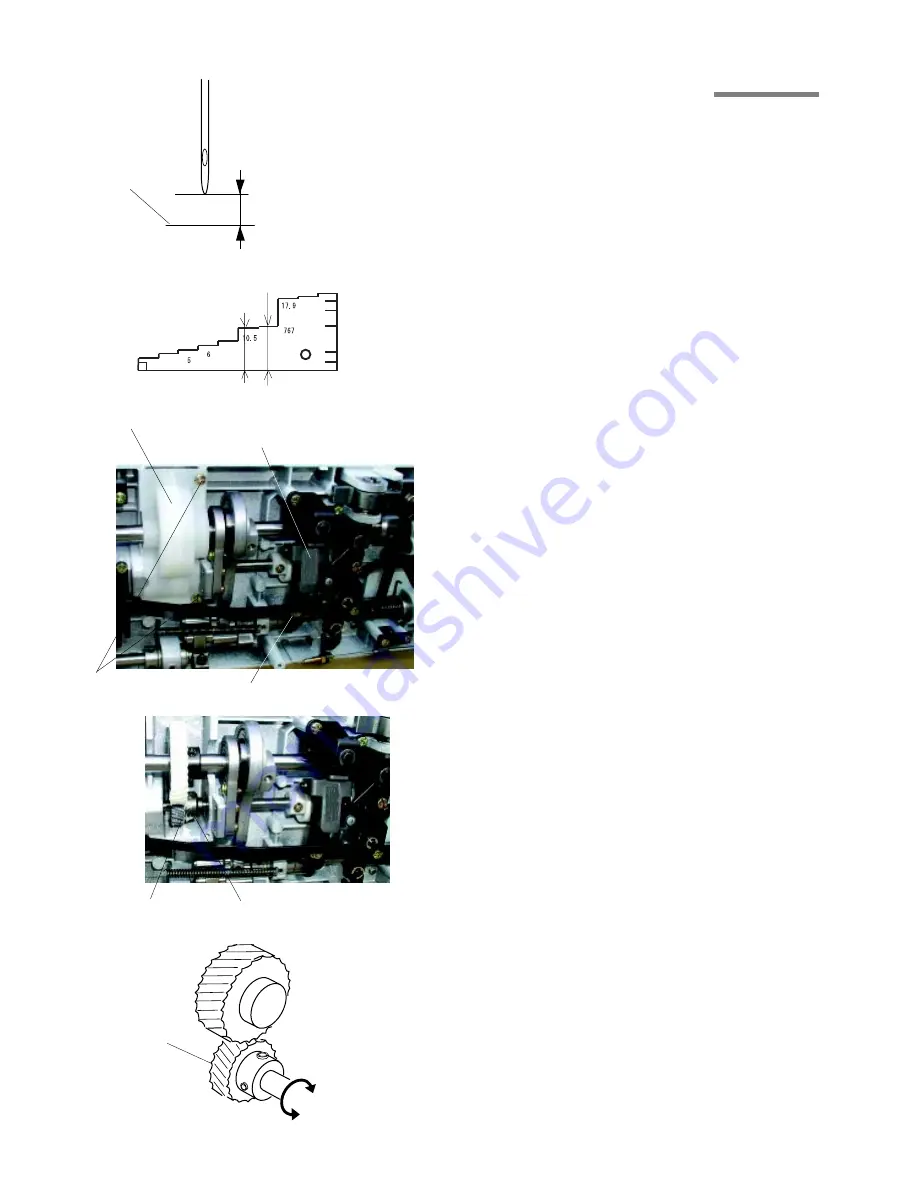
24
4. Needle to Cutter Cam Timing
[1] Remove the base.
[2] Remove the setscrews (1) and gear cover (2).
[3] Lower the needle bar to the lowest position.
Turn the hand wheel toward you until tip of the needle
levels with the presser foot. Continue to turn the
hand wheel toward you to raise the needle bar while
pushing up the link body (3).
[4] Continue to turn the handwheel until the thread
drawing arm (4) starts to move to the right.
The needle point should be 10.5 mm (1600P-DB/
DBX) or 10.9 mm (1600P) above the upper surface of
the needle plate (5) when the thread drawing arm
starts to move.
(Use the 6th and 7th steps of the Gauge 767G-001 for
10.5 mm and 10.9mm).
[5] Loosen the 2 setscrews (6) and turn the hook shaft
gear (7) to adjust the timing.
- If the needle point is too high, turn the hook shaft
gear in the direction
A
.
- If the needle point is too low, turn the hook shaft
gear in the direction
B
.
NOTES:
Hold the hook so that it will not rotate when turning the
hook shaft gear.
Check the needle to hook timing and adjust it if neces-
sary.
[6] Tighten the 2 setscrews (6) firmly. Attach the gear
cover (2) and secure it with the setscrews (1).
Attach the base.
(1)
(2)
(3)
(5)
(4)
(6)
(7)
(7)
B
A
10.5 mm (1600P-DB/DBX)
10.9 mm (1600P)
10.5 mm
10.9 mm
Содержание 1600P PROFESSIONAL -
Страница 1: ...Servicing Manual 1600P 1600 DB 1600 DBX ...