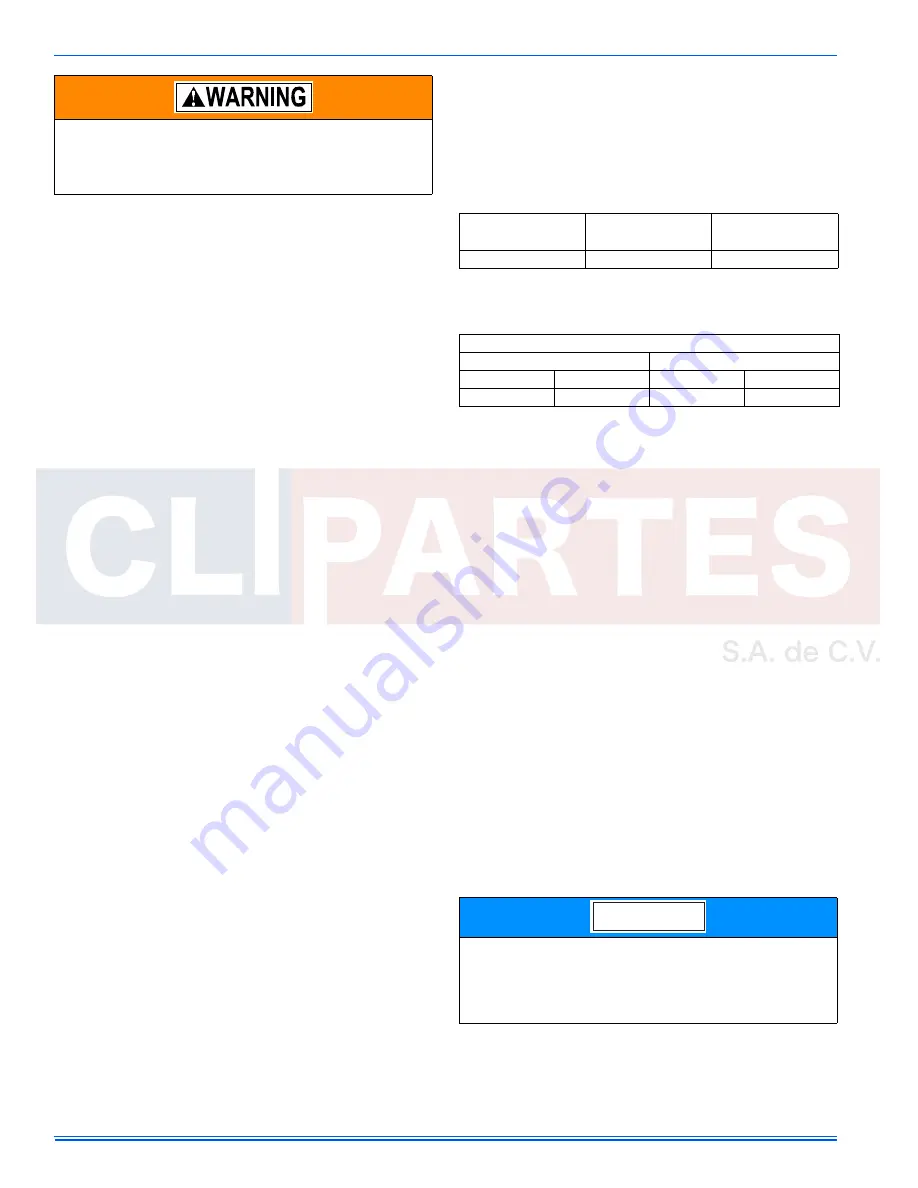
536636-UIM-A-1209
2
Johnson Controls Unitary Products
1.
Install this air handler only in a location and position as specified in
SECTION III of these instructions.
2.
Always install the air handler to operate within the air handler’s
intended maximum outlet air temperature. Only connect the air
handler to a duct system which has an external static pressure
within the allowable range, as specified on the air handler rating
plate.
3.
When an air handler is installed so that supply ducts carry air cir-
culated by the air handler to areas outside the space containing
the air handler, the return air shall also be handled by duct(s)
sealed to the air handler casing and terminating in the space to be
cooled/heated.
4.
The air handler is not to be used for temporary heating of buildings
or structures under construction.
5.
The size of the unit should be based on an acceptable heat loss or
gain calculation for the structure. ACCA, Manual J or other
approved methods may be used.
SAFETY REQUIREMENTS
1.
This air handler should be installed in accordance with all national
and local building/safety codes and requirements, local plumbing
or wastewater codes, and other applicable codes.
2.
Refer to the unit rating plate for the air handler model number, and
then see the dimensions page of this instruction for supply air ple-
num dimensions in Figure 4. The plenum must be installed accord-
ing to the instructions.
3.
Provide clearances from combustible materials as listed under
Clearances to Combustibles.
4.
Provide clearances for servicing ensuring that service access is
allowed for electric heaters and blower.
5.
Failure to carefully read and follow all instructions in this manual
can result in air handler malfunction, death, personal injury and/or
property damage.
6.
Check the rating plate and power supply to be sure that the electri-
cal characteristics match.
7.
Air handler shall be installed so the electrical components are pro-
tected from water.
8.
Installing and servicing heating/cooling equipment can be hazard-
ous due to the electrical components. Only trained and qualified
personnel should install, repair, or service heating/cooling equip-
ment. Untrained service personnel can perform basic maintenance
functions such as cleaning and replacing the air filters. When
working on heating/cooling equipment, observe precautions in the
manuals and on the labels attached to the unit and other safety
precautions that may apply.
9.
These instructions cover minimum requirements and conform to
existing national standards and safety codes. In some instances
these instructions exceed certain local codes and ordinances,
especially those who have not kept up with changing residential
and non-HUD modular home construction practices. These
instructions are required as a minimum for a safe installation.
INSPECTION
As soon as a unit is received, it should be inspected for possible dam-
age during transit. If damage is evident, the extent of the damage
should be noted on the carrier’s freight bill. A separate request for
inspection by the carrier’s agent should be made in writing. Also, before
installation the unit should be checked for screws or bolts, which may
have loosened in transit. There are no shipping or spacer brackets
which need to be removed.
Also check to be sure all accessories such as heater kits, suspension
kits, and coils are available. Installation of these accessories or field
conversion of the unit should be accomplished before setting the unit in
place or connecting any wiring, electric heat, ducts or piping.
LIMITATIONS
These units must be wired and installed in accordance with all national
and local safety codes.
Voltage limits are as follows:
Airflow must be within the minimum and maximum limits approved for
electric heat, evaporator coils and outdoor units.
SECTION III: UNIT INSTALLATION
CLEARANCES
Clearances must be taken into consideration, and provided for as fol-
lows:
1.
Refrigerant piping and connections - minimum 12” recommended.
2.
Maintenance and servicing access - minimum 36” from front of unit
recommended for blower motor / coil replacement.
3.
Condensate drain lines routed to clear filter and panel access.
4.
Filter removal - minimum 36” recommended.
5.
The ductwork and plenum connected to this unit are designed for
zero clearance to combustible materials.
6.
A combustible floor base accessory is available for downflow
applications of this unit, if required by local code.
LOCATION
Location is usually predetermined. Check with owner’s or dealer’s
installation plans. If location has not been decided, consider the follow-
ing in choosing a suitable location:
1.
Select a location with adequate structural support, space for ser-
vice access, clearance for air return and supply duct connections.
2.
Use hanging brackets to wall mount this single piece air handler
unit, is not recommended.
3.
Normal operating sound levels may be objectionable if the air han-
dler is placed directly over some rooms such as bedrooms, study,
etc.
4.
Select a location that will permit installation of condensate line to
an open drain or outdoors allowing condensate to drain away from
structure.
5.
Proper electrical supply must be available.
6.
If unit is located in an area of high humidity (ie: an unconditioned
garage or attic), nuisance sweating of casing may occur. On these
installations, unit duct connections and other openings should be
properly sealed and a wrap of 2” fiberglass insulation with vinyl
vapor barrier should be used.
FIRE OR ELECTRICAL HAZARD
Failure to follow the safety warnings exactly could result in serious
injury, death or property damage.
A fire or electrical hazard may result causing property damage, per-
sonal injury or loss of life.
Air Handler Voltage
Voltage code
1
Normal Operating
Voltage Range
1. Rated in accordance with ARI Standard 110, utilization range “A”.
208/230-1-60
06
187-253
Entering Air Temperature Limits
Wet Bulb Temp.°F
Dry Bulb Temp. °F
Min.
Max.
Min.
Max.
57
72
65
95
The primary and secondary drain line must be trapped to allow
proper drainage of condensate water. If the secondary drain line is
not used, it must be capped. The coil is provided with a secondary
drain. It should be piped to a location that will give the occupant a
visual warning that the primary drain is clogged. If the secondary
drain is not used it must be capped.
NOTICE