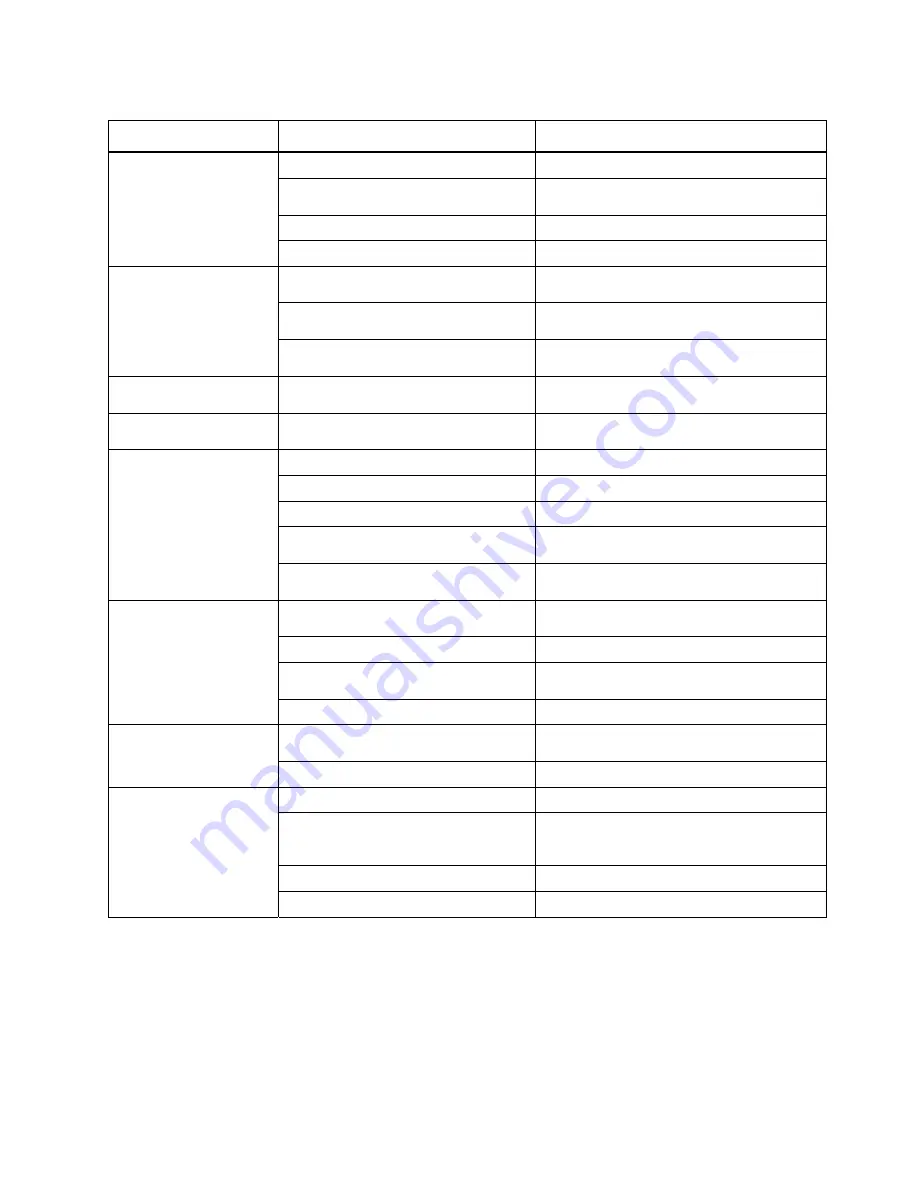
20
14.0
Troubleshooting JWSS-18B Scroll Saw
Table 3
Symptom
Possible Cause
Correction *
Motor will not start.
Low voltage.
Check power line for proper voltage.
Open circuit in motor or loose
connection.
Inspect all lead connections on motor for
loose or open connections.
Damaged cord or plug.
Inspect and replace.
Carbon brushes worn.
Replace brushes.
Motor will not start:
fuses blow or circuit
breaker trips.
Short circuit in line cord or plug.
Inspect cord or plug for damaged
insulation and shorted wires.
Short circuit in motor or loose
connections.
Inspect all connections on motor for loose
or shorted terminals or worn insulation.
Incorrect fuses or circuit breakers in
power line.
Install correct fuses or circuit breakers.
Machine slows when
operating.
Applying too much pressure to
workpiece.
Feed workpiece more slowly.
Tilting mechanism
difficult to move.
Caked dust or other obstruction in
trunnion assemblies.
Clean trunnion areas and apply light dabs
of grease to contacting parts.
Blades frequently
break.
Incorrect blade tension.
Set proper tension.
Blade being overworked.
Reduce feed rate.
Wrong blade type for job.
Select proper blade.
Blade twisting in workpiece.
Avoid side pressure on blade. Reduce
feed rate.
Too few teeth per inch.
Blade should have minimum 3 teeth in
contact with workpiece.
Blade refuses to
tension properly, or
keeps slipping.
Blade not seated properly.
Inspect entry of blade into upper and lower
blade chucks.
Blade tension lever needs tightening.
Tighten tension lever.
Set screws in upper blade chuck are
backed out, not contacting blade.
Tighten set screws.
Blade clamp has oil or debris on it.
Clean blade clamp, ends of set screws.
Blade drift.
Some drift is unavoidable depending
upon size of blade and type of cut.
Compensate by manipulation of workpiece
into blade.
Incorrect blade tension.
Increase tension.
Excessive vibration.
Saw improperly mounted.
Secure saw properly to bench or stand.
Unsuitable mounting surface.
Less vibration will occur with a heavier
work bench. Use pads or fiber washers at
mounting contact points.
Arms/linkage system not tight.
Tighten trunnion lock knob.
Loose motor mounting.
Tighten motor mount screws.
*
WARNING:
Some corrections may require a qualified electrician or service personnel.