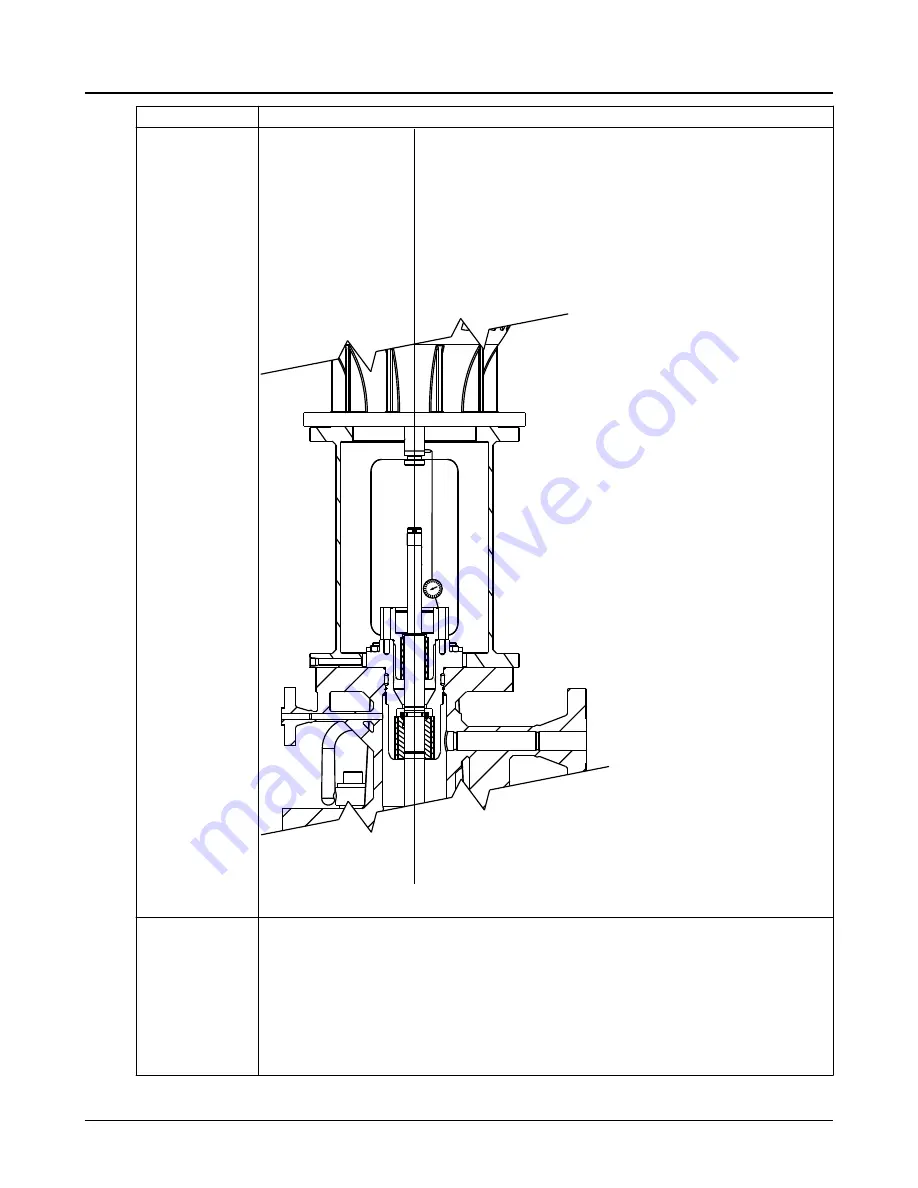
Procedure
Figure 12: Seal Chamber Flatness and Angularity Setup
Runout of the seal
housing bore
This measurement requires that you remove the mechanical seal.
1.
Install the dial indicator as shown.
2.
Rotate the driver shaft by hand and run the indicator in the inside-machined surface of
the seal housing in order to determine the concentricity.
3.
If the indicator reads higher than 0.10 mm | 0.004 in. TIR, loosen the driver hold-down
bolts and relocate the driver on the motor base register.
4.
Obtain the desired position.
5.
Tighten the hold-down bolts and repeat the indicator reading.
4.3 Installing a disassembled pump
Model VICR Installation, Operation, and Maintenance Manual
33