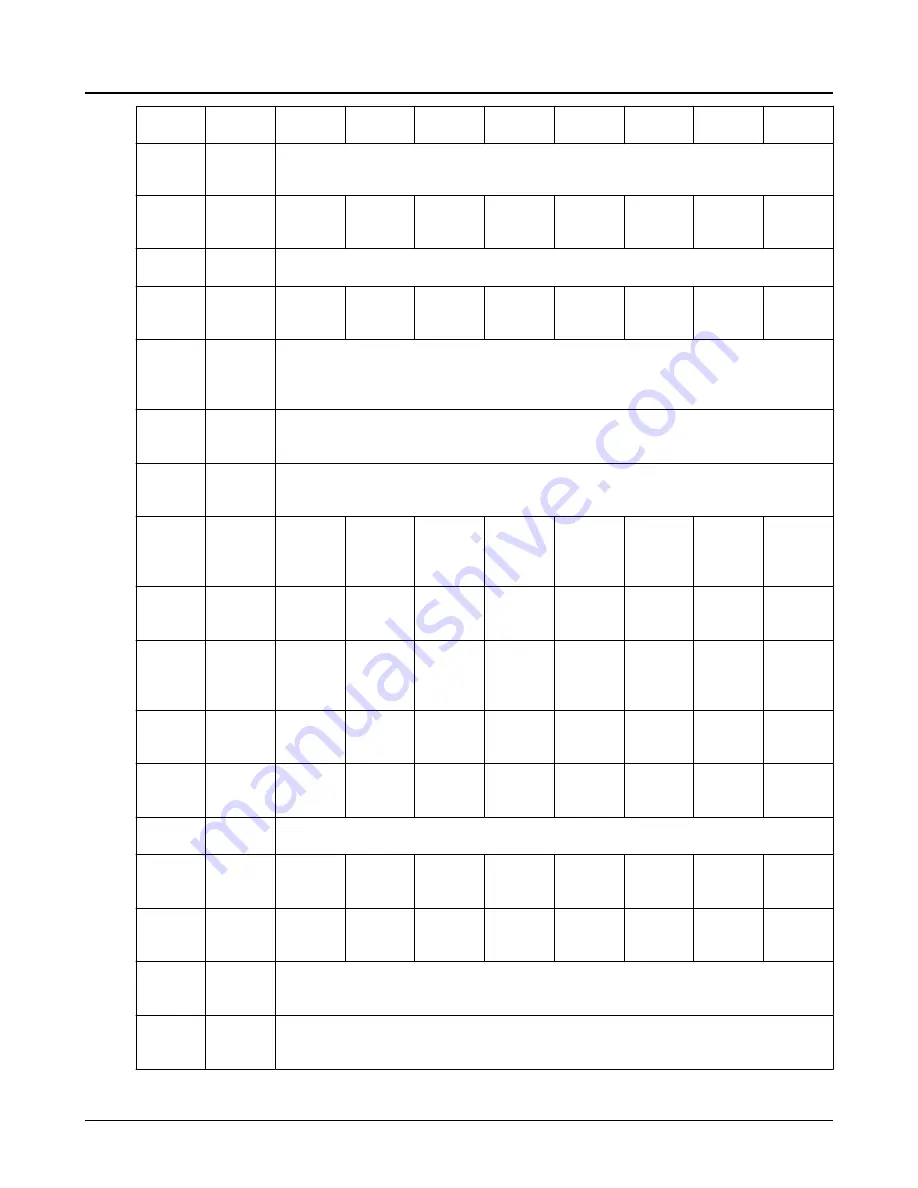
Item
Part
Name
S-6
S-8
C-6
A-8
D-1
D-2
S-8N
A-8N
Cover,
Coupling
End
164,
164A,
164B
Wear
Ring, Cas-
ing
2222
6983
2222
6983
6187
6171
1265
1265
168
Radial
Bearing
-
178,
178A,
178B
Impeller/
Sleeve
Key
2226
2226
2244
2226
2435
3280
2226
2226
178Y
Aux.
Pump
Coupling
Key
2213
195G
Flange
Cover –
Suction
3201
195H
Flange
Cover –
Discharge
3201
202,
202A,
202B
Wear
Ring, Im-
peller –
Suction
2255
6983
2255
6983
6186
6170
1071
1071
203
Wear ring,
Impeller –
Hub
2255
6983
2255
6983
6186
6170
1071
1071
203A
Wear
Ring, Im-
peller –
Center
2255
6983
2255
6983
6186
6170
1071
1071
204
Sleeve,
Dia-
phragm
2445
6983
2445
6983
6186
6170
2445
2445
205
Sleeve,
Center
Bushing
2445
6983
2445
6983
6186
6170
2445
2445
219
Auxiliary
Oil Pump
-
220
Seal
Chamber,
Radial
2210
2210
2244
2229
2435
3280
2210
2229
221
Seal
Chamber,
Thrust
3201 OR
1212
3201 OR
1212
3220 OR
1234
2229 OR
1296
2435 OR
1362
3280 OR
1361
3201 OR
1212
2229 OR
1296
222B
Set Screw,
Thrust
Collar Nut
2229
222S
Set Screw,
Coupling
Nut
2229
8.1 Parts list
130 Model 3600 i-FRAME API610 11th Edition / ISO 13709 2nd Edition to current API BB3 Multi-Stage, Axially Split Installa-
tion, Operation, and Maintenance Manual
Содержание GOULDS PUMPS 3600 i-FRAME
Страница 2: ......