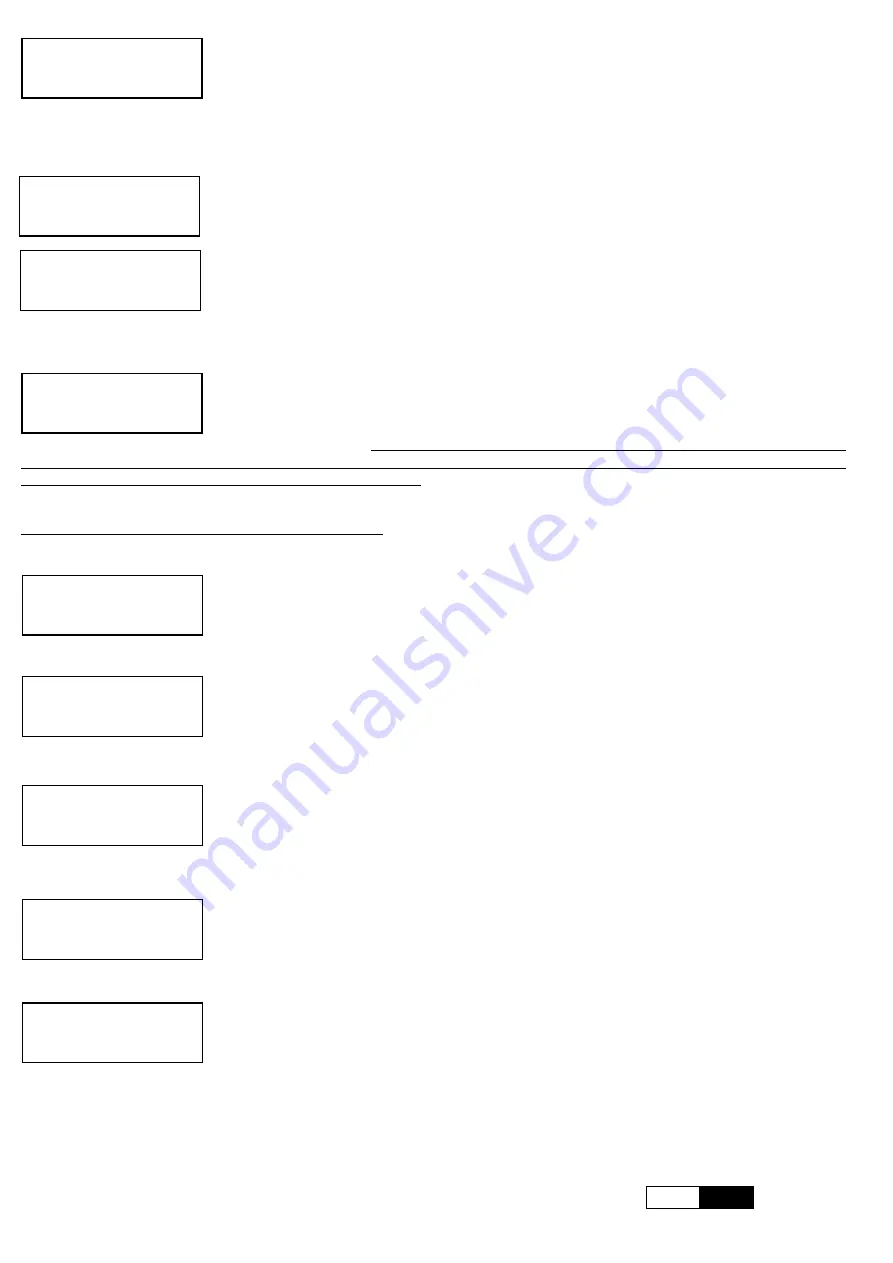
RO
EN
36
1.3 - Stop frequency:
this parameter defines the minimum frequency value, below which the motor is
stopped. During regulation, if the set point pressure value is reached and the motor frequency is below
this value, the inverter attempts to stop the pump (the motor frequency is decreased to the value set in
parameter 1.2 Minimum Frequency). If all utilities are closed and the pressure remains constant despite
the reduction in rotation speed, the pump is stopped correctly. If the pump does not stop, try to increase this value. Otherwise, in case of
continuous pump cycling, try to lower the stop frequency value. To enable correct execution of the shutdown ramp, the stop frequency
must be at least 5 Hz above the set minimum frequency in parameter 1.2.
1.4 - Nominal motor frequency
:
depending on which motor is running, it is possible to select the
maximum inverter output frequency (50 or 60 Hz). Caution: an incorrect selection of the maximum
frequency may cause damage to the pump; consult the manufacturer's technical data carefully.
1.5 - Switching frequency:
set the frequency of inverter switching. The selectable values are 3, 5 and 10
kHz. Higher switching frequency values may reduce the noise of the inverter and allow a more fluid
regulation of the motor but may cause increased temperatures in the electronic board, an increase in
electromagnetic disturbances and potential damage to the electric motor (especially with long cables).
Low switching frequency values are recommended for medium-large pumps, where there is a long distance between the inverter and motor
or high ambient temperatures.
1.6 - Frequency correction:
this parameter enables entry of a deviation, positive or negative, of the
maximum frequency compared to the set nominal value. It may be useful to set a negative deviation (down
to –5Hz) where a limit to the maximum power of the electric pump is wanted and to avoid possible
overload. A positive increase (up to +5Hz) may instead be necessary when a slightly higher electric pump
performance is required. While no particular precautions exist in lowering the maximum frequency, its
increase must be carefully evaluated after having consulted the manufacturer of the electric pump and taking into consideration the
maximum current supported by the inverter and the electric motor.
GROUP 2 : MULTIPLE OPERATION PARAMETERS
2.0 – Serial address
: in the case of single installations with a single pump, leave this value at 1. If a
pressurisation unit with multiple pumps is installed, set the number of the device in the serial bus from 1
to 8. The value must correspond to the setting of the dip-switch on the I/O board, as explained in the
paragraph on electrical connections. Each device must have a different serial address number to be
separate from the others.
2.1 – Pressure sensor serial address
: in the case of single installations with a single pump, leave this
value at 1. If a pressurisation unit with multiple pumps is installed, set the number of the device to which
the pressure sensor and any other auxiliary inputs are connected.
The value must be the same for all devices to ensure that only one pressure sensor transmits the signal to
all inverters.
2.2 – Auxiliary pump
:
Nettuno
can be connected to an auxiliary pump at fixed speed via one of the relays
on the I/O board. The auxiliary pump is started up when the maximum frequency is reached and the
pressure is below the set point. To enable the auxiliary pump function, proceed as follows:
- deactivate multiple operation by setting parameter 2.5 to OFF
- set parameters 3.4 or 3.5 to “AUX” to associate the auxiliary pump function with one
of the output relays.
2.3 – Partner activation delay
: this defines the delay before Nettuno activates the auxiliary pump or
requests intervention of a partner inverter when the maximum frequency is reached. Increase this delay
interval if too many consecutive start-ups occur at close intervals of the auxiliary pump or partner inverters
in the case of high speed pressure transients in the system. Reduce the parameter to increase the speed of
intervention of the partner device or pilot pump on increase of water demand.
2.4 – Timed master changeover
: when using pressurisation units with multiple pumps, it is possible to
implement timed master changeover, where, together with pump shut-down, the master is also changed
over every 60 minutes of continuous operation. In this way, in systems where collection is continuous
and the stop condition for all pumps is never reached, the correct changeover of master devices is still
guaranteed.
1.3 Stop motor
freq. 31 Hz
1.4 Motor rated
freq. 50 Hz
1.5 Switching
freq. 5 KHz
1.6 Frequency
corr. 0 Hz
2.1Press. Sensor
ser.address 1
2.0 Serial
Address 1
2.2 Auxiliary
pump OFF
2.3 Partner act.
delay 2.0 sec
2.4 Timed master
Swapping OFF