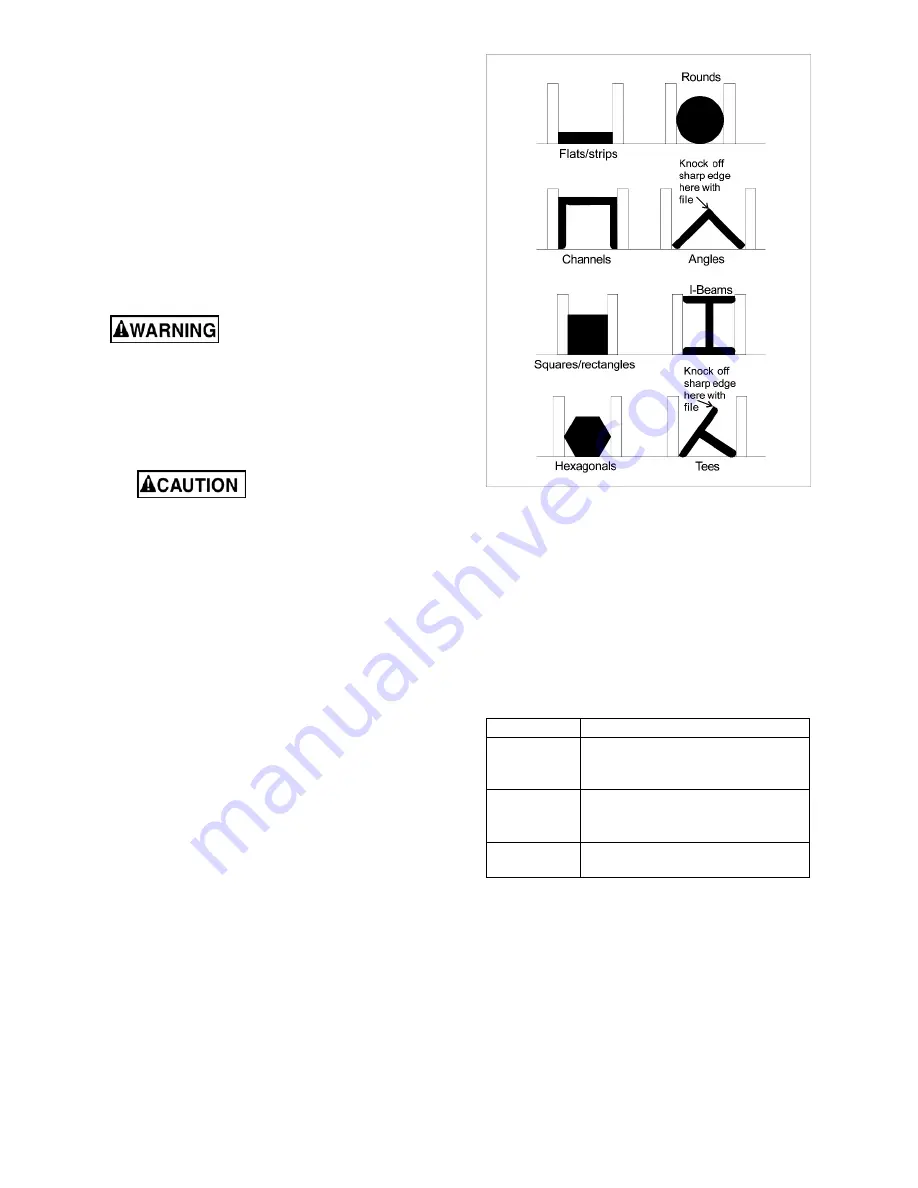
14
4. Select proper speed and feed rate for material
being cut.
5. Material to be cut must be securely held in vise.
6. Check to see that coolant level is adequate and
turn on coolant pump if material to be cut
requires it. Machine should be filled with
approximately 15 L (4 gal.) of proper coolant
mixture. Follow directions on product maker’s
label and fill coolant tank through chip tray area.
7. Do not start cut on a sharp edge.
8. Keep machine lubricated. See
sect. 10.2.
9.4
General operating procedure
All blade covers and guards
must be in place and secured before turning on
band saw.
1. Select proper speed for type of material to be
cut.
2. Close feed rate knob and lift bow high enough
to clear workpiece.
Make sure blade is not in
contact with workpiece when motor is
started. Do not drop bow onto workpiece or
force blade through workpiece.
3. Place stock between vise jaws, set stock for
desired width of cut and tighten vise. (See
Figure 9-3 for recommended placement in vise
of varied workpiece shapes.)
4. Make sure left blade guide bracket is adjusted
as close as possible to left vise jaw.
5. Start motor and allow machine to reach
operating speed.
6. Adjust coolant valves as desired.
7. Turn feed rate control knob for desired rate.
Allow blade to slowly enter workpiece.
8.
Saw will shut off at completion of cut.
9.5
Evaluating cutting efficiency
Is the blade cutting efficiently? The best way to
determine this is to observe the chips formed by the
cutting blade:
If chip formation is powdery, then feed rate is much
too light, or blade is dull.
If chips formed are curled, but colored — that is,
either blue or straw-colored from heat generated
during the cut — then feed rate is too high.
If chips are slightly curled and are not colored by
heat — blade is sufficiently sharp and is cutting at
its most efficient rate.
Figure 9-3
9.6
Blade selection
The saw is provided with a blade that is adequate
for a variety of cut-off jobs on a variety of common
materials.
See Table 3 for recommended speeds for various
materials. These selections, while appropriate for
many shop cutting needs, do not encompass the
wide variety of blades of special configuration (tooth
pitch and set) and special alloys for cutting unusual
or exotic materials.
Speed/FPM Material
100
Tool Steel, Stainless Steel,
Phosphor Bronze, Hard Bronze,
Hard Cast Iron, Malleable Iron
165
Mild Steel, Soft Cast Iron,
Med. Hard Brass,
Med.Hard Bronze
230
Soft Brasses and Bronzes,
Hard Aluminum, Plastics
Table 3
A coarse blade could be used for a solid steel bar
but a finer tooth blade would be used on a thin-wall
tube. In general, the blade choice is determined by
the thickness of the material; the thinner the
material, the finer the tooth pitch.
A minimum of three teeth should be on the work
piece at all times for proper cutting. The blade and
workpiece can be damaged if the teeth are so far
apart that they straddle the workpiece.
Содержание MBS-1018-1
Страница 18: ...18 12 1 1 MBS 1018 1 MBS 1018 3 Bow Assembly Exploded View...
Страница 22: ...22 12 2 1 MBS 1018 1 MBS 1018 3 Base Assembly Exploded View...
Страница 26: ...26 12 3 1 MBS 1018 1 MBS 1018 3 Electrical Box Assembly Exploded View...
Страница 29: ...29 13 2 Wiring Diagram for MBS 1018 3...
Страница 31: ...31 This page intentionally left blank...
Страница 32: ...32 427 New Sanford Road LaVergne Tennessee 37086 Phone 800 274 6848 www jettools com...