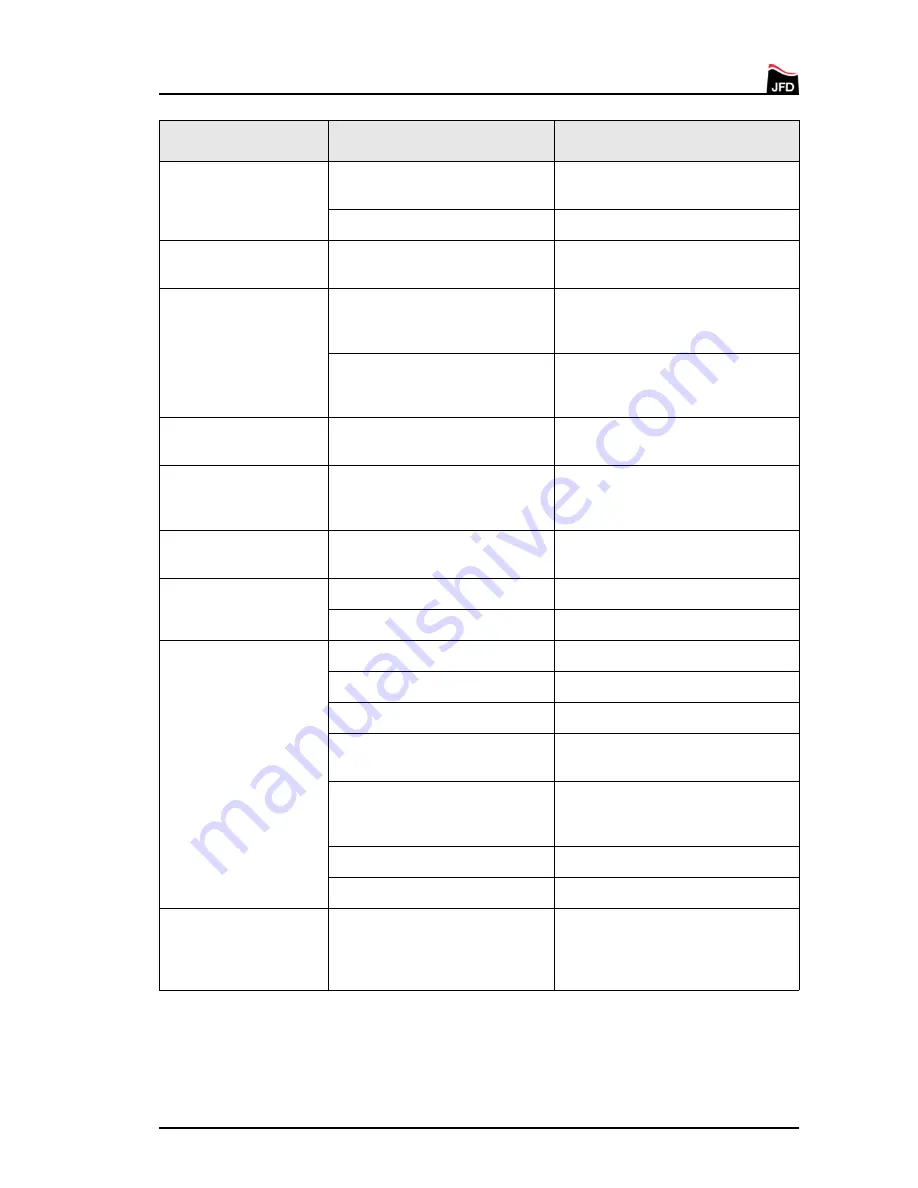
KI-OM-0591 Rev 3
23
Troubleshooting
Oil leaking in the
crankshaft area.
Worn crankshaft seal or improperly
installed oil seal retainer o-ring.
Remove oil seal retainer and replace
damaged o-ring and/or seals.
Worn bearing.
Replace bearing.
Excessive play on the
crank shaft pulley
Worn main bearing from excessive
tension on drive belt.
Replace bearing. Properly tension
belt.
Water in crankcase
May be caused by humid air
condensing into water inside the
crankcase.
Change oil at 3 month or 500 hour
intervals using JFD part no. DO03764.
Leakage of packing seals. Over-
pressure or faulty pressure
regulator.
Replace packing. Check pressure
regulator.
Oil leaking from underside
of crankcase.
Worn crankcase seals.
Replace seals.
Oil leaking at the rear
portion of the crankcase.
Damaged or improperly installed oil
gauge or crankcase rear cover o-
ring and drain plug o-ring.
Replace oil gauge or cover o-ring and
drain plug o-ring.
Oil leaking from drain
plug.
Loose drain plug or worn drain plug
o-ring.
Tighten drain plug or replace o-ring.
Loud knocking noise in
pump.
Pulley loose on crankshaft.
Check key and tighten set screw.
Broken or worn bearing.
Replacing bearings.
Frequent or premature
failure of the inlet manifold
seals.
Scored plungers.
Replace plungers.
Over pressure to inlet manifold.
Reduce inlet pressure (2.5 bar).
Damaged or worn plungers.
Replace the plungers.
Abrasive material in the fluid being
pumped.
Install proper filtration pump inlet
plumbing.
Excessive pressure and / or
temperature of fluid being pumped.
Check pressures and fluid inlet
temperature; be sure they are within
specified range.
Over pressure of pumps.
Reduce supply pressure.
Running pump dry.
Do not run pump without water.
Strong surging at inlet and
low pressure on
discharge side.
Foreign particles in the inlet or
discharge valve or worn inlet and /
or discharge valves.
Check for smooth lap surfaces on inlet
and discharge valve seals. Discharge
valve seals and inlet valve seals may
be lapped on a very fine oil stone.
Problem
Possible Cause
Solution
Содержание WHE - 3
Страница 2: ......
Страница 6: ...vi KI OM 0591 Rev 3 Intentionally blank ...
Страница 8: ...viii KI OM 0591 Rev 3 Intentionally blank ...
Страница 46: ...38 KI OM 0591 Rev 3 Part Identification Intentionally blank ...
Страница 56: ...B 2 KI OM 0591 Rev 3 Intentionally blank ...
Страница 60: ...C 4 KI OM 0591 Rev 3 WWHE 3 Electrical Schematic 24 VDC Control Circuit With Remote Sheet 1 of 2 ...
Страница 61: ...KI OM 0591 Rev 3 C 5 Sheet 2 of 2 ...
Страница 62: ...C 6 KI OM 0591 Rev 3 WHE 3 Electrical Schematic 440 V Heater Circuit With Remote ...
Страница 63: ...KI OM 0591 Rev 3 C 7 WHE 3 Electrical Schematic With Remote Busbar Manufacturing Detail ...
Страница 64: ...C 8 KI OM 0591 Rev 3 Schematic Water Heater Electric WHE 3 Upgrade With PV S 3 1 Cert Sheet 1 of 2 ...
Страница 65: ...KI OM 0591 Rev 3 C 9 Sheet 2 of 2 ...
Страница 66: ...C 10 KI OM 0591 Rev 3 Schematic Water Heater Electric WHE 3 Upgrade With PV S 3 2 Cert Sheet 1 of 2 ...
Страница 67: ...KI OM 0591 Rev 3 C 11 Sheet 2 of 2 ...
Страница 68: ...C 12 KI OM 0591 Rev 3 Intentionally blank ...