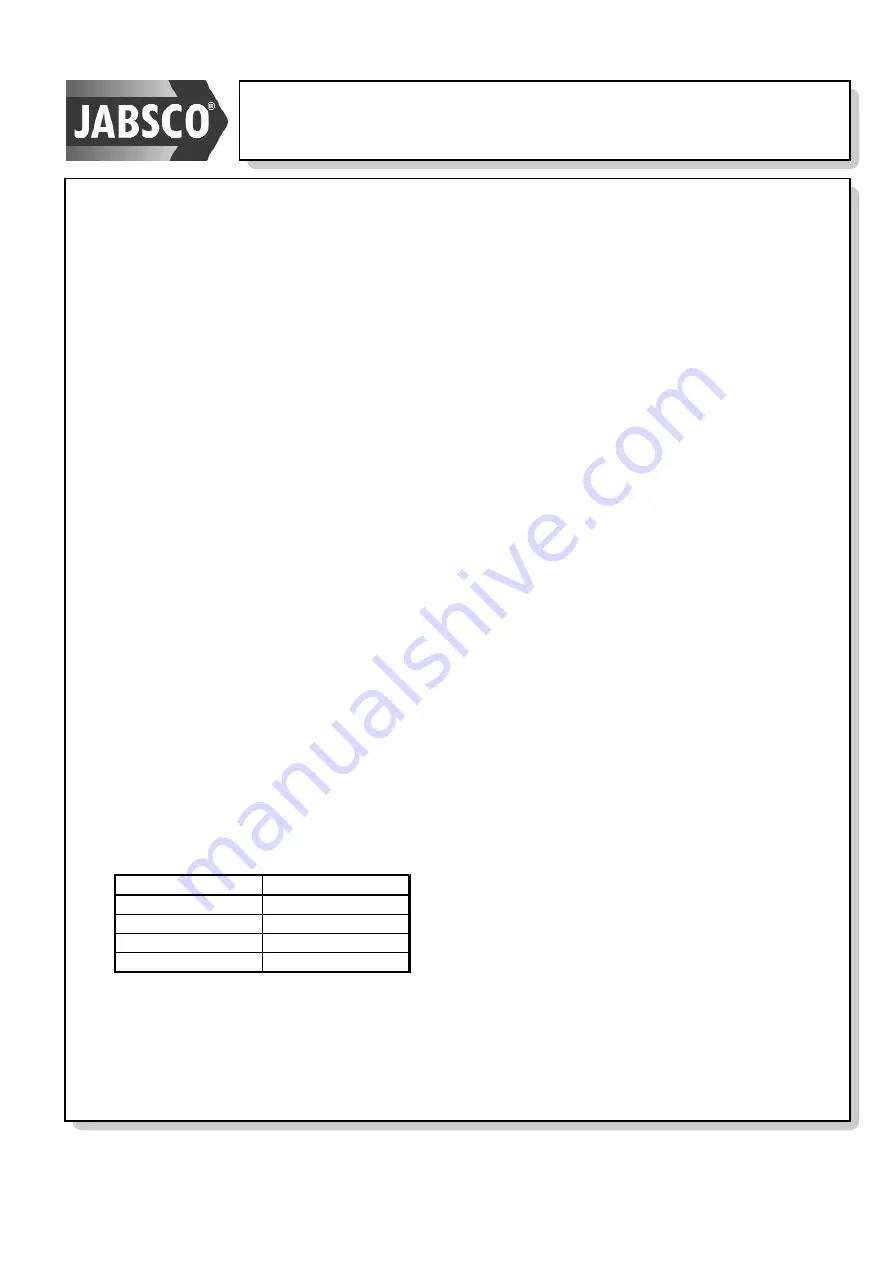
2.11 MECHANICAL SEAL MATERIALS
SEAL FACES
All primary seals are available with carbon-
on-silicone carbide faces (Codes 3, 4 or 5)
for non abrasive fluids and silicon carbide-
on-silicon carbide faces (Codes 1, 2 or 7) for
abrasive fluids containing crystals, powders
or particles or when no particles of wear can
be allowed to enter the pumped fluid.
Silicon carbide-on-silicon carbide (Code 1, 2
or 7) seals are not recommended for steam
flushed applications.
Hy~Line
only:
Carbon on stainless steel
single seals (Code 8) are available for non-
abrasive and lubricating fluids.
All secondary double mechanical seals
(Codes 1 or 4) are with carbon on silicon
carbide faces.
ELASTOMERS
Product contacting primary elastomers must
be selected to be compatible with the
product and the process operation.
Consideration must be given to chemical
compatibility, temperatures and material
standards.
Hy~Line
and
Ultima
are
available in a selection elastomers, see
below.
Consult supplier for more information.
2.12 END COVER RELIEF VALVE
Hy~Line
pumps can be fitted with an end
cover relief valve which can be set to protect
the PUMP ONLY from overpressure. This
valve is not designed to protect the system
or to provide long term by-pass of liquid. If
this is required then an IN-LINE relief valve
should be fitted which can by-pass the liquid
back to the suction vessel during
overpressure situations.
The maximum pressure rating of the pump
is stated on the Performance Data Sheet.
The relief valve should be set so that is fully
open before it reaches this pressure. Be
aware that there may be a piece of
equipment in the system that is limited to a
lower pressure than the pump. If this is the
case then the pump end cover relief valve
should be set so that the pump cannot
exceed this pressure.
Setting the relief valve :
This should be done, if possible, using the
liquid to be pumped.
1. Screw the adjusting screw (135)
clockwise so that enters the housing as
far as possible. This ensures that the
valve is fully closed.
2. A pressure gauge is required to be fitted
in the pipe sysytem directly after the
pump.
3. Start the pump running.
4. Increase the pressure on the pump by
closing a valve downstream or by
increasing the pump speed. Continue
until the desired relief valve pressure
setting is achieved.
5. MAKE SURE THAT THE MAXIMUM
PRESSURE OF THE PUMP IS NOT
EXCEEDED. CHECK THE
PERFORMANCE DATA SHEET.
Page 13
Hy~Line
and
Ultima
Lobe Pumps
07/03
Hy~Line
Ultima
Nitrile- food grade
EPDM- FDA grade
EPDM- FDA grade
Viton- FDA grade
Viton- FDA grade
PTFE
PTFE
Содержание Hy-Line
Страница 41: ...07 03 Page 39 Hy Line and Ultima Lobe Pumps 7 00 MODEL NUMBER BUILD CODE...
Страница 43: ...07 03 Page 41 Hy Line and Ultima Lobe Pumps 8 01 PARTS LIST...
Страница 44: ...Page 42 Hy Line and Ultima Lobe Pumps 07 03 8 01 PARTS LIST CONTENTS OF KITS...
Страница 45: ...Page 43 Hy Line and Ultima Lobe Pumps 07 03 8 02 Hy Line EXPLODED DIAGRAM...
Страница 46: ...07 03 Page 44 Hy Line and Ultima Lobe Pumps 8 03 Ultima EXPLODED DIAGRAM...
Страница 47: ...07 03 Page 45 Hy Line and Ultima Lobe Pumps 8 04 Hy Line 3 Size SECTIONAL VIEW...
Страница 51: ...07 03 Page 49 Hy Line and Ultima Lobe Pumps...