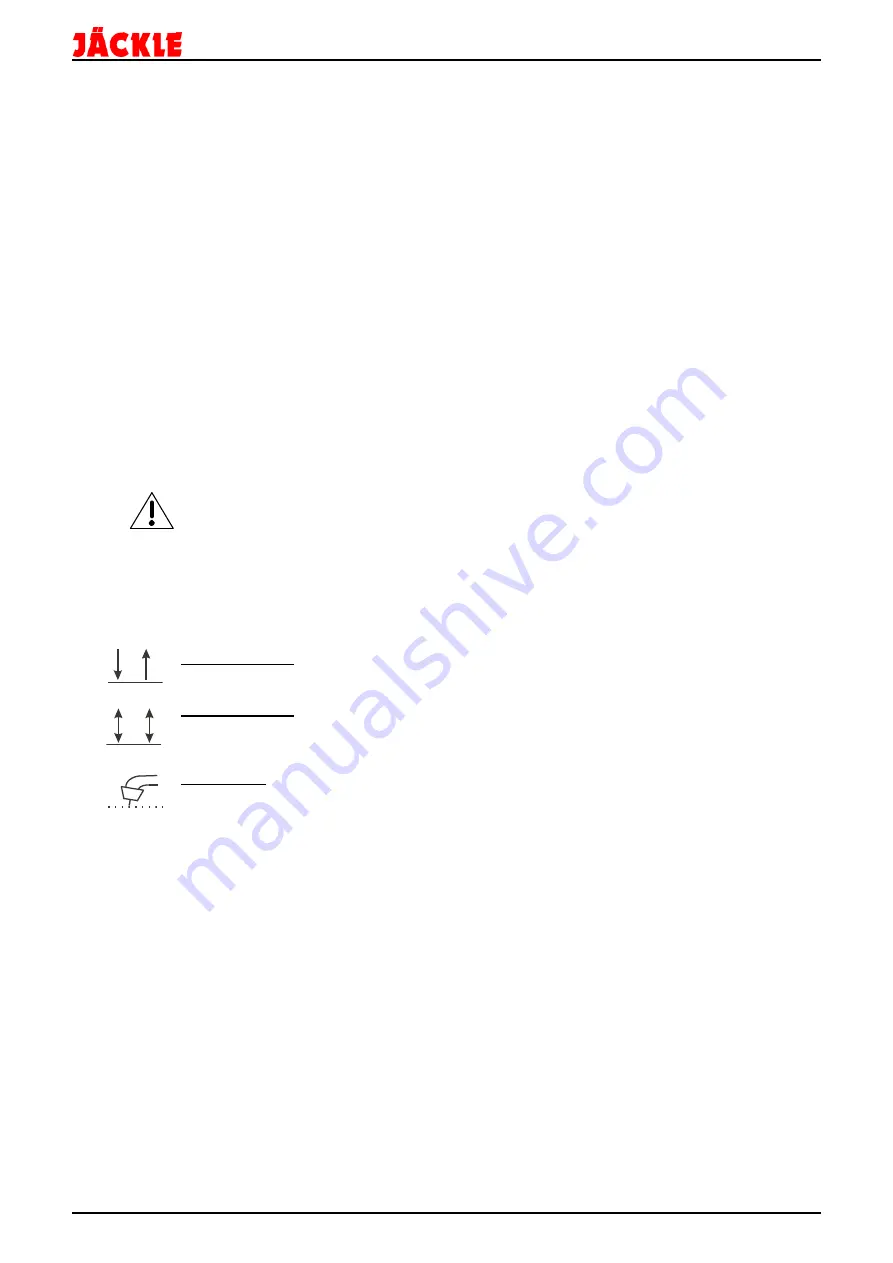
maxiMIG 250/300
Operating manual
Page 21
1
Temperature fault indicator
is lit in the event of thermic overload. No possibility of starting the welding process by means of the torch
trigger. With the fan running, the unit will be operable again after approx. 5 minutes.
2
Master switch
Position „0“:
unit is switched off.
Position „I“:
unit is switched on, control lamp is lit.
3
Weld-grade-switch, 12 steps
4
Central connecting socket
5
‘Wire feed rate’ potentiometer control knob
For infinitely variable regulation of desired wire feed speed, ranging from 1,0 to 24m/min
6
‘Spot welding time’ potentiometer control knob
For infinitely variable regulation of the spot welding time ranging from 0.5 to 10 sec.
maxiMIG 250:
For normal welding operation the Control knob
must be set to position ‘0’ (left-hand stop).
7
Selector switch for 2-cycle/ 4-cycle operation / spot welding (only maxiMIG 300)
for selecting the desired torch trigger program, ie. either 2-cycle or 4-cycle operation or spot welding
function.
2-cycle operation for short weld seams and tack-welds
The welding process continues as long as the torch trigger is kept pressed down.
4-cycle operation for long weld seams
The welding process is initiated upon the first press of the torch-trigger and terminated by
pressing again.
Spot welding
In spot welding two overlapping thin sheets are pressed together and joined by spot-type
welding, using a special gas nozzle. To obtain flat weld points, a high welding voltage will be
required in dependence on the sheet thickness.
The welding process is started by pressing the torch trigger and terminates as set on the
“spot welding time“ potentiometer (7).
The next welding process is started by pressing the torch trigger again.
Premature release of the torch trigger will cause immediate stop of the welding process.
8
workpiece socket
X
‘Wire burnback time’ knob – only maxiMIG 300 (see next page, under wire feed motor)
For infinitely variable regulation of wire burn-back time at the end of the welding operation.
Anticlockwise:
reduces wire burn-back time, i.e. wire does not burn back as far. If burn-back time is too
short, the wire end adheres to the solidified weld pool.
Clockwise:
increases wire burn-back time, i.e. wire burns back towards the current contact tip.
Wire must not burn back into the current contact tip, otherwise, it will burn into the tip.
Содержание maxiMIG 250
Страница 1: ...maxiMIG 250 300 Version 08 2012 Deutsch Seite 1 12 27 32 English Page 13 32...
Страница 2: ......
Страница 16: ...maxiMIG 250 300 Operating manual Page 13 Operating manual maxiMIG 250 300...
Страница 30: ...maxiMIG 250 300 Operating manual Page 27 20 Ersatzteile spare parts Frontansicht frontview maxiMIG 250 300...
Страница 32: ...maxiMIG 250 300 Operating manual Page 29 Seitenansichten sideview maxiMIG 250 300...