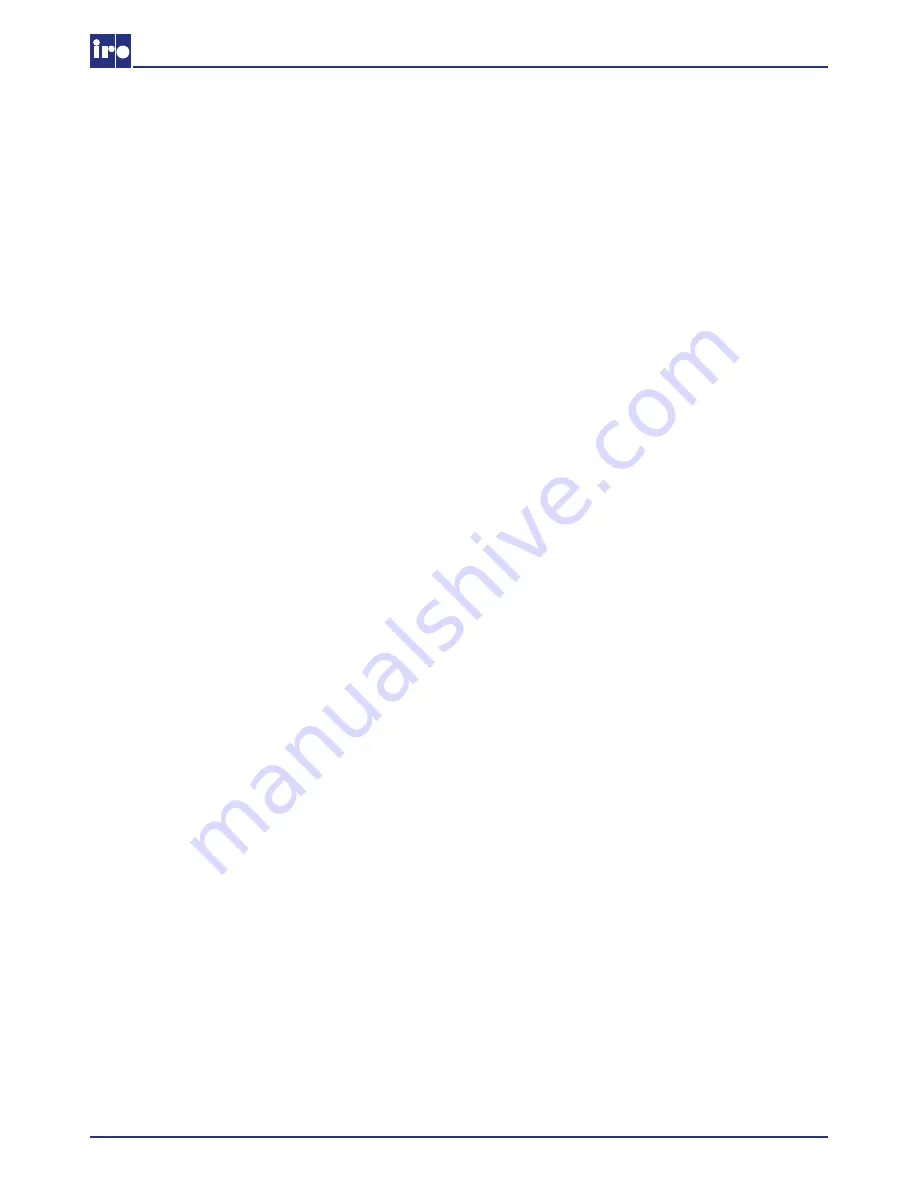
10
Ref. no. 31-8939-0201-05/1805
1131 X2
System Orientation
SYSTEM
The system consists of feeders, cables to each feeder, interface
control box, PTU (pneumatic threading up),
input yarn tensioners and external accessories such as bobbin
break sensors and bobbin change detectors.
INTERFACE
This control box handles all communication between feeders
and machine via the CAN-bus system.
The control box also distributes 290 VDC and 24VDC from the
machine to each feeder.
FEEDER
The feeder consists of:
• Motor and control unit
• Spool body with 4 independently adjustable finger pairs
• Pick length control stopper magnet
• Yarn store sensor
• Positioning sensor
• Winding sensor
• Bobbin break sensor
Spool body circumference, yarn store size and stopper
unit are mechanically adjusted on the feeder.
All other settings are carried out on the weaving
machines terminal and transmitted to the feeder through
the CAN bus.
The permanent magnet motor is controlled from the
control board situated under the top cover.
At feeder start-up, the number of windings on the spool
body is controlled by the yarn store sensor which
indicates the outer limit of the yarn store. The number of
windings supplied to the yarn store is continuously
counted by the wind-on sensor whilst at the same time
the number of windings removed from the yarn store
is counted by the winding sensor. For optimal regulation
the pattern information is transferred to each feeder
a few picks in advance.
The weft length is equal to the spool body circumference
multiplied with number of windings removed
during one insertion. The stopper magnet pin is opened
at a requested machine-angle by reading the anglebus
and closed directly after the second last winding sensor
pulse. The stopper magnet is driven in both directions
electrically, but held in closed position after the power is
switched off.