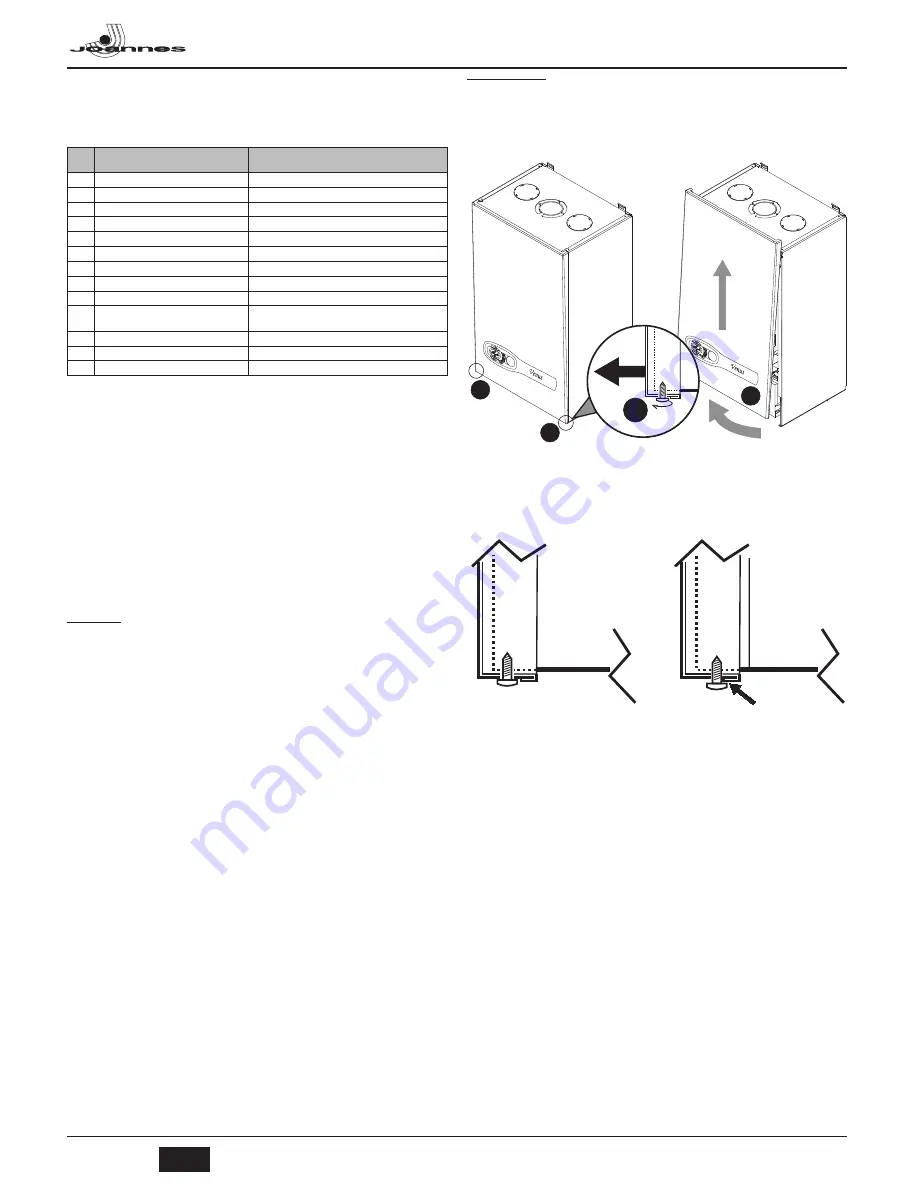
VENUS BA MS 24- 34
26
EN
cod. 3541I710 - Rev. 00 - 06/2016
“In” - Information Menu
13 pieces of information are available.
Press the Heating buttons to scroll the list of information in increasing or decreasing or-
der. Press the DHW buttons to display the value.
Notes:
1.
In case of damaged sensor, the card displays hyphens.
Press the Reset button to return to the Service Menu. Press the Reset button for 20 sec-
onds to exit the card Service Menu, or exiting occurs automatically after 15 minutes.
"Hi" - History Menu
The card can store the last 11 faults: the History datum item H1 represents the most re-
cent fault that occurred, whereas the History datum item H10 represents the least recent.
The codes of the faults saved are also displayed in the relevant menu of the Remote Tim-
er Control.
Press the Heating buttons to scroll the list of faults in increasing or decreasing order.
Press the DHW buttons to display the value.
Press the Reset button to return to the Service Menu. Press the Reset button for 20 sec-
onds to exit the card Service Menu, or exiting occurs automatically after 15 minutes.
"rE" - History Reset
By pressing the Eco/comfort button for 3 seconds it will be possible to delete all the faults
stored in the History Menu: the card will automatically exit the Service Menu, so as to
confirm the operation.
Press the Reset button for 20 seconds to exit the card Service Menu, or exiting occurs
automatically after 15 minutes.
4.2 Startup
Before lighting the boiler
•
Check the seal of the gas system.
•
Check correct prefilling of the expansion tank.
•
Fill the water system and make sure all air contained in the boiler and the system
has been vented.
•
Make sure there are no water leaks in the system, DHW circuits, connections or boiler.
•
Check correct connection of the electrical system and efficiency of the earthing system.
•
Make sure the gas pressure for heating is that required.
•
Make sure there are no flammable liquids or materials in the immediate vicinity of
the boiler
Checks during operation
•
Switch the unit on.
•
Check the tightness of the fuel circuit and water systems.
•
Check the efficiency of the flue and air/fume ducts while the boiler is working.
•
Check the correct tightness and efficiency of the condensate removal system and trap.
•
Make sure the water is circulating properly between the boiler and systems.
•
Make sure the gas valve modulates correctly in heating and domestic hot water pro-
duction.
•
Check proper lighting of the boiler by turning it on and off several times with the room
thermostat or remote control.
•
Make sure the fuel consumption indicated on the meter matches that given in the
technical data table on cap. 5.
•
Make sure that with no heating demand the burner correctly lights on opening a hot
water tap. Check that the heating circulating pump stops on opening a hot water tap
during heating operation and there is a regular production of hot water.
•
Check correct programming of the parameters and carry out any required customi-
sation (compensation curve, power, temperatures, etc.).
4.3 Maintenance
Opening the front panel
To open the boiler casing:
1.
Partially undo the screws
A
(see fig. 24).
2.
Pull the panel
B
towards you and release it from the upper fastenings.
B
Before carrying out any operation inside the boiler, disconnect the power supply
and turn off the gas valve upstream
fig. 24 - Front panel opening
B
On this unit, the casing also acts as a sealed chamber. After any opera-
tion involving opening the boiler, carefully check the correct refitting of
the front panel and its seal.
Proceed in reverse order to refit the front panel. Make sure it is correctly hooked to the
upper fastenings and is correctly positioned at the sides. When tightened, the head of
screw "A" must not be below the lower fold (see fig. 25).
fig. 25 - Correct position of front panel
Periodical check
To ensure proper operation of the unit over time, have qualified personnel carry out a
yearly inspection, providing for the following checks:
•
The control and safety devices (gas valve, flow meter, thermostats, etc.) must func-
tion correctly
•
The fume exhaust circuit must be perfectly efficient
•
The sealed chamber must be tight
•
The air-fume end piece and ducts must be free of obstructions and leaks
•
The burner and exchanger must be clean and free of deposits For possible cleaning
do not use chemical products or wire brushes
•
The electrode must be properly positioned and free of scale
•
The gas and water systems must be tight.
•
The water pressure in the cold water system must be about 1 bar; otherwise, bring
it to that value
•
The circulating pump must not be blocked.
•
The expansion tank must be filled.
•
The gas flow and pressure must correspond to that given in the respective tables
•
The condensate evacuation system must be efficient with no leakage or obstruc-
tions
•
The trap must be full of water.
Con-
tents
Description
Range
t01
NTC Heating sensor (°C)
between 05 and 125°C
t02
NTC Safety sensor (°C)
between 05 and 125°C
t03
NTC Return sensor (°C)
between 05 and 125°C
t04
NTC DHW sensor (°C)
between 05 and 125°C
t05
NTC External sensor (°C)
between -30 and 70°C (negative values flash)
t06
NTC Fume sensor (°C)
between 05 and 125°C
F07
Actual fan frequency (Hz)
0-220 Hz
L08
Actual burner power (%)
00%=Min., 100%=Max.
F09
Actual DHW drawing (Lt_min/10)
00-99 Lt_min/10
P10
Actual system water pressure (bar/10)
00=With Pressure switch open, 14=Pressure switch closed,
00-99 bar/10 with Pressure transducer
P11
Actual modulating pump speed (%)
00-100%
P12
Actual modulating pump step (%)
24-59
F13
Actual ionization current (uA/10)
00-99 uA/10 (00=burner off)
A
A
B
A
OK
NO