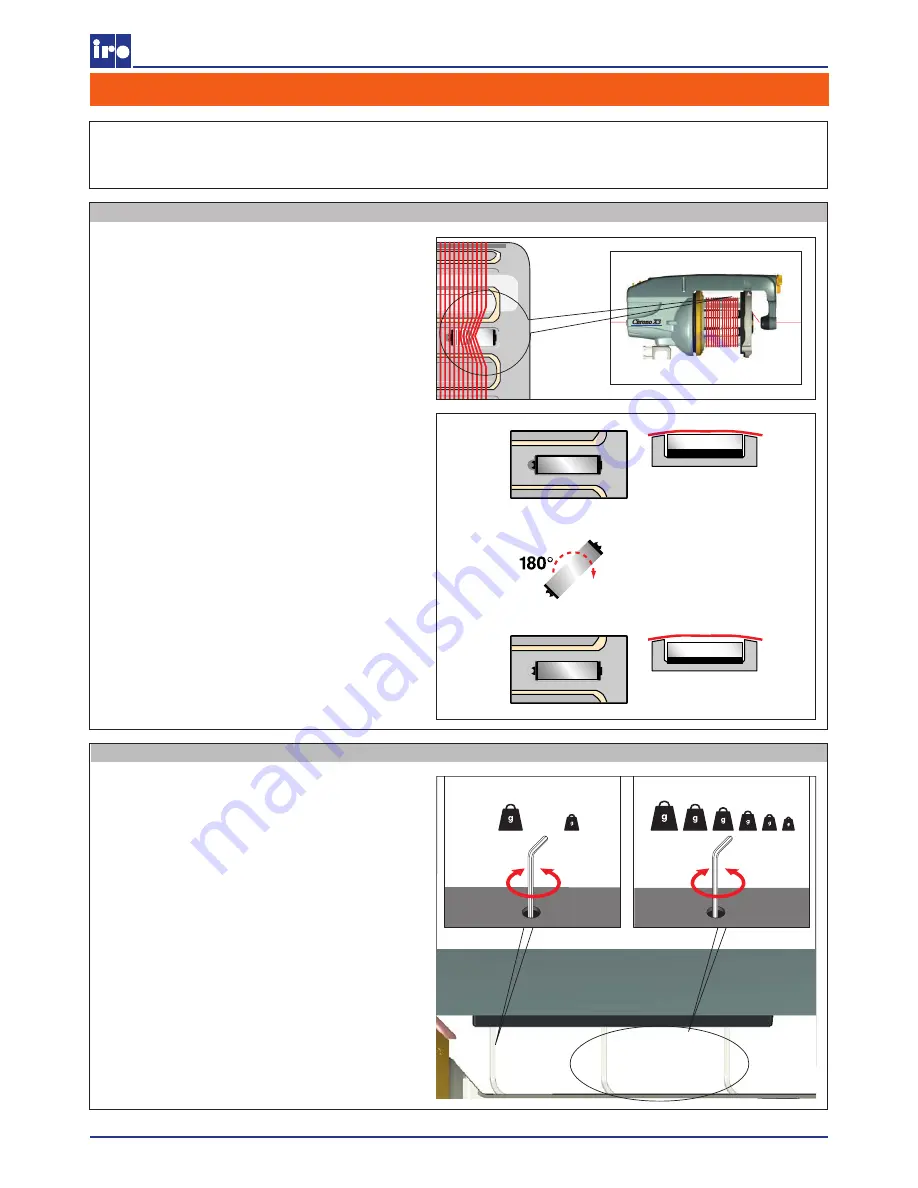
26
+ –
+ –
Luna X3, Chrono X3, XD X3, XD X3 Plus
Ref. no. 40-8939-2001-04/1712
Optical sensors
2. Certain yarn types may stick to, or leave deposits
on, the sensor mirror. In such cases the clearance
between the yarn and the mirror can be increased.
3. Adjust the clearance by rotating the mirror
180 degrees.
Normal Position
Mech. sensor
2. Certain yarns may cause excessive vibration of
the sensors. This can be remedied by increasing
the damper pressure.
Yarn break sensor
Yarn store sensors
Increased clearance
Sensor adjustment
1. Ensure that the spoolbody sensor part is in the correct position