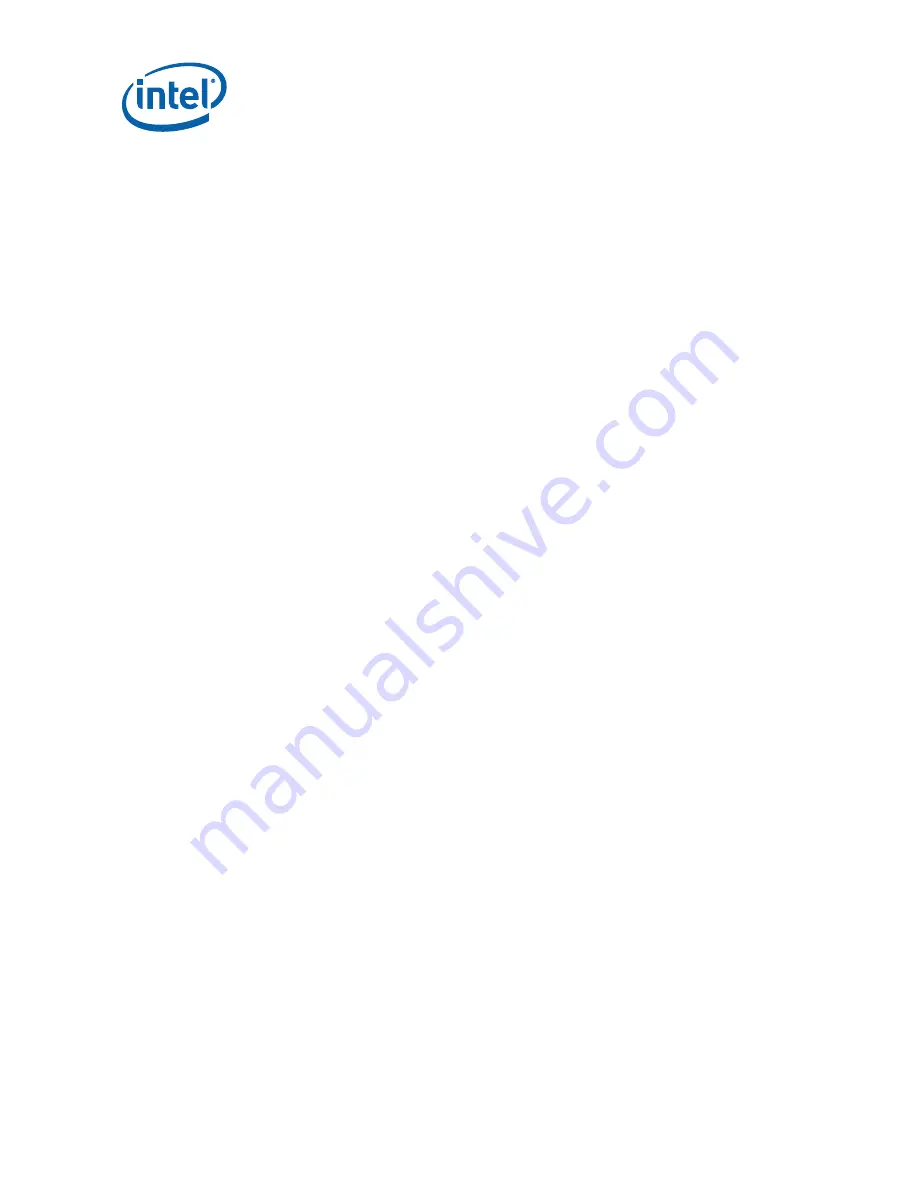
LGA775 Socket Heatsink Loading
14
Thermal and Mechanical Design Guidelines
The primary function of the IHS is to transfer the non-uniform heat distribution from
the die to the top of the IHS, out of which the heat flux is more uniform and spread
over a larger surface area (not the entire IHS area). This allows more efficient heat
transfer out of the package to an attached cooling device. The top surface of the IHS
is designed to be the interface for contacting a heatsink.
The IHS also features a step that interfaces with the LGA775 socket load plate, as
described in LGA775 Socket Mechanical Design Guide. The load from the load plate is
distributed across two sides of the package onto a step on each side of the IHS. It is
then distributed by the package across all of the contacts. When correctly actuated,
the top surface of the IHS is above the load plate allowing proper installation of a
heatsink on the top surface of the IHS. After actuation of the socket load plate, the
seating plane of the package is flush with the seating plane of the socket. Package
movement during socket actuation is along the Z direction (perpendicular to
substrate) only. Refer to the LGA775 Socket Mechanical Design Guide for further
information about the LGA775 socket.
The processor package has mechanical load limits that are specified in the processor
datasheet. The specified maximum static and dynamic load limits should not be
exceeded during their respective stress conditions. These include heatsink
installation, removal, mechanical stress testing, and standard shipping conditions.
•
When a compressive static load is necessary to ensure thermal performance of the
thermal interface material between the heatsink base and the IHS, it should not
exceed the corresponding specification given in the processor datasheet.
•
When a compressive static load is necessary to ensure mechanical performance, it
should remain in the minimum/maximum range specified in the processor
datasheet
•
The heatsink mass can also generate additional dynamic compressive load to the
package during a mechanical shock event. Amplification factors due to the impact
force during shock must be taken into account in dynamic load calculations. The
total combination of dynamic and static compressive load should not exceed the
processor datasheet compressive dynamic load specification during a vertical
shock. For example, with a 0.550 kg [1.2 lb] heatsink, an acceleration of 50G
during an 11 ms trapezoidal shock with an amplification factor of 2 results in
approximately a 539 N [117 lbf] dynamic load on the processor package. If a
178 N [40 lbf] static load is also applied on the heatsink for thermal performance
of the thermal interface material the processor package could see up to a
717 N [156 lbf]. The calculation for the thermal solution of interest should be
compared to the processor datasheet specification.
No portion of the substrate should be used as a load- bearing surface.
Finally, the processor datasheet provides package handling guidelines in terms of
maximum recommended shear, tensile and torque loads for the processor IHS relative
to a fixed substrate. These recommendations should be followed in particular for
heatsink removal operations.
Содержание QX68000 Core 2 Extreme
Страница 30: ...LGA775 Socket Heatsink Loading 30 Thermal and Mechanical Design Guidelines...
Страница 74: ...Heatsink Clip Load Metrology 74 Thermal and Mechanical Design Guidelines...
Страница 76: ...Thermal Interface Management 76 Thermal and Mechanical Design Guidelines...
Страница 96: ...Case Temperature Reference Metrology 96 Thermal and Mechanical Design Guidelines...
Страница 108: ...Legacy Fan Speed Control 108 Thermal and Mechanical Design Guidelines...
Страница 112: ...BTX System Thermal Considerations 112 Thermal and Mechanical Design Guidelines...