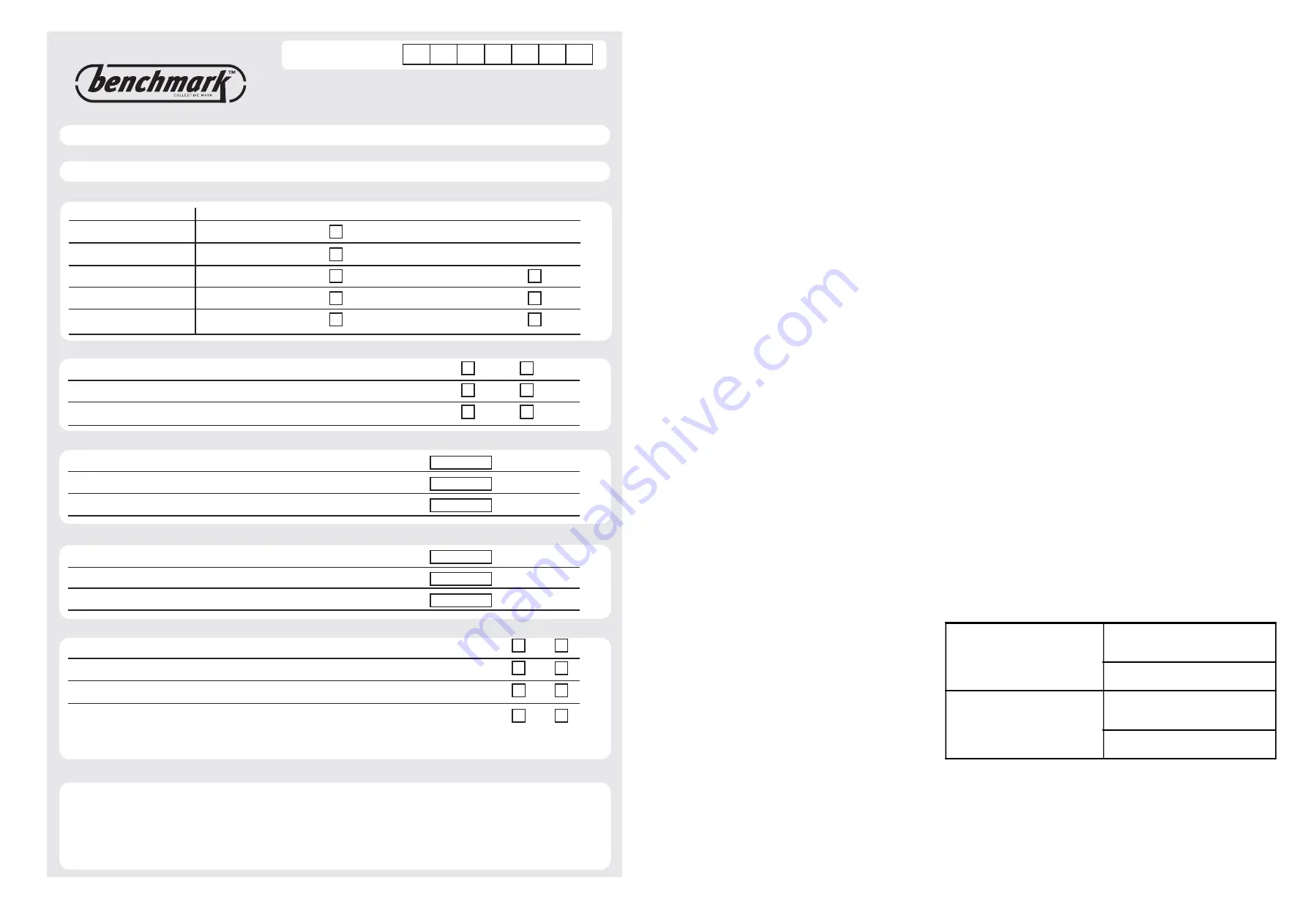
3
22
2.4
In airing cupboard installations, the part used as the air heater compartment must comply with the relevant section of BS
5864 and must be completely separated by either a non-combustible partition or a perforated metal partition with the
perforations not exceeding 13mm (1/2in). The secondary flue must be a tight fit where it passes through the partition and
must be suitably protected (see BS 5440: Part 1).
2.5
In under-stairs installations, the compartment must comply with the relevant section of BS 5864, provided that in addition all
internal surfaces (including the base) are non-combustible or lined with non-combustible material. This requirement is
applicable only to dwellings of more than two storeys.
2.6
In free-standing installations, only one or two walls will be in close proximity to the air heater and these MUST be non-
combustible.
2.7
Where the air heater is to be installed onto a combustible surface and under-floor ducting used, a suitable base tray (BT65/
90) MUST be used in order to provide insulation.
NB where a base plenum is used no base tray is required!
3.
VENTILATION AIR
3.1
When installed in a compartment two permanent ventilation openings into the compartment are required, one at high level
and one at low level. The minimum effective areas specified in Table 1 are related to the rated heat input of the air heater.
4.
DUCT SYSTEM
(See British Design Manual - Gas fired Warm Air Heating)
4.1
RETURN AIR
4.1.1
Room-sealed appliances may be installed without return air ducting, provided that the path between the return air
grille and the appliance return air inlet is protected in such a manner that the required air-flow will be maintained at all
times. The return air grille MUST have a free area of not less than 2118cm
2
(328in
2
). It is recommended that the return
air duct not be routed directly from the main living area, but from a convenient central area serving the remainder of
the dwelling.
4.1.2
The return air system should be constructed of fire-resistant material. The flue shall not be run through an area
serving as a return air plenum. It is extremely important that the correct size of return air grilles and ducting is used.
For heaters on maximum output the return air duct size should not be less than the equivalent of 400mm x 300mm
(16" x 12"). If flexible duct is used the duct diameter should not be less than 406mm (16") dia. The return air grille
should have a free area of not less than 2118cm
2
(328in
2
).
4.1.3
An adequate and unobstructed return air path is essential from areas not served by a directly ducted return and to
which warm air is delivered. All such rooms should be fitted with relief grilles which have a free area of 0.0088m
2
/kW
(1in
2
/250Btu/h) of heat supplied to the room. The only exceptions are kitchens, bathrooms and WC.’s.
4.1.4
The return air duct should allow for ease of removal for access to the flue.
4.1.5
All duct work in the room or internal space in which the heater is installed shall be mechanically secured and sealed
with ducting tape.
4.2
WARM DELIVERED AIR
4.2.1
All duct work, including riser ducts, should be fully insulated with 50mm (2in) fibreglass or similar. If short extended
duct runs are taken below floor level these should be similarly insulated and in addition wrapped with a sound
vapour proof barrier. They must also be protected from crushing.
4.2.2
The duct system should be carefully designed (as given in the guidelines in the British System Design Manual) to
suit the needs of specific heating requirements and building layout. The type of duct system (e.g. radial/extended
plenum/ stepped) should be installed
using the least number of fittings to
minimise airflow resistance. The base
duct, which equalises the air pressure
to supply ducts, must be constructed
to support the weight of the heater,
which must be sealed using self-
adhesive foam strip, ducting tape or
sealing compound. All ducting and
blanking plates must be mechanically
secured and sealed.
VENTILATED FROM INSIDE
BUILDING
Low level grille 297cm
2
(48in
2
)
High level grille 297cm
2
(48in
2
)
VENTILATED FROM OUTSIDE
BUILDING
Low level grille 149cm
2
(24in
2
)
High level grille 149cm
2
(24in
2
)
Table 1:
Minimum Effective Areas
WARM AIR HEATER AND CIRCULATOR
COMMISSIONING CHECKLIST
WARM AIR UNIT
BENCHMARK Number
HOT WATER GENERATOR
CONTROLS
to comply with the Building Regulations, each section must have a tick on one or other of the boxes
APPLIANCE SERIAL NUMBER: . . . . . . . . . . . . . . . . . . . . . . . . . . . . . . . . . . . . . . . . . . . . . . . . . . . . . . . . . . NOTIFICATION No: . . . . . . . . . . . . . . . . . . . . . . . . . . . .
APPLIANCE SERIAL NUMBER: . . . . . . . . . . . . . . . . . . . . . . . . . . . . . . . . . . . . . . . . . . . . . . . . . . . . . . . . . . NOTIFICATION No: . . . . . . . . . . . . . . . . . . . . . . . . . . . .
REQUIREMENT
1. Time & temp control to heating
2. Time & temp control to hot water
3. Heating zone valves
4. Thermostatic Radiator Valves
5. Boiler interlock
MEASURES PROVIDED
Room stat & integral timer
Cylinder stat & Integral timer
Fitted
Not Required
Fitted
Not Required
Provided
Not Required
FOR WARM AIR HEATERS ONLY
Has the system been balanced in accordance with the heater manufacturer’s instructions?
YES
NO
Was an anemometer used?
YES
NO
Have balancing dampers been fitted?
YES
NO
FOR WARM AIR HEATING: MEASURE AND RECORD
Burner operating pressure
Mbar
Heat input
KW
Temperature differential between return air inlet and nearest outlet
o
C
FOR HOT WATER GENERATORS: MEASURE AND RECORD
Burner operating pressure
Mbar
Heat input
KW
Water flow temperature
o
C
Does the heating & hot water system comply with the appropriate building regulations?
YES
NO
Has the appliance and associated controls been installed & commissioned in accordance with manufacturer’s instructions?
YES
NO
Have you demonstrated the operation of the appliance & system controls to the customer?
YES
NO
Have you left all the manufacturer’s literature with the customer
YES
NO
Competent person’s signature . . . . . . . . . . . . . . . . . . . . . . . . . . . . . . . . . . . . . . . . . . . . Customer’s Signature . . . . . . . . . . . . . . . . . . . . . . . . . . . . . . . . . . . . . . . . . . .
(To confirm demonstration of equipment & receipt of appliance instructions)
COMMISSIONING ENGINEER’S DETAILS
Name . . . . . . . . . . . . . . . . . . . . . . . . . . . . . . . . . . . . . . . . . . . . . . . . . . . . . . . . . . . . . . . . . . . . . . . . . . . . . . . . Commissioning Date . . . . . . . . . . . . . . . . . . . . . . . . . . . .
Address . . . . . . . . . . . . . . . . . . . . . . . . . . . . . . . . . . . . . . . . . . . . . . . . . . . . . . . . . . . . . . . . . . . . . . . . . . . . . . . . . . . . . . . . . . . . . . . . . . . . . . . . . . . . . . . . . . . . . . . . . . . . .
. . . . . . . . . . . . . . . . . . . . . . . . . . . . . . . . . . . . . . . . . . . . . . . . . . . . . . . . . . . . . . . . . . . . . . . . . . . . . . . . . . . . . Tel No . . . . . . . . . . . . . . . . . . . . . . . . . . . . . . . . . . . . . . . .
CORGI REGISTRATION No . . . . . . . . . . . . . . . . . . . . . . . . . . . . . . . . . . . . . . . . . . . . . . . . . . . . . . . . . . . . . CORGI ID SERIAL No . . . . . . . . . . . . . . . . . . . . . . . . . . .
FOR ALL PRODUCTS