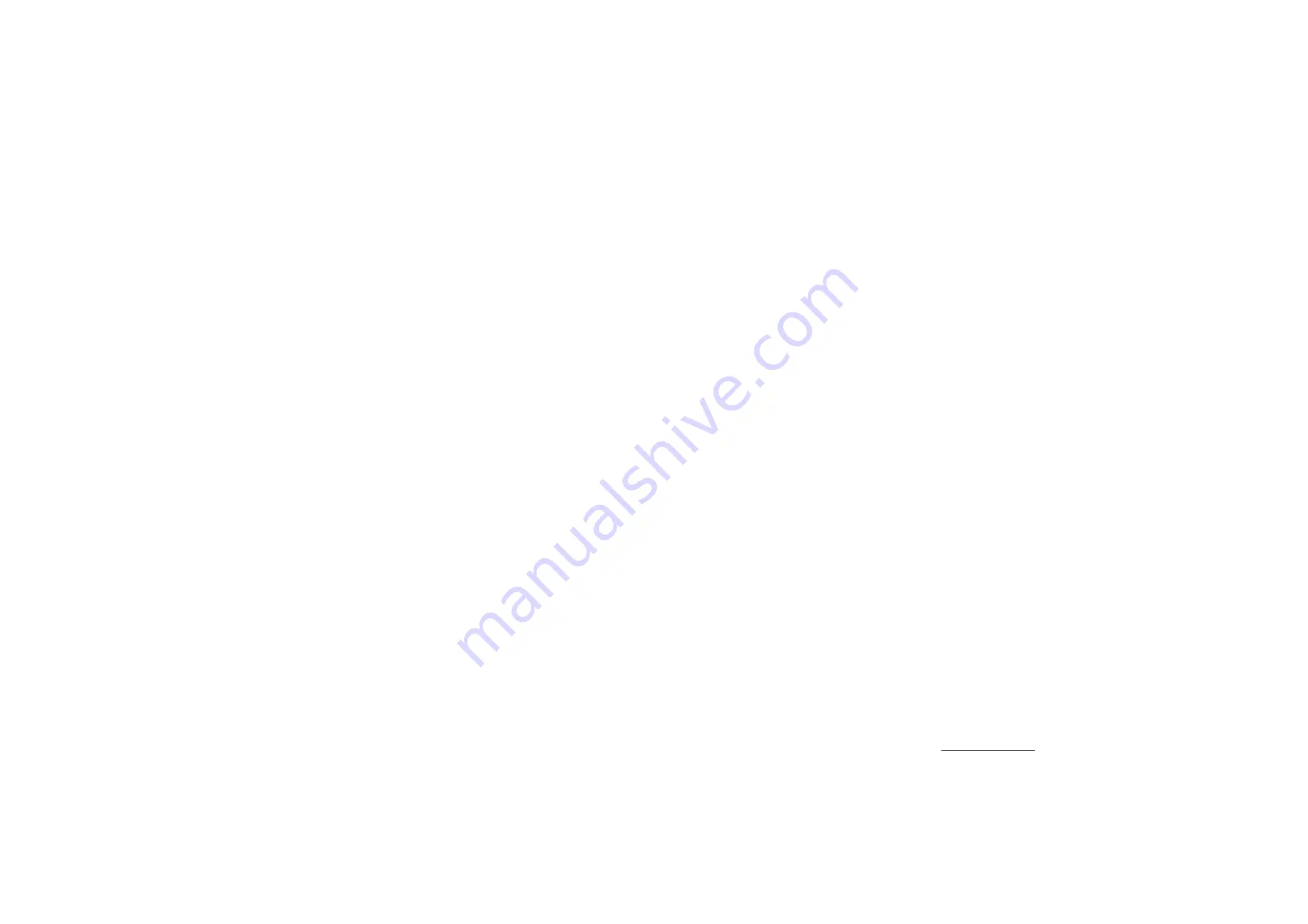
14
8.10
TIME CONTROL and SWITCH REMOVAL:
8.10.1 Ensure that the electrical supply is isolated.
8.10.2 Remove the appliance louvre door, release the 2 x securing screws and hinge down the fan chamber door.
Time Control
removal:
8.10.3 Disconnect conductors ‘
C1
’, ‘
C2
’, ‘
C3
’ and ‘
C5
’ from the Time control.
8.10.4 Release the 2 x fixing screws, and withdraw the Time control.
8.10.5 Refitting or replacement is in reverse order.
8.10.6 Set the Time Control to the required ON and OFF times.
8.10.7 Set the Time Control to the correct time.
Switch removal:
8.10.8
Disconnect the conductors from the switch terminals.
8.10.9
Depress the retaining clips and press the switch out of the fascia panel.
8.10.10
Refitting or replacement is in reverse order.
WARNING: The fascia panel is held in place by push fit retainers which must be removed with caution to avoid
causing damage to the support pins. Removal of the fascia is not advised unless it is intended to be replaced.
8.11
FAN DELAY CONTROL/LIMIT SWITCH REMOVAL:
8.11.1 Ensure that the electrical supply is isolated.
8.11.2 Remove the appliance louvre door, release the 2 x securing screws and hinge down the fan chamber door.
8.11.3 Disconnect the following at the Electrical panel:
a.
Limit Switch from connection block terminals ‘
13
’ and
‘
14
’,
b.
Fan Delay Control from connection block terminals ‘
18
’ and
‘
17
’,
c.
Earth connection from common earth stud.
8.11.4 Release 2 x 4mm screws securing Limit Switch mounting plate, and withdraw the control from the appliance by
drawing the conductors through the grommet in the fan chamber floor.
8.11.5 Refitting or replacement is in reverse order.
8.12
SPILLAGE MONITORING DEVICE (TTB) REMOVAL:
8.12.1 Ensure that the electrical supply is isolated.
8.12.2 Remove the appliance louvre door, release the 2 x securing screws and hinge down the fan chamber door.
8.12.3 Disconnect the TTB from its conductors.
8.12.4 Release 2 x screws securing the TTB Bracket to the fan chamber floor, and withdraw TTB Bracket.
8.12.5 Refitting or replacement is in reverse order.
8.13
HEAT EXCHANGER ACCESS:
8.13.1 Ensure that the electrical supply is isolated.
8.13.2 Remove the appliance louvre door.
8.13.3 Remove the Burner and Controls Assembly as detailed in sect 8.2.
8.13.4 Release the 4 screws securing the combustion chamber heat shield, and withdraw the heat shield.
8.13.5 Release the 4 screws securing the top access cover plate, and withdraw the cover plate and gasket
8.13.6 Release the 4 screws securing the heat exchanger top sealing plate, and withdraw the sealing plate and gasket.
8.13.7 Reassembly is in reverse order.
NOTE: When reassembling, ensure that the gaskets are soundly sealed, and fully re-commission the heater.
7
5.1.15
Important:
Before installing the appliance, carry out a visual check of the flue system as directed in the relevant
section of BS5440 Pt. 1, then check the flue performance as follows:-
a.
Close all doors and windows in the room in which the appliance is to be installed.
b.
Introduce some heat into the flue, using a blow torch or other means.
c.
Carry out a flow visualisation check with a smoke pellet at the intended position for the appliance. Ensure
that there is discharge of smoke from the correct terminal only, and no spillage into the room.
Smoke coming out of other than the correct terminal only, or a down draught or ‘no flow’ condition,
indicates that the flue has failed the test, and the appliance shall not be connected until the defect has been
found and rectified, and the test satisfactorily completed.
5.2
ELECTRICAL
5.2.1
Mains.
a.
The heater is supplied with mains cable (PVC sheathed, heat resisting to 85
o
C), 3-core Brown-Blue-
Green/Yellow, 6A, 0.75mm
2
), connected to a terminal block and exiting through the heater at the right
hand top. The cable is suitable for a 230V 50Hz supply and shall be connected to the fixed wiring
using a double pole switched, fused spur, incorporating a protective earth link. The fuse fitted shall be
rated 5A to BS 1362 Connections shall be in accordance with the current edition of I.E.E Regulations BS
7671.
b.
Fan Delay Controls and Limit Switch are not adjustable and are set as follows:
i.
Fan Delay Control closes at 54
O
C± 4.5
O
C; opens at 40
O
C±3
O
C.
ii.
Limit Switch opens at 80
O
C; closes at 60
O
C.
c.
A 24V room thermostat (not supplied), that complies with BS 800 BS 3955 and BS 4201 is essential to
ensure close control of comfort conditions. An anticipator is located within the thermostat and is graded
in amps. The anticipator should be checked and adjusted to 0.2A.
5.2.2
Room Thermostat and its location.
a.
The Room Thermostat should be located where there is free air circulation approx. 1.5m (5ft) from the
floor.
b.
Avoid the following locations:-
i.
In a room where temperature is greatly affected by the sun or any other heat source, e.g. radiant
fire, wall light fittings or TV set.
ii.
Near an outside door or windows, or on an outside wall.
iii.
Where affected by warm air ducts, diffusers, waste pipes or the heater itself.
iv.
Where subject to vibration.
c.
Connect Room thermostat wires to control panel terminals ‘7’ and ‘8’ (see Fig. 6 or 7).
5.3
GAS
(See BS5864 and BS 6891)
5.3.1
An independent gas supply pipe from the meter is to be preferred wherever possible. When this is not possible,
the pipe must be capable of taking the complete input of the heater and all other gas appliances being served by
this same pipe. This supply should be suitably sized to conform to British Standards requirements of no more than
2.5 mbar (0.4in wg) pressure drop (See table of discharge in BS 5482 Part 1.).
5.3.2
The 1/2in union gas cock (supplied) must be fitted to the gas inlet of the heater for easy isolation during
servicing. The gas pipe should be so fitted and installed as to be durable, substantial and gas tight. To assist in
determining where a gas connection may not be tight, a leak detection fluid should be applied around the
connection. Under no circumstances should a flame be used to locate a gas leak. Gas entry to the air heater is
through either side to a Rc1/2 (1/2in BSP. external [taper] thread).
6.
COMMISSIONING
6.1
PREPARATION:
6.1.1
Ensure that:
a.
Gas and Electrical supplies are
OFF.
b.
Filter, fan and fan compartments are free from obstructions.
c.
All registers or grilles are open and conform to design specifications.
d.
Return, relief and ventilation air installations are adequate.