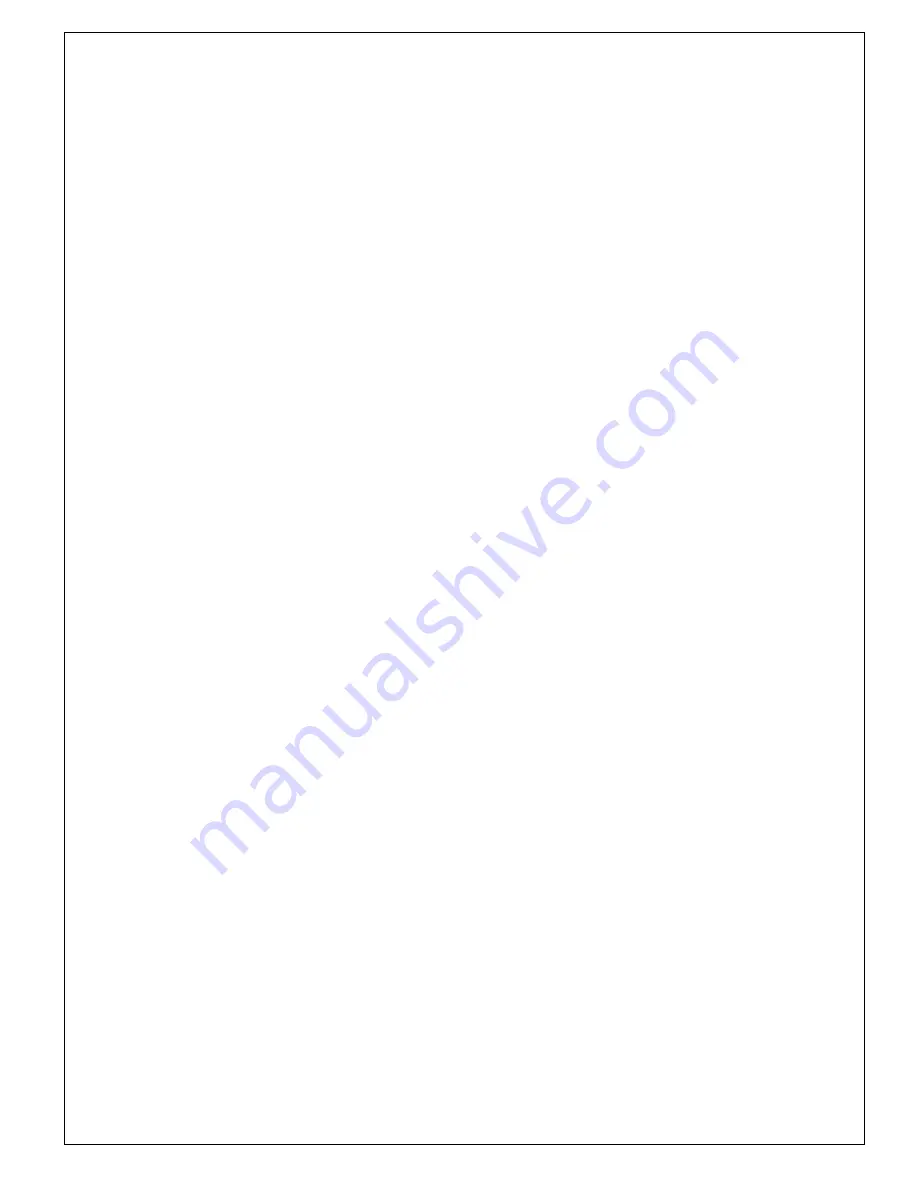
ITT
Engineered Valves, LLC
Page 19 of 22
Technical Manual No. IOT1000P Effective 8/31/2018
REV LEVEL B
3.
Pressurize the atomizing inlet to 50 PSIG (344.7 KPa) air while
monitoring the fuel outlet port for leakage. The allowable leakage rate per
ANSI Class IV is 439 cc/min.
4.
If leakage is excessive, stroke the valve 10 to 20 times to allow the metal
seat to wear in with the metal plug and retest the valve. If valve leakage is
still excessive, the main stem and purge seat should be replaced and the
valve retested.
C.
Oil Seat
1.
The valve should be in fully closed position.
2.
The atomizing inlet and outlet should be plugged.
3.
Pressurize the fuel inlet port to 50 PSIG (344.7 KPa) air while measuring
the leakage rate from the fuel outlet. The allowable leakage rate is one
bubble per minute or Class VI.
4.
If leakage is excessive, stroke the valve 10 to 20 times to allow the soft
seal in the oil seat to wear in with the metal plug and retest the valve. If
valve leakage is still excessive the oil seat and/or stem should be replaced
and the valve retested.
VI.
PROOF OF CLOSURE (POC) SWITCH TESTING
The POC switches should be tested after the valve has been leak tested.
The intent of the Proof of Closure (POC) switch is to prove the valve is in the closed
position. To accomplish this, the oil valve is designed with valve seal over-travel. That is,
the seal will stop the flow of oil and continue to move in the valve seat bore until the
metal seat is made. During this portion of valve stroke the oil valve is effectively sealed,
the POC switch contacts must change state. That is, the POC Switch changes state before
oil flows regardless of whether the valve moves from the Closed position to Fire or Fire
to Closed (Purge).
A.
Limit Switches
1.
Ensure the valve is in the closed position.
2.
Wire the switch to a test device.
3.
Loosen switch and push it towards the end flange (up - orientation