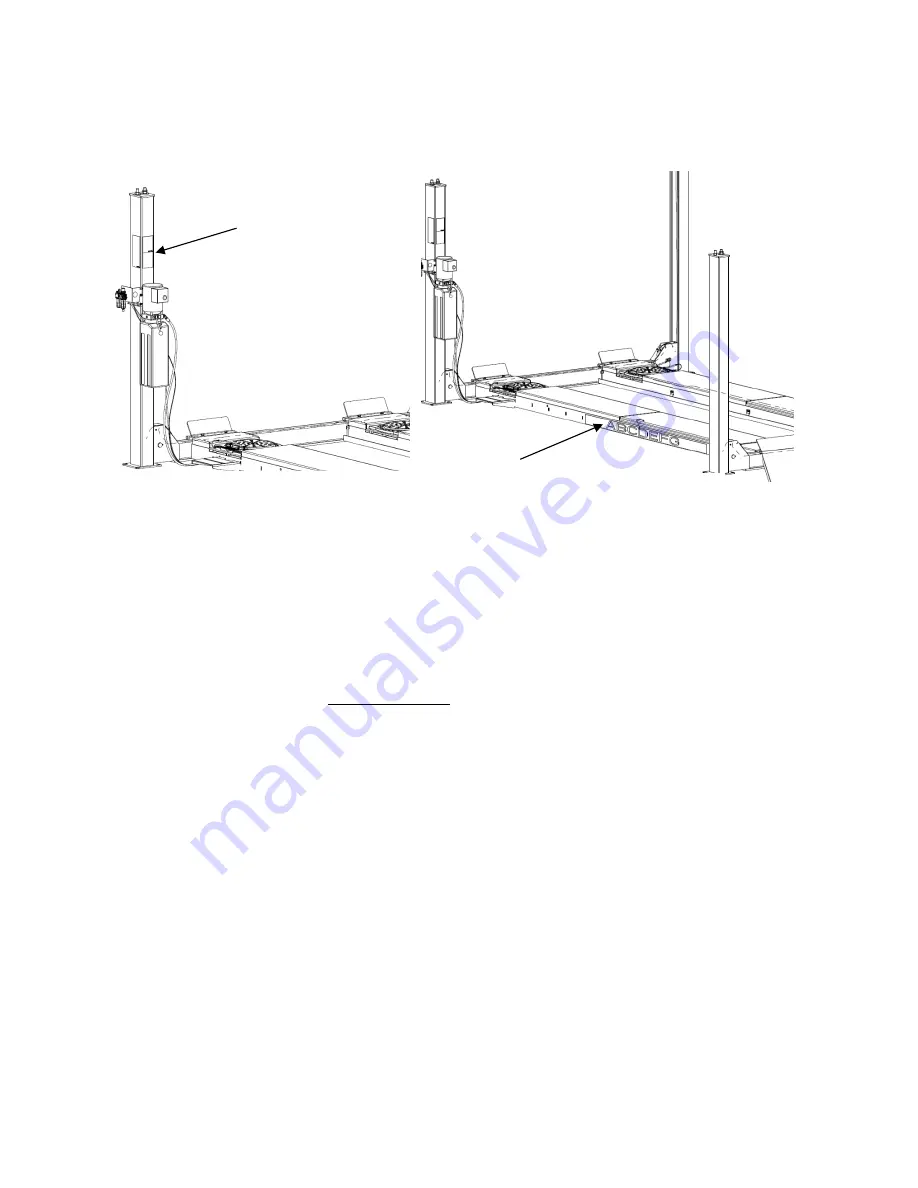
- 23 -
Figure 23 -
Logo Decal
Placement
7.9 DECAL PLACEMENT
Clean the column surface before placing any decals.
Install safety decals (NOTICE / CAUTION / WARNING) at the power unit as shown in
Figure 22
below. An illustration of these safety decals can be found on page 4.
Place a logo decal on the outside deck as shown in
Figure 23
.
NOTE
: Logo decal may cover some step holes on the side of decks.
8. OWNER/USER CHECKLIST
SAVE THESE INSTRUCTIONS
deliver them to owner/user/employee along with other
materials furnished with this lift.
Demonstrate the operation of the lift to the owner/operator and review correct and safe
lifting procedures using the
Lifting It Right
booklet as a guide.
Complete the Installation Checklist/Warranty Validation questionnaire with the owner.
Review the terms of the warranty registration card, and return the card and a copy of the
questionnaires to:
Snap-on Equipment
309 EXCHANGE AVENUE
CONWAY, ARKANSAS, 72032
9. OPERTATION PROCEDURE
Safety Notices and Decals
This product is furnished with graphic safety warning labels, which are reproduced
on page 3 of these instructions. Do not remove or deface these warning labels or
allow them to be removed or defaced. For your safety, and the safety of others, read
and understand all the safety notices and decals included.
Owner/User Responsibilities
This lift has been designed and constructed according to ANSI/ALI ALCTV-2017 standard.
The standard applies to lift manufactures, as well as to owners and employees. The
owner/employee’s responsibilities as prescribed by ANSI/ALI ALOIM-2013, are
summarized below. For exact wording refer to the actual standard provided with this
manual in the literature pack.
Figure 22 -
Safety Decal
Placement
Safety Decal
Logo Decal
Содержание EELR369A
Страница 4: ... 4 1 2 SAFETY WARNING LABELS FOR 4 POST SURFACE MOUNTED ROLL ON LIFTS SAVE THESE INSTRUCTIONS ...
Страница 8: ... 8 6 ALIGNMENT LAYOUT Aligner mount holes Figure 2 ...
Страница 20: ... 20 Figure 18 ...
Страница 26: ... 26 10 PARTS LIST 10 1 LIFT ASSEMBLY Figure 24 ...
Страница 38: ... 38 Jack Beam Installation Operation and Maintenance Manual Parts Breakdown ...
Страница 41: ... 41 LAYOUT VIEW Figure 1 ...