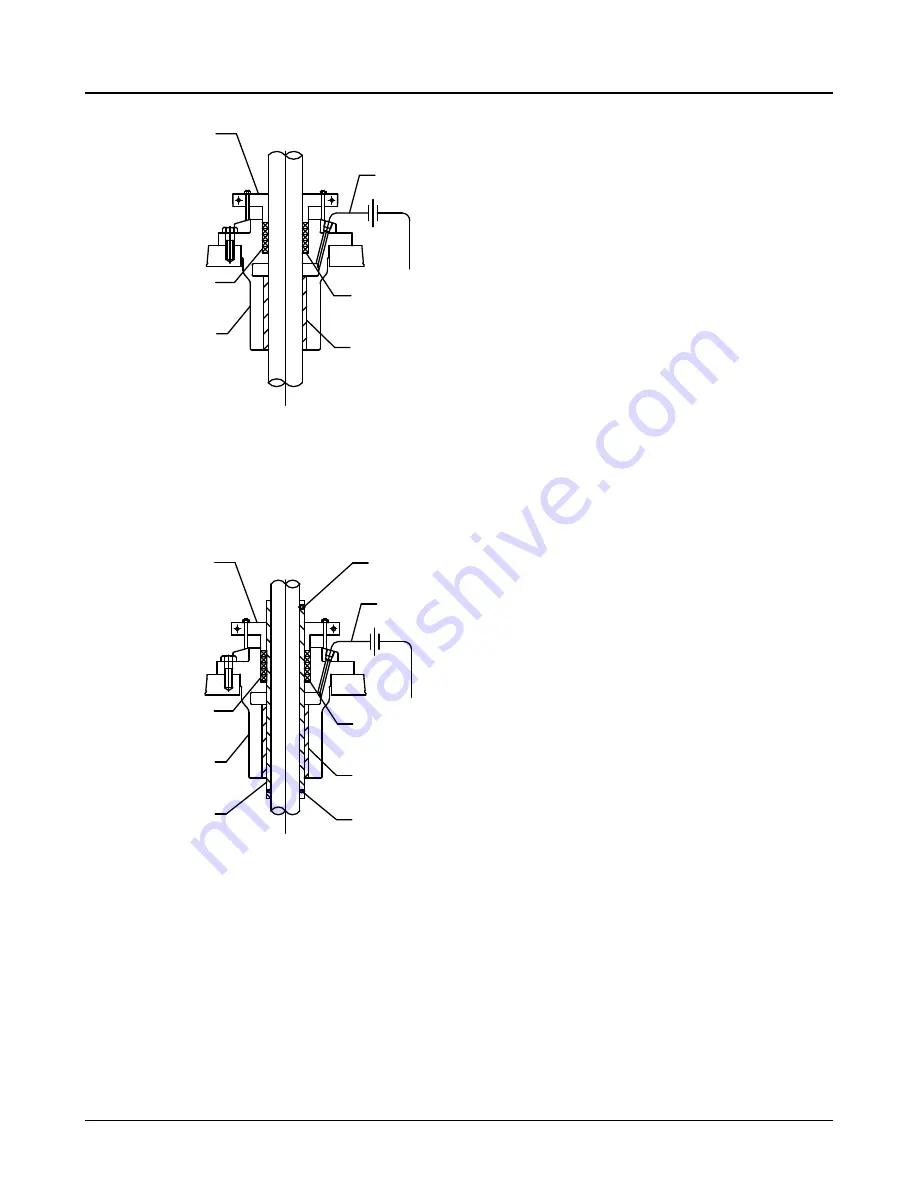
1
2
3
4
5
6
1.
Bypass line
4.
Packing box
2.
Packing washer
5.
Packing rings
3.
Bearing
6.
Split gland
Figure 7: Type A stuffing box
1
2
3
4
5
6
7
8
9
(618) SPLIT
SET SCREW (774)
1,
Setscrew
6.
Sleeve
2.
Bypass line
7.
Packing box
3.
Packing washer
8.
Packing rings
4.
Bearing
9.
Split gland
5.
O-ring
Figure 8: Type B stuffing box
4.7.1 Installing the type A and B stuffing boxes
The type B stuffing box is the same as the type A with the exception that it has a shaft sleeve with an O-
ring.
4.7 Stuffing box installation
28
Model VCW Installation, Operation, and Maintenance
Содержание Goulds Pumps VCW
Страница 1: ...Installation Operation and Maintenance Model VCW ...
Страница 2: ......