
At a minimum, include the following items in scheduled
inspections:
• Observe damper motors and actuators through an op-
erating cycle to check for defects and binding. Inspect
mounting bolts for integrity.
• Adjust actuator linkages so those dampers open and
close fully for given stroke.
• Verify tightness of closed blades – readjust linkage for
any blades that may not close fully.