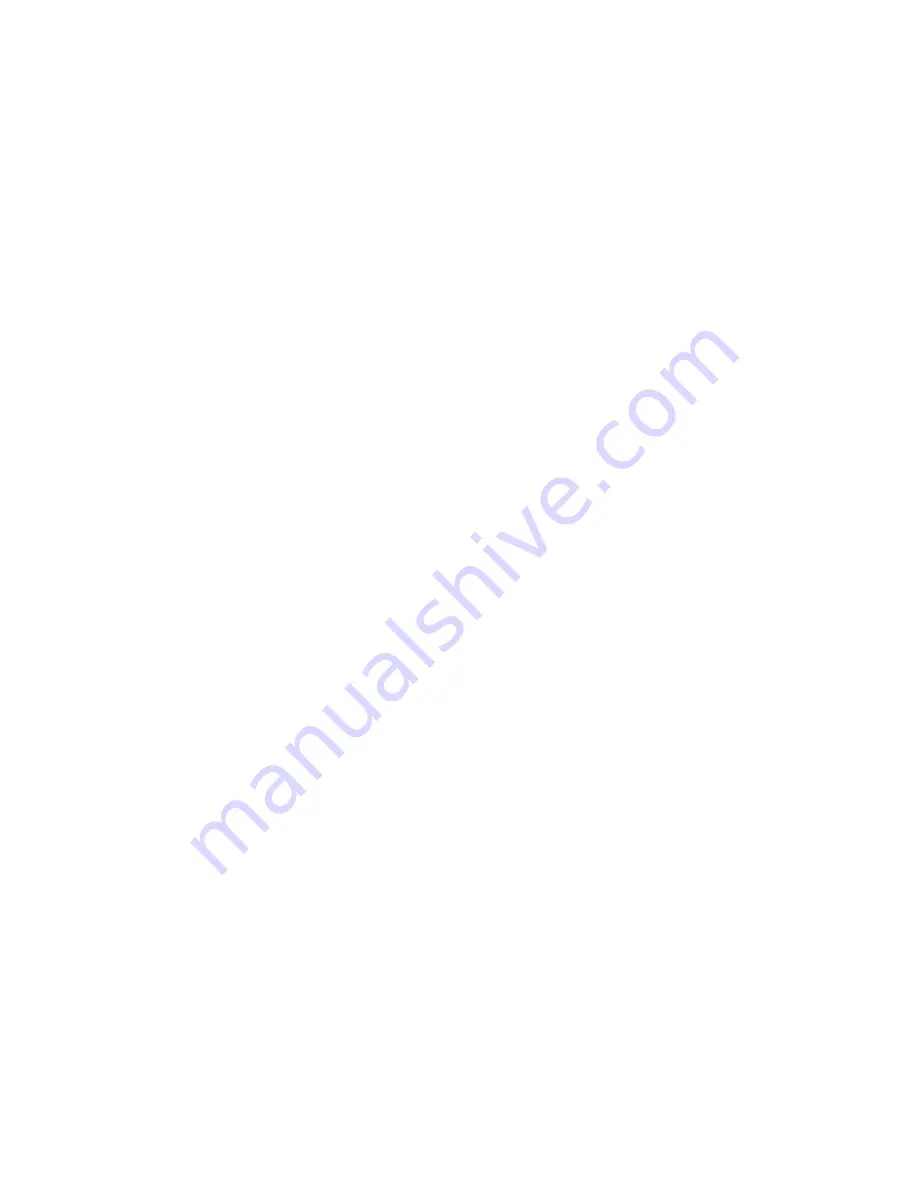
IM483H/IM805H Rev. R032206
18
19
IM483H/IM805H Rev. R032206
M i c r o s t e p S e l e c t ( M S E L ) I n p u t s
Another unique feature of the IM2000 is the ability to change resolutions at
any time. A resolution change can occur whether the motor is being clocked or
is at rest. The change will not take place until the rising edge of the next STEP
CLOCK input. At this time, the new resolution is latched and implemented
before the step clock pulse takes effect.
If a resolution is chosen such that the sine/cosine output of the IM2000 would
not land on an electrical fullstep of the motor, then the IM2000 will auto-
matically align itself to the full step position on the step clock pulse that would
have caused the motor to rotate past the full step. The step clock pulses, from
that point forward, will be equal to the selected resolution. This feature al-
lows the user to switch resolutions at any time without having to keep track of
sine/cosine location. Now the On-Full-Step output of the IM483H/IM805H can
easily be used to monitor position.
Interface guidelines and settings for the Microstep Resolution inputs are lo-
cated in Section 7 of this document,
Interfacing to the IM483H/IM805H.
S t e p p i n g
The IM2000 contains a built-in sine/cosine generator used for the generation of
Phase A and Phase B position reference. This digitally encoded 9 bit sine and 9
bit cosine signal is directly fed into a digital to analog converter.
The step clock (SCLK) and direction (DIR) inputs are buffered using Schmidt
triggered buffers for increased noise immunity and are used to increment or
decrement the sine/cosine position generator. The position generator is updated
on the rising edge of the step clock input. It will increment or decrement by the
amount specified by the microstep resolution select (MSEL) inputs.
The direction (DIR) input determines the direction of the position generator
and hence the direction of the motor. The DIR input is synchronized to the
SCLK input. On the rising edge of the SCLK input the state of the DIR input
is latched in. The position generator will then look to see if there has been a
change in direction and implement that change before executing the next step.
By utilizing this method to implement the direction change, the noise immunity
is greatly increased and no physical change in the motor occurs if the direction
line is toggled prior to the step clock input.
The enable/disable input does not effect the step clock input. The sine/cosine
generator will continue to update if a signal is applied to the step clock input.
The IM2000 outputs both sine and cosine data simultaneously when applying a
step clock input. Dual internal look-up tables are used to output a unique posi-
tion for every step clock input to enhance system performance.