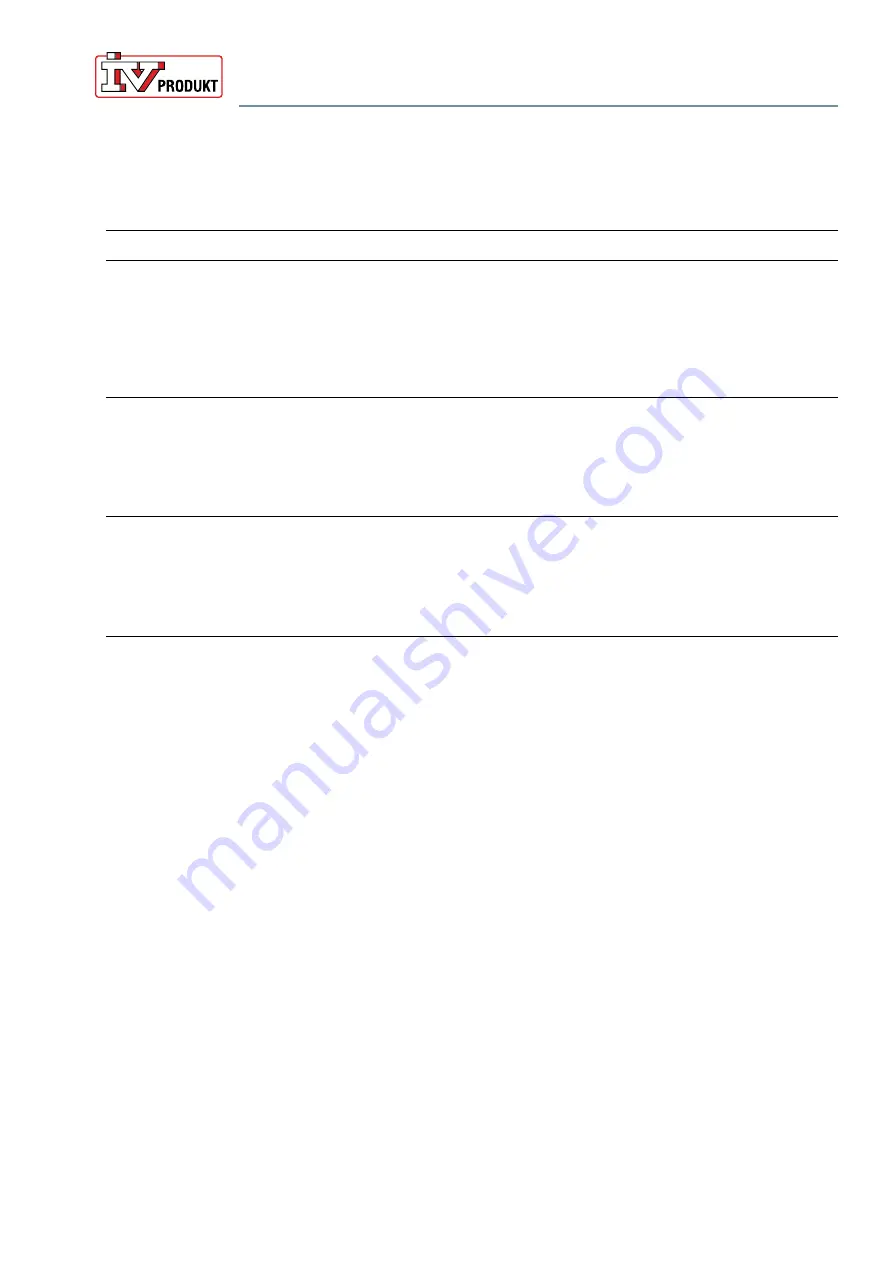
Page 17
Operation and Maintenance
NEW EcoCooler
DSKE.191101.01.EN
Continuous product development may give rise to specification changes without notice.
6.2 Troubleshooting via symptoms
Symptom
Possible cause
Corrective action
Low cooling power - too
high temperature in the
cooled object
The power supply has been interrupted.
Check the control/safety switches and
fuses.
No air flow or too low air flow across eva-
porator.
Check that nothing is inhibiting the air
flow.
The control equipment is incorrectly pre-
set/defective
Adjust the settings or replace the
equipment.
Compressor is not ope-
rating
The power supply has been interrupted.
Check the control/safety switches and
fuses.
The compressor has tripped the high
pressure switch.
Check and reset, if needed.
Defective compressor
Check/replace
Frost on the evaporator
The expansion valve is incorrectly preset/
defective
Check/replace
Insufficient refrigerant volume
Search to detect leakage, seal the leak
and charge with refrigerant
Low supply air flow
Adjust the flow
Alarm reset
In the event of an alarm initiated by the frequency inverter or the high pressure
switch, the compressor stops and the sum alarm relay is energised. The alarm
is displayed in the control unit menus “Operating information, compressors” and
“Status: Alarm”.
In the event of an alarm, take corrective action to correct the fault, and then
press the “Alarm reset” button on the control unit for 3 seconds. If the high pres-
sure alarm trips repeatedly, an authorised refrigeration service company must be
called in.