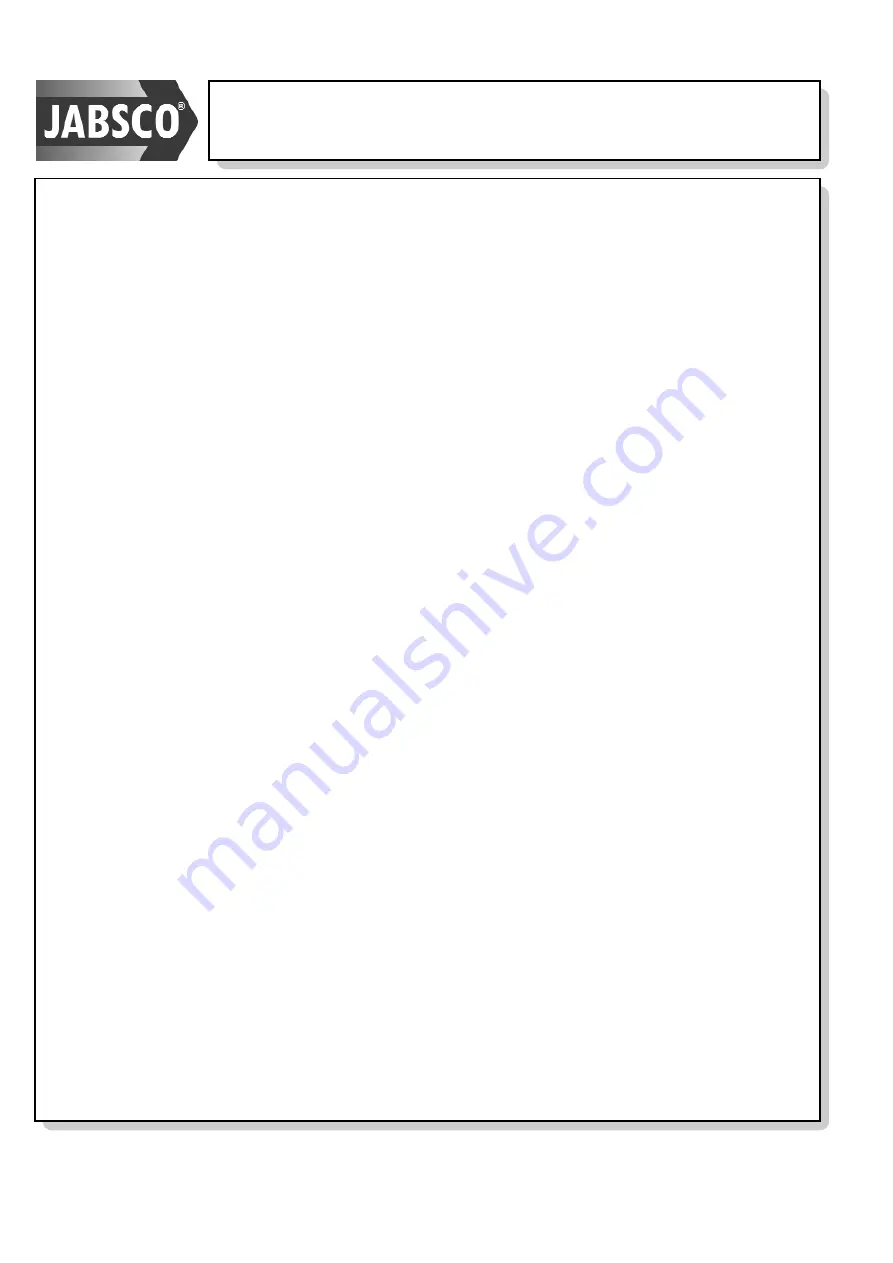
l) If the valve was previously set and the
adjusting screw to housing dimension had
been noted (see note at start of
Disassembly), re-set the adjusting screw to
this dimension, this does not apply if a new
spring has been fitted. Otherwise set the
valve as in Section 2.12.
6.13 THERMAL JACKET - END COVER
Ensure that the liquid feed to the jacket is
switched off before attempting to service it.
a) Dismantle the jacket (144) from the cover
(143) by removing the screw(s) (147) from
the centre of the jacket
b) Remove the inner O-ring(s) (146) from
the groove(s) around the screws and the
outer O-ring(s) (145) from the groove
around the outside edge of the jacket.
c) Replace the O-rings and re-fit the jacket.
d) Tighten the screws to the correct torque.
6.14 THERMAL JACKET - PUMP HEAD
Ensure that the liquid feed to the jackets is
switched off before attempting to service
them.
a) Dismantle the two jackets (139) from the
end cover (138) by removing the screws
(141).
b) Remove the O-rings (140) from their
grooves.
c) Replace the O-rings and re-fit the jackets.
d) Tighten the screws to the correct torque.
6.15 THERMAL JACKET - ROTOR CASE
Ensure that the liquid feed to the jackets is
switched off before attempting to service it.
a) Dismantle the jackets from the rotor case
(51) by removing the nuts (153) from the
port retaining studs (152).
b) Remove the joint rings (53 & 149) from
the grooves in the ports and the jackets.
c) Remove the screws from the jackets
where fitted, and separate the 2 halves of
the jackets
d) Peel off the gaskets and clean the two
mating faces of the jackets.
e) Fit new gaskets (148) and re-assemble
the 2 halves. Tighten the screws to the
correct torque.
f) Fit new port joints (53 & 149) and
re-assemble the jackets to the rotor case.
g) Tighten the nuts to the correct torque.
6.16 BEARING HOUSING
Power input to the pump is via the drive
shaft (24). The gearbox has two
contra-rotating shafts (24 & 25), supported
by taper roller bearings (4 & 5). The shafts
are synchronized by a pair precision cut
gears (6) that distribute power between the
drive shaft (24) and driven (lay) shafts (25).
Hy~Line
and
Ultima
pump gearboxes have
been designed for easy inspection and
maintenance. Care must be taken, as
correct gearbox assembly is essential for
effective pump operation and long-life. If in
doubt consult your supplier or the
manufacturer. (See figure 20).
Page 34
Hy~Line
and
Ultima
Lobe Pumps
07/03
Содержание Hy-Line
Страница 41: ...07 03 Page 39 Hy Line and Ultima Lobe Pumps 7 00 MODEL NUMBER BUILD CODE...
Страница 43: ...07 03 Page 41 Hy Line and Ultima Lobe Pumps 8 01 PARTS LIST...
Страница 44: ...Page 42 Hy Line and Ultima Lobe Pumps 07 03 8 01 PARTS LIST CONTENTS OF KITS...
Страница 45: ...Page 43 Hy Line and Ultima Lobe Pumps 07 03 8 02 Hy Line EXPLODED DIAGRAM...
Страница 46: ...07 03 Page 44 Hy Line and Ultima Lobe Pumps 8 03 Ultima EXPLODED DIAGRAM...
Страница 47: ...07 03 Page 45 Hy Line and Ultima Lobe Pumps 8 04 Hy Line 3 Size SECTIONAL VIEW...
Страница 51: ...07 03 Page 49 Hy Line and Ultima Lobe Pumps...