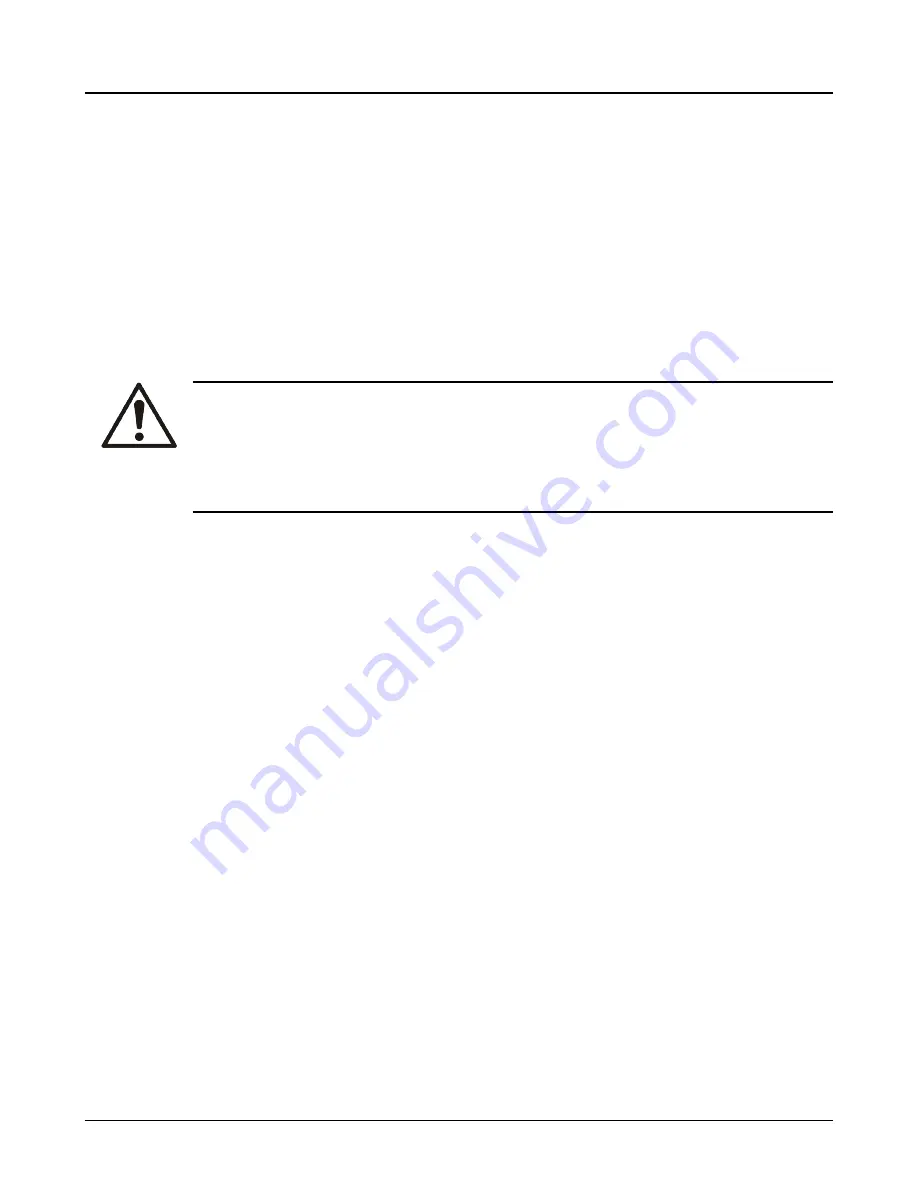
1.3 Safety regulations for Ex-approved products in potentially
explosive atmospheres
Description of ATEX
The ATEX directives are a specification enforced in Europe for electrical and non-electrical equipment.
ATEX deals with the control of potentially explosive atmospheres and the standards of equipment and
protective systems used within these atmospheres. The relevance of the ATEX requirements is not limit-
ed to Europe. You can apply these guidelines to equipment installed in any potentially explosive atmos-
phere.
Guidelines for compliance
WARNING:
This manual clearly identifies accepted methods for disassembling units. These methods must
be adhered to. Trapped liquid can rapidly expand and result in a violent explosion and injury.
Never apply heat to impellers, propellers, or their retaining devices to aid in their removal. If
there are any questions regarding these requirements, the intended use, or if the equipment
requires modification, contact an ITT representative before you proceed.
Compliance is only fulfilled when the pump is operated within its intended use, for example within its in-
tended hydraulic range. The conditions of the service must not be changed without approval of an au-
thorized ITT representative. When installing or maintaining explosion-proof pumps, follow these guide-
lines:
•
Always install ATEX-approved equipment in compliance with the directive and applicable standards
(IEC/EN 60079–14).
•
Do not install explosion proof products in locations that are classified as hazardous in the national
electric code, ANSI/NFPA 70–2005.
Personnel requirements
ITT disclaims all responsibility for work done by untrained and unauthorized personnel.
These are the personnel requirements for Ex-approved products in potentially explosive atmospheres:
•
All work on the product must be carried out by certified electricians and ITT-authorized mechanics.
Special rules apply to installations in explosive atmospheres.
•
All users must know about the risks of electric current and the chemical and physical characteristics
of the gas and/or vapor present in hazardous areas.
•
Any maintenance for Ex-approved products must conform to international and national standards
(for example IEC/EN 60079-17).
Product and product handling requirements
These are the product and product handling requirements for Ex-approved products in potentially explo-
sive atmospheres:
•
Only use the product in accordance with the approved motor data stated on the nameplates.
•
The Ex-approved product must never run dry during normal operation. Dry running during service
and inspection is only permitted outside the classified area.
•
Never start a pump without the proper priming.
•
Before you start working with the product, make sure that the product and the control panel are iso-
lated from the power supply and the control circuit, so they cannot be energized.
1.3 Safety regulations for Ex-approved products in potentially explosive atmospheres
8
Model 3393 Installation, Operation, and Maintenance Manual
Содержание GOULDS PUMPS 3393
Страница 1: ...Installation Operation and Maintenance Manual Model 3393 ...
Страница 2: ......
Страница 67: ...6 5 Disassembly Model 3393 Installation Operation and Maintenance Manual 65 ...
Страница 69: ...6 5 Disassembly Model 3393 Installation Operation and Maintenance Manual 67 ...
Страница 73: ...6 5 Disassembly Model 3393 Installation Operation and Maintenance Manual 71 ...
Страница 76: ...6 5 Disassembly 74 Model 3393 Installation Operation and Maintenance Manual ...
Страница 77: ...6 5 Disassembly Model 3393 Installation Operation and Maintenance Manual 75 ...
Страница 78: ...6 5 Disassembly 76 Model 3393 Installation Operation and Maintenance Manual ...
Страница 81: ...6 5 Disassembly Model 3393 Installation Operation and Maintenance Manual 79 ...
Страница 82: ...6 5 Disassembly 80 Model 3393 Installation Operation and Maintenance Manual ...
Страница 92: ...6 7 Reassembly 90 Model 3393 Installation Operation and Maintenance Manual ...
Страница 97: ...6 7 Reassembly Model 3393 Installation Operation and Maintenance Manual 95 ...
Страница 100: ...6 7 Reassembly 98 Model 3393 Installation Operation and Maintenance Manual ...
Страница 101: ...6 7 Reassembly Model 3393 Installation Operation and Maintenance Manual 99 ...